Based on the analysis of the structural characteristics and casting process difficulties of a certain equipment’s steel casting guide rail, the initial process of the steel casting was trial-produced and verified. Aiming at the defects such as insufficient pouring, cold shuts, shrinkage holes, shrinkage porosity, and deformation caused by the initial process of the steel casting, the solidification process of the steel casting was simulated and analyzed using the ProCAST three-dimensional numerical simulation software, Based on the simulation and analysis results, improvement measures were formulated. After the process improvement, defects such as insufficient pouring, cold shuts, shrinkage holes, and porosity of the guide rail steel castings produced were well resolved, and the deformation amount was effectively controlled. After processing, the overall structure and dimensions of the guide rail steel castings met the design requirements of the drawings.
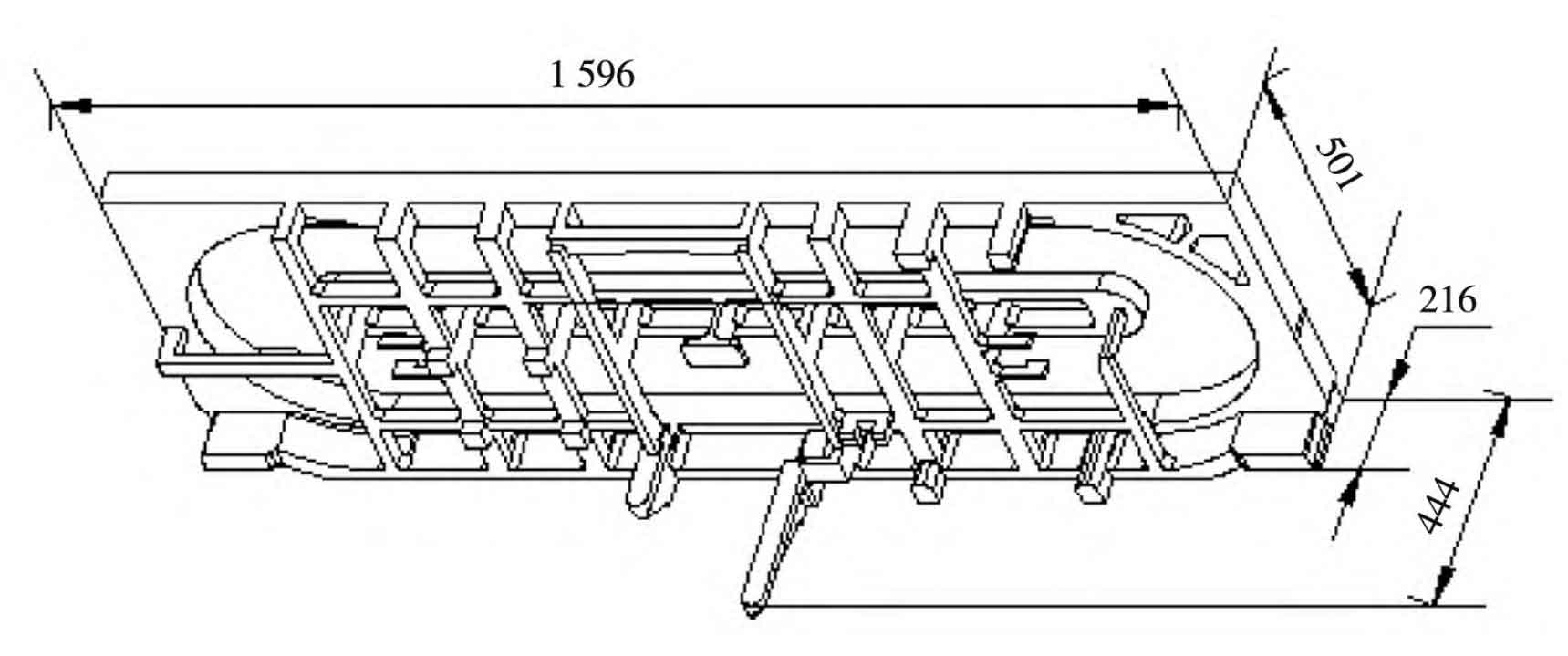
The cast steel guide rail part of an equipment belongs to a typical large-scale frame structure, with large dimensions, complex structures, and high requirements for dimensional accuracy and material internal organization. Using integrated casting and precision machining is an ideal method for achieving efficient mass production of such parts.
Based on the analysis of the structure and material characteristics of the cast steel guide rail parts, a systematic design of the casting scheme was carried out from the aspects of the determination of the pouring position and the selection of the parting surface, the design of the pouring system, the design of the riser parameters, the selection of the pouring temperature, and the control of the shrinkage rate of the steel casting. Through the trial production of the casting process, the relationship between the casting process parameters, the sand mold structural parameters, and the defects of the steel casting was explored, and through simulation and comprehensive optimization, The integrated casting and forming process for large frame castings in sand mold casting and measures to prevent heat treatment deformation have been extracted, solving the difficult problems in the development and production of a certain equipment. The summarized casting process design scheme and casting process parameters have good application and promotion value. This has laid a solid foundation for the company to replace welding with casting for large-scale frame structural parts in the future, and provided a technical reference for the industry to produce large-scale frame structural steel castings.