1.Casting Structural Characteristics
As a flat casting, the cushion block is the main structural component of automotive driving equipment and plays the role of vibration reduction.The castings are subject to alternating mechanical impact loads during service and therefore require high strength.According to its technical requirements, the castings must not have defects such as cold insulation, cracks, shrinkage holes and shrinkage. Considering the small size of several small holes on the castings, they are not cast.The contour size of pad is 259 mm x 179 mm x 102 mm, the maximum wall thickness is 18 mm, the average wall thickness is 8.8 mm, the minimum wall thickness is 8 mm, and its net weight is 7.4 kg.
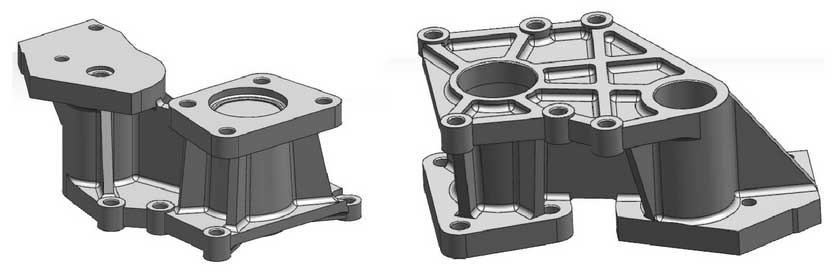
The overall structure of the pad is relatively symmetrical, and it contains more porous and grooves. There are two cylindrical cavities in the pad, and there are 9 reinforcing ribs around the two cylindrical cavities, which protect and seal the periphery of the castings. The thickness of reinforcing ribs is 8 mm.A three-dimensional model of the pad is shown in the figure.
2.Casting material selection
Gaskets are mainly used in the automotive field, which need to meet the requirements of shock absorption, and the accuracy of internal two-cylinder cavity part is required higher.Casting material selection QT450-10, and use Cupola-Induction electric furnace duplex smelting furnace to melt it.
The casting is produced by sand casting, one box and two pieces.Gaskets are produced in small batches and medium scales. According to the structural characteristics of the castings, the complex internal structure can not be made by using machine-shaped coring. Therefore, manual molding and coring are chosen.The casting is ductile iron. Self-hardening resin sand is used as the molding material for sand and core. The raw sand is silica sand and the sand for core making is furan resin self-hardening sand.