Testing and certification of gate valve bodies are crucial to ensure their performance, reliability, and compliance with industry standards and regulations. These tests and certifications ensure the safety and functionality of the valves under various operating conditions and provide confidence to end-users in their performance. Below are some of the common tests and certifications for gate valve bodies.
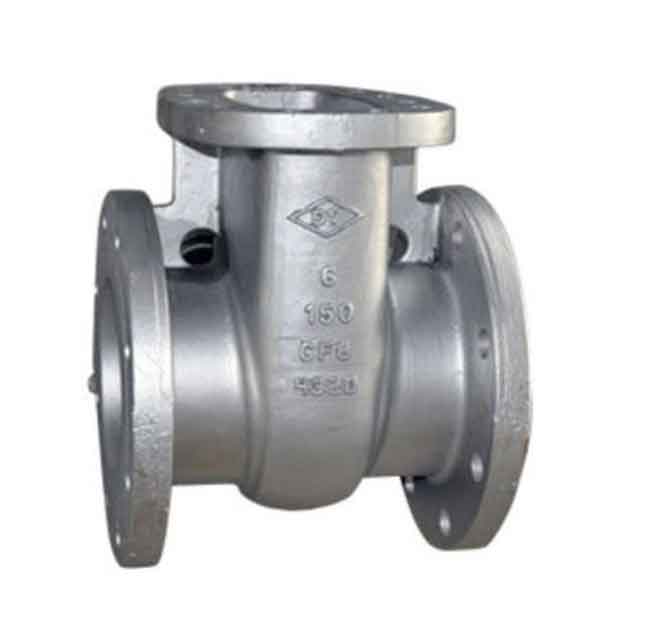
1.Hydrostatic and Pneumatic Tests
Hydrostatic and pneumatic tests evaluate the structural integrity and pressure resistance of gate valve bodies and components. These tests involve filling the valve with a test fluid (typically water or air) and subjecting it to the specified pressure to evaluate its sealing performance, leak-tightness, and resistance to deformation or rupture.
a. Shell Test: The shell test checks for leaks or structural defects in the valve body, bonnet, and flanges under a specified pressure level. The test determines if the components can withstand the pressure without permanent deformation or failure.
b. Seat Test: The seat test examines the sealing performance of the gate and seat under a specified pressure to ensure a leak-free seal. The test pressure is typically lower than the shell test pressure, and any leak rate is measured and compared to an acceptable limit.
c. Backseat Test: The backseat test is performed on valves with a backseat design to verify the sealing performance between the stem and the bonnet and ensure that the design prevents leakage through the stem.
d. Pneumatic Test: The pneumatic test uses air or gas to evaluate the gas-tightness of the valve body or components at a specified pressure and temperature.
2.Functional and Performance Tests
Functional and performance tests are conducted to evaluate the valve’s operability, flow control, and other performance characteristics under different operating conditions.
a. Opening and Closing Torque Test: This test measures the required torque to open and close the valve fully and ensures that the valve operates smoothly within specified torque limits.
b. Cycle Test: The cycle test assesses the valve’s durability and reliability by subjecting it to a predefined number of opening and closing cycles while monitoring its performance and wear.
c. Flow and Pressure Drop Test: This test evaluates the flow characteristics of the valve, such as pressure drop, flow coefficient, and turbulence, under various flow rates and operating conditions.
3.Material and Welding Tests
Material and welding tests are performed on the valve materials, welds, and coatings to ensure their compliance with the specified standards and guidelines. These tests may include chemical composition analysis, mechanical property tests, non-destructive examination, and corrosion resistance tests.
4.Certifications and Compliance
Gate valve bodies must conform to international and national standards and regulations, such as those set by American Petroleum Institute (API), American Society of Mechanical Engineers (ASME), International Organization for Standardization (ISO), and European Pressure Equipment Directive (PED). These organizations provide guidelines, specifications, and certifications on various aspects of gate valve design, manufacture, testing, and performance. It is essential to have the appropriate certifications and ensure compliance with these standards to maintain the quality and integrity of the gate valves.
Testing and certification of gate valve bodies are essential steps in ensuring their safety, performance, and compliance with applicable standards and regulations. Manufacturers must ensure that their gate valves undergo rigorous testing and meet the necessary certification requirements to provide confidence to end-users and maintain the trust and reliability of their products.