1. Working principle of the first mock examination double cavity aluminum piston casting mold assembly
External mold I and external mold II are limited to split and close movement on the table top of the operating platform. When assembling the mold, the two are joined together, and the split surface is the vertical parting surface. Core mold I and core mold II are installed on the core mold fixed base of the CNC hydraulic traction mechanism fixed on the bench. The top mold is placed on the cavity of the outer mold I and the outer mold II. During casting, the top mold maintains gravity on the top. During demoulding, the piston rod of the hydraulic cylinder moves in reverse direction, the top mold moves upward from the outer mold cavity, the core mold moves downward, and finally the outer mold and the pinhole mold are pulled to the initial position to complete the demoulding process.
2. Original technology of the first mock examination double cavity aluminum piston casting mold components.
There is no separation process after the original technology external mold is processed as a whole, and the external mold dual cavity is a whole. The advantages of this structure are that the external mold is simple to manufacture, and the disadvantages are that the external mold does not expand independently to the left and right sides with the center axis of the cavity as the center when contacting the aluminum liquid during the casting process, but expands laterally to the left and right with the center between the two cavities as the center. The left and right lateral thermal expansion value of the double chamber is about 0.5-0.7 mm. However, the core mold I and core mold II are installed and fixed on the “core mold fixed base”, which is a whole and does not directly contact the aluminum liquid, and is subject to small heat. Therefore, the core mold I and core mold II are expanded laterally from the center of the two molds, and the horizontal thermal expansion value is not more than 0.1 mm. Because the value of the left and right lateral expansion of the integral outer mold with the center between the two cavities as the center exceeds the value of the left and right lateral thermal expansion of the core mold I and core mold II fixed on the “core mold fixed seat” with the center of the two molds as the center, the radial wall thickness difference of the aluminum piston blank skirt is difficult to avoid.
As the power manufacturers put forward higher requirements for the quality of aluminum piston, if the wall thickness difference of aluminum piston blank exceeds 0.15 mm, the casting is unqualified. It can be said that there is no separation process for the external mold. It is not a the first mock examination double cavity casting with the central axis of the cavity as the center, which expands independently to the left and right. The radial wall thickness difference of the aluminum piston blank skirt is inevitable and unavoidable.
3. Technical improvement plan for the first mock examination and double cavity aluminum piston casting mold components
In the aluminum piston casting industry, because there is no separation process after the overall processing of the original external mold, the horizontal thermal expansion value of the overall external mold exceeds the horizontal thermal expansion value of the “core mold fixed seat”, it is difficult to solve the problem of radial wall thickness difference of the skirt of the the first mock examination double cavity aluminum piston blank. This problem has long puzzled the casting technicians. This technology solves this problem on the mold components.
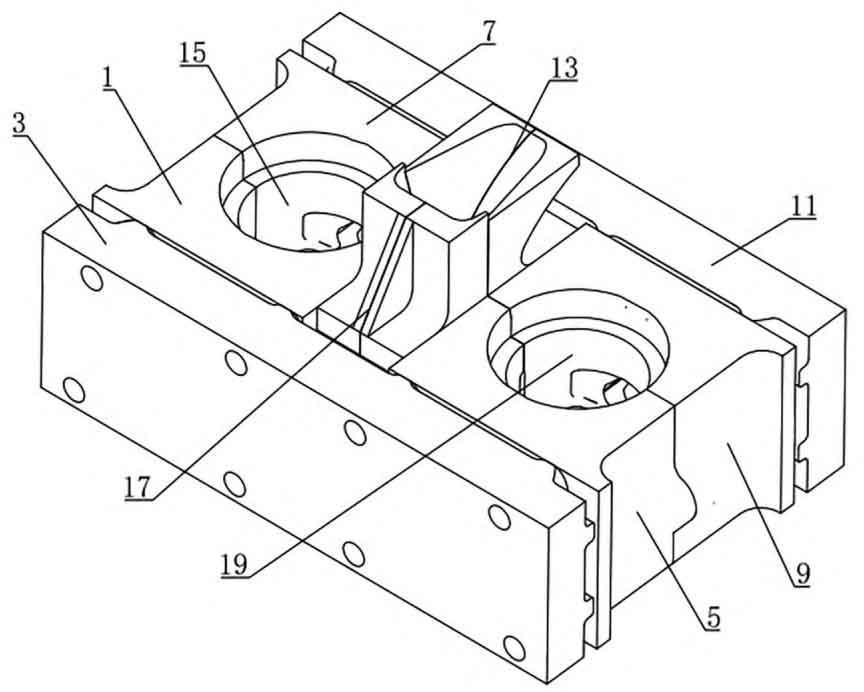
9 The fourth half cavity external mold; 11 Connecting plate II; 13 Normal temperature clearance of external mold II; 15 External model cavity I;
17 Normal temperature clearance of external mold I; 19 Outer model cavity II
In 2021, the Chinese invention patent published the title of “Improved Structure of Mold Assembly for Greatly Improving the Casting Precision of Lightweight Aluminum Piston” (Bulletin No.: CN111421114B) (invented by the author), which uses the above the first mock examination double cavity mold assembly structure. The disadvantage is that the thickness difference between the maximum and minimum radial thickness of the cast aluminum piston skirt is large, It can not meet the requirements of high-precision casting in the industry. In the industry, the H13 die steel double cavity external mold assembly with a length of 350 mm, a height of 100 mm and a thickness of 90 mm is generally used. The problem of large radial thickness difference of the cast aluminum piston blank skirt of the the first mock examination double cavity mold assembly has not been solved, and the maximum radial difference of the cast aluminum piston blank skirt is 0.3 mm. See Fig. 1, Fig. 2, Fig. 3 and Fig. 4 for the technical improvement description of mold components. The left and right sides of Figure 5 show the aluminum piston blanks cast in two cavities after technical improvement. Figure 6 shows the sectional diagram of the finished double-chamber cast aluminum piston after technical improvement.
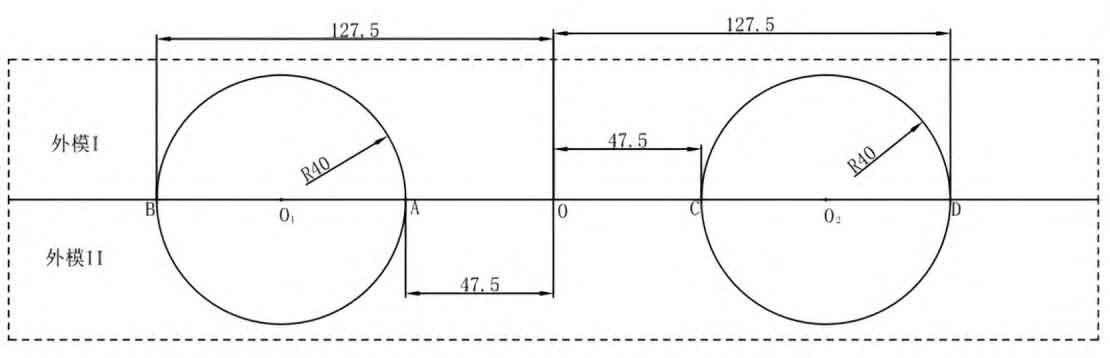
The nearest point between the I wall of the model cavity outside A and O; The farthest point of the wall I of the model cavity outside B from O;
Center point of model cavity II outside O2; The nearest point of the second wall of the model cavity outside C to O;
The farthest point from the outer model cavity II wall to O
The specific implementation mode of the technology: the technology is made of H13 mold steel material. The existing technology has an outer dimension of 350 mm long, 100 mm high and 90 mm thick for the outer mold I or outer mold II, a semicircle diameter of 70 to 80 mm for the inner cavity, and a working temperature of 300 ± 20 ℃. Linear expansion coefficient of H13 die steel material between 20 ℃ and 300 ℃ α= 11.5 * 10-6 ℃ – 1, therefore, the elongation of external mold I or II rises from normal temperature or room temperature (about 20 ℃) to the working temperature Δ L= α L Δ T=11.5*10-6*350mm*(300-20)=1.127mm。 That is to say, during this temperature change, the outer mold I or the outer mold II extend about 0.6 mm from the transverse center point O of the outer mold I and the outer mold II to both ends. The distance between the farthest point B of the outer model cavity wall I and the nearest point A of the outer model cavity wall I and O, and the distance between the farthest point D of the outer model cavity wall II and the nearest point C of the outer model cavity wall II and O are both 0.6 elongation of the outer model cavity size/175, taking the 80 mm cavity as an example, The movement is equal to 0.6 * 80/175 ≈ 0.3 mm. At normal temperature, the core mold is inserted in the mold cavity, and the vertical centerline passes through O1 or O2 point. The central line of the core mold can remain unchanged during the thermal expansion, so the skirt of the cast aluminum piston blank will be thicker in the radial direction away from the transverse center point O of the external mold I and II, with a thickness difference of 0.3 mm.
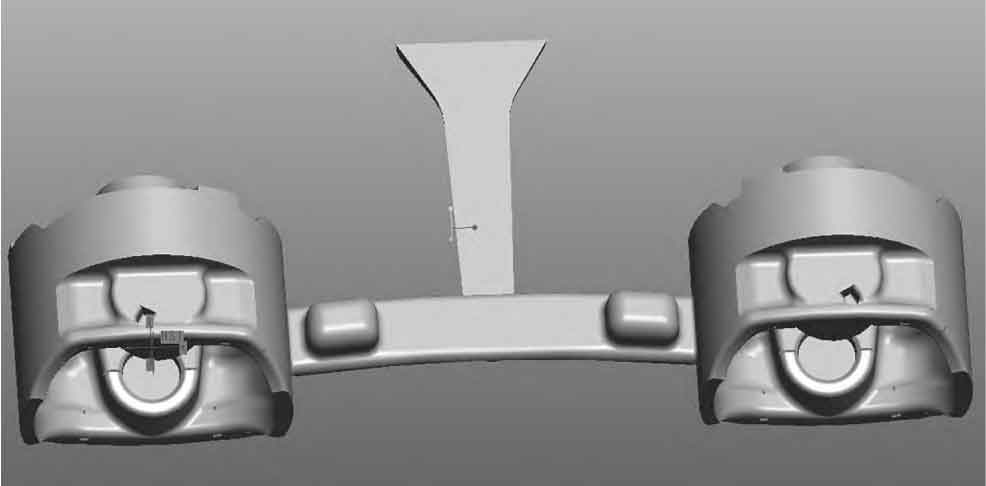
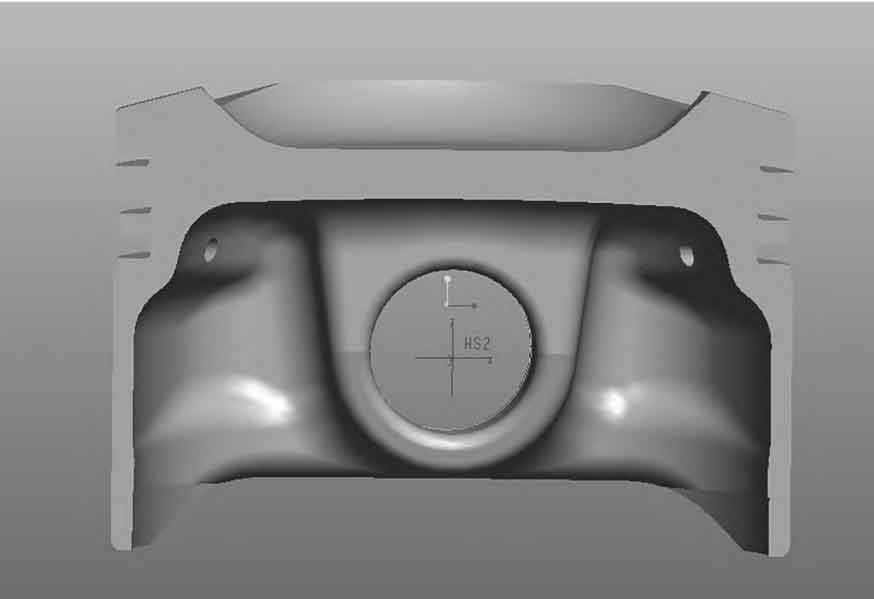
In order to eliminate the radial thickness difference of the skirt of the cast aluminum piston blank, the improvement of this technology is that the first half cavity outer mold (1) and the second half cavity outer mold (5) are fixed on the surface of the connecting plate I (3) by screws, the two are horizontally aligned, and the normal temperature clearance (17) of the outer mold I is reserved between the adjacent end faces. The third half cavity external mold (7) and the fourth half cavity external mold (9) are fixed on the surface of the connecting plate II (11) by screws, and the two are horizontally aligned. The normal temperature gap (13) of the external mold II between the adjacent end faces is 0.3mm. The room temperature gap of the external mold refers to the gap at room temperature or room temperature. It is not necessary to consider the influence of the actual room temperature difference in different seasons on the gap requirements during production, and the gap width is preset to 0.3 mm. The two cavities of the outer mold I and the outer mold II are closed due to the expansion of the mold material at the working temperature with a normal temperature gap of 0.3 mm, which does not affect the flow of the casting liquid in the runner. This technology (external mold I, external mold II), together with the top mold, core mold I, core mold II, pin hole mold I, pin hole mold II, and the mouth locking fixing seat, forms the mold component of the first mock examination with two cavities. When in use, install them on the workbench together with them, and follow the normal operation. The first half cavity outer mold, the second half cavity outer mold, the third half cavity outer mold, and the fourth half cavity outer mold are all thermally expanded around the center of the center line of the cavity. Because the center line of the core mold coincides with the center line of the cavity, the radial thickness of the cast aluminum piston blank skirt is uniform, which overcomes the existing external mold I The two cavities of the external mold II are connected integrally with the external mold, and the thermal expansion of the center line of the conical runner in the vertical section around causes the defect that the center line of the cavity and the center of the core mold cannot be kept coincident under the working temperature, which eliminates the radial thickness difference of the casting aluminum piston blank skirt caused by this defect. The external mold of this technology does not expand left and right with the center between the two cavities as the center when heated, but with the central axis of the cavity as the center, and expands to the left and right independently, so as to ensure that the central axis of the aluminum piston inner core mold and the central axis of the aluminum piston outer casting cavity are on the same central axis when casting the aluminum piston blank, and the transverse thermal expansion values of the two cavities of the external mold are consistent with the transverse thermal expansion values of the two “core molds”, (As shown in Figure 5) Ensure that the radial wall thickness difference of the skirt of the cast aluminum piston blank is within 0.05 mm. This fundamentally solves the problem of the radial wall thickness difference of the skirt of the cast aluminum piston blank caused by the inconsistency between the transverse thermal expansion values of the two cavities of the outer mold and the transverse thermal expansion values of the two “core molds” when casting the aluminum piston blank, (as shown in Figure 6) to ensure that the radial wall thickness difference of the skirt of the finished aluminum piston is within 0.05 mm after the aluminum piston casting blank is processed into the finished aluminum piston.