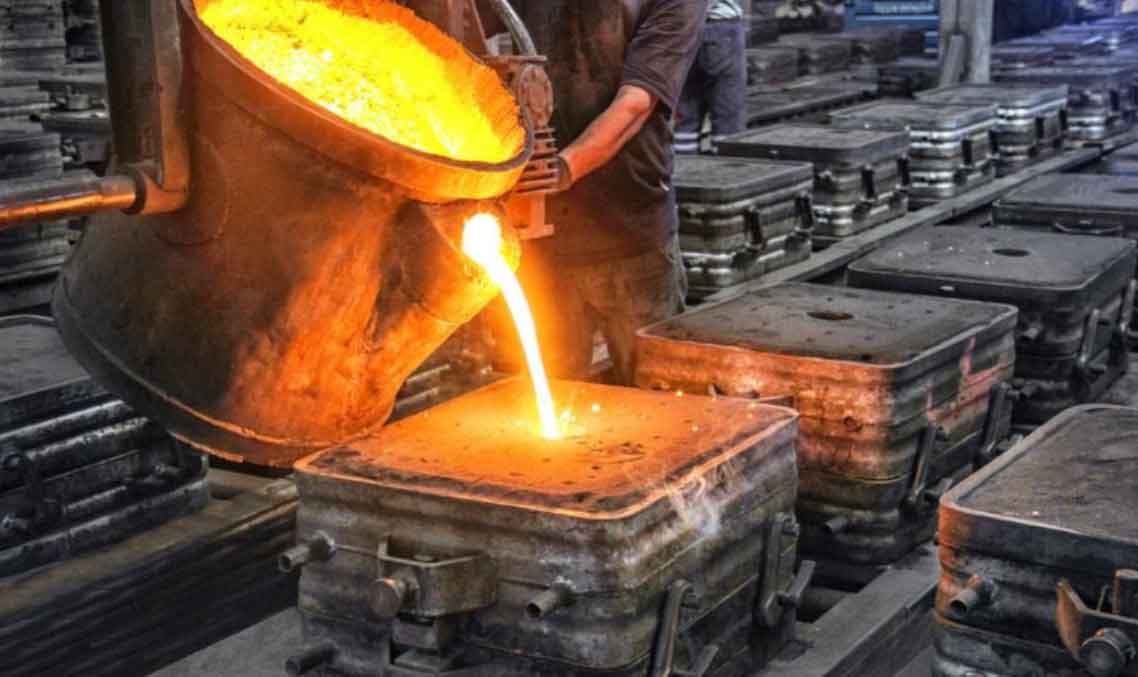
Sand casting services offer several advantages and have some limitations in the manufacturing process. Let’s explore them in detail:
Advantages:
- Cost-Effective: Sand casting is a cost-effective method for producing metal components, especially for low to medium volume production. The initial tooling and setup costs are relatively low compared to other casting methods.
- Versatility: Sand casting services can accommodate a wide range of part sizes and shapes, making it suitable for producing both small and large components with complex geometries.
- Complexity: Sand casting allows the production of intricate and complex designs, including internal cavities and undercuts, which may be challenging with other manufacturing methods.
- Wide Material Selection: Sand casting supports a broad range of materials, including various types of metals and alloys, enabling the production of components with diverse properties.
- Short Lead Times: The setup and production process in sand casting can be relatively fast, leading to shorter lead times for producing parts compared to other manufacturing methods.
- No Geometric Limitations: Sand casting does not impose strict geometric limitations, allowing designers and engineers to achieve greater design freedom and flexibility.
- High Heat Resistance: Sand castings exhibit excellent heat resistance, making them suitable for applications requiring high-temperature performance.
Limitations:
- Surface Finish: The surface finish of sand castings is not as smooth as other manufacturing methods, and additional finishing processes may be required to achieve the desired surface quality.
- Tolerance and Dimensional Accuracy: Sand casting may have limitations in achieving tight tolerances and high dimensional accuracy, especially for intricate designs.
- Mold Complexity: Creating the sand molds can be a labor-intensive and time-consuming process, especially for complex designs, which may impact production efficiency.
- Material Properties: While sand casting supports a wide range of materials, certain materials may not be suitable due to their metallurgical properties, limiting the material options for specific applications.
- Mold Wear: The sand molds used in sand casting have a limited number of uses before they need to be replaced, which can add to the production costs.
- Surface Defects: Sand castings may have surface defects like sand inclusions, surface roughness, or mold shift, which can affect the final part quality.
Despite these limitations, sand casting services remain a versatile and widely used method in manufacturing due to their ability to produce a variety of components in a cost-effective manner. They are particularly well-suited for producing larger and complex parts where surface finish and dimensional accuracy are not critical.
Pages: 1 2