1. Structure of nodular cast iron
The structure of the nodular cast iron part of the end cover of the high pressure cylinder is shown in Figure 1. It is mainly composed of end cover body a, oil port b and 14 bolt holes c. The external diameter of the 14 bolts is 157 mm, the maximum wall thickness of the end cover body is 44 mm, the minimum wall thickness is 8 mm, and the mass of the nodular cast iron is 11.2 kg. The wall thickness difference is large. The bolt hole blocks the feeding channel of the nodular cast iron. The nodular cast iron is used for the oil cylinder of the 20-ton hydraulic excavator, and the maximum working pressure reaches 34.3 MPa. Therefore, the requirements for strength, elongation and internal shrinkage of the nodular cast iron are relatively high, After machining, the surface of nodular cast iron parts shall be free of defects such as air holes, sand inclusions, slag inclusions, etc., which will affect the sealing and lead to pressure relief and even oil leakage of high-pressure oil cylinder.
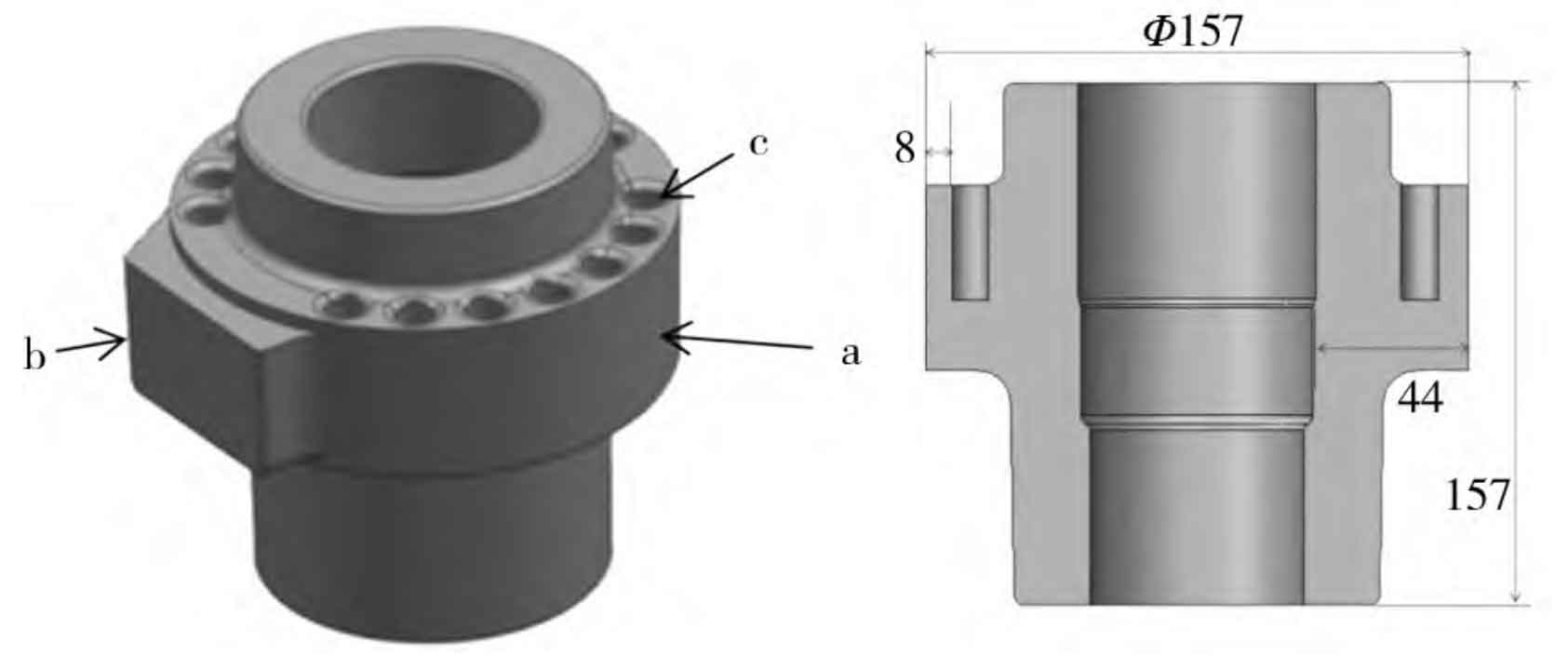
2. Material selection of ductile iron castings
The high pressure cylinder end cover material QT500-7 is ferritic+pearlitic ductile iron, which has the properties of cast iron and steel, and has high strength, good toughness, high elongation and other characteristics. The chemical composition is shown in Table 1.
C | Mn | S | Si | P | Cr | Cu | Mg |
3.6~3.9 | ≤1 | ≤0.025 | 2.0~2.5 | ≤0.07 | ≤0.07 | ≤0.7 | 0.035~0.055 |
3. Test methods for ductile iron castings
The raw materials used in the test are pig iron, scrap steel and furnace feed. After drying a certain proportion of the furnace charge, it is put into the FS60/1T type ABP medium-frequency coreless induction furnace with a capacity of 1 t for smelting. The German ZORC Dual Track Injection Master dual-channel wire feeder is used to automatically feed the wire ball chemical technology and the German KW static pressure molding line. After the wire feeding spheroidization is completed, the FOX 15 type KW SLS fully automatic pouring machine is used for pouring, and the pouring temperature is (1380 ± 10) ℃, Open the box after cooling to 300 ℃, clean the surface of the nodular cast iron after cooling to room temperature, and then conduct internal dissection of the nodular cast iron.