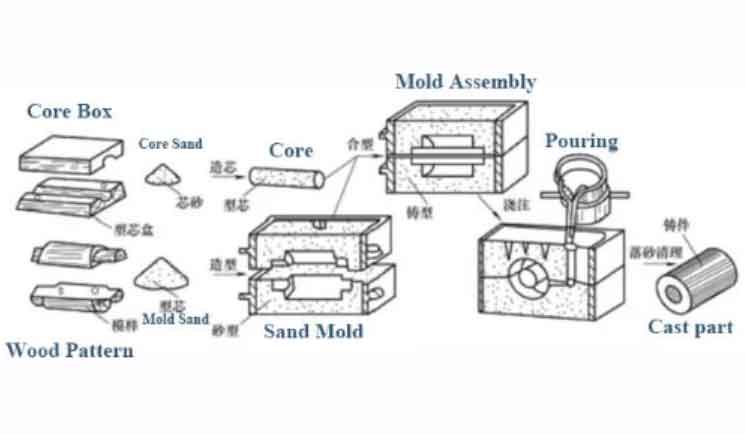
Sand casting is a widely used manufacturing method that offers several advantages for producing parts. Here are some of the key advantages of sand casting:
Versatility:
Sand casting can accommodate a wide range of part sizes, complexities, and materials. It is suitable for both small and large components, from a few ounces to several tons. The process can handle intricate geometries, including internal features and undercuts.
Cost-effective:
Sand casting is generally a cost-effective manufacturing method, especially for low to medium production volumes. The tools and equipment required for sand casting are relatively inexpensive compared to other casting methods like investment casting or die casting. The low-cost materials, such as sand and binders, make it an economical choice for various applications.
Design flexibility:
Sand casting allows for greater design flexibility compared to other casting processes. It can accommodate complex shapes, draft angles, and undercuts without the need for additional features like cores or slides. This flexibility enables the production of parts with intricate details and customized designs.
Material compatibility:
Sand casting can be used with a wide range of metals and alloys, including ferrous and non-ferrous materials. It is suitable for casting materials such as aluminum, iron, steel, brass, bronze, and many others. This versatility makes sand casting applicable in various industries, from automotive to aerospace, agriculture, and beyond.
Short lead times:
Sand casting offers relatively shorter lead times compared to other manufacturing methods like machining or forging. Once the pattern and mold are prepared, the production process can begin promptly. The simplicity of the process allows for faster turnaround times, making it suitable for urgent or time-sensitive projects.
Low tooling costs:
Sand casting typically requires simpler tooling compared to other casting processes. The pattern used to create the mold can be made from various materials, including wood, plastic, or metal. This flexibility in pattern materials helps keep tooling costs relatively low, especially for prototypes or short production runs.
Surface finish and dimensional accuracy:
Sand casting can achieve good surface finishes and dimensional accuracy, especially with proper pattern design and careful molding techniques. With post-processing operations like machining or polishing, the final parts can meet the required specifications and surface quality standards.
Scalability:
Sand casting is highly scalable and can be easily adapted for high-volume production if needed. Multiple molds can be prepared simultaneously, allowing for efficient batch production. The process can be optimized for improved productivity and yield, making it suitable for both small-scale and large-scale manufacturing.
It’s important to note that while sand casting has numerous advantages, it may not be the ideal choice for all types of parts or production requirements. Factors such as part complexity, volume, material properties, and specific industry standards should be considered when selecting the appropriate manufacturing method.