1. Introduction
Lost foam casting, also known as full mold casting, has gained significant popularity in the casting industry due to its numerous advantages such as high dimensional accuracy, near – net – shape forming, and wide process adaptability. It is widely used in the production of automotive parts, machine tool castings, and other products. However, like any manufacturing process, it is not without its challenges. One of the most common and difficult – to – solve problems in lost foam casting is the “coating flakes” slag inclusion defect. This defect not only affects the appearance and dimensional accuracy of the castings but also significantly reduces their mechanical properties, leading to potential product failures. Therefore, in – depth research on the causes and improvement measures of this defect is of great importance for improving the quality of lost foam castings and enhancing the competitiveness of casting enterprises.
2. Overview of Lost Foam Casting Process
2.1 Process Principles
Lost foam casting is a unique casting method that uses a foam pattern, typically made of expandable polystyrene (EPS) or other foam materials. The foam pattern is coated with a special casting coating and then surrounded by dry sand or other molding materials. When molten metal is poured into the mold, the foam pattern vaporizes instantly under the high – temperature action of the molten metal, leaving a cavity for the molten metal to fill. The molten metal then solidifies in the cavity to form the final casting product.
2.2 Advantages and Disadvantages
Advantages | Disadvantages |
---|---|
High – dimensional accuracy, reducing machining allowance | Higher process cost compared to some traditional casting methods |
Near – net – shape forming, saving material and machining time | Prone to various casting defects, such as “coating flakes” slag inclusion defects |
Wide process adaptability, can produce complex – shaped castings | Requires strict control of process parameters |
Simplified molding process, reducing labor intensity | The quality of foam patterns and coatings has a great impact on casting quality |
3. Characterization of “Coating Flakes” Slag Inclusion Defects
3.1 Appearance Characteristics
“Coating flakes” slag inclusion defects usually appear as large – area depressions on the top, side, corners, or confluence positions of castings. These depressions can be in the form of long strips, with lengths ranging from 30mm to 100mm or even more than 150mm, or they can be in the form of blocks, with areas up to 300mm×300mm. Before cleaning, the pits are filled with coating ash, sand, and other debris, as well as large – scale slag visible to the naked eye. (See Figure 1 for defect morphology)
3.2 Impact on Casting Quality
This defect seriously affects the mechanical properties of castings. Experimental data shows that when a casting has “coating flakes” slag inclusion defects, its mechanical properties, such as tensile strength, hardness, and impact toughness, will be significantly reduced. In addition, the presence of these defects can also lead to problems such as poor surface quality and dimensional instability of the castings, reducing the overall quality and performance of the products.
4. Causes Analysis of “Coating Flakes” Slag Inclusion Defects
4.1 Pouring System Design
Pouring System Type | Impact on Defects |
---|---|
Open – type Pouring System | Does not have a good slag – blocking effect. The slag floats on the surface of the molten iron and easily enters the casting with the flow of the molten metal, increasing the risk of slag inclusion defects |
Closed – type Pouring System | The molten iron has a high flow rate after flowing out of the inner gate, which is likely to cause turbulence and splashing of the molten iron, intensifying the oxidation of the molten iron and resulting in secondary slag inclusion |
Semi – closed – type Pouring System | Can prevent and weaken turbulence to a certain extent and has a better slag – blocking effect. However, in lost foam casting, due to the influence of factors such as the gasification speed of the foam pattern, simply adjusting the cross – section of the pouring system components to control the flow rate may not be feasible |
In lost foam casting, an unreasonable pouring system design can cause the molten metal to fill the mold unevenly, leading to the scouring of the coating by the molten metal. This can break the coating and cause “coating flakes” to enter the molten metal, forming slag inclusion defects.
4.2 Coating – related Factors
Coating – related Factors | Impact on Defects |
---|---|
Low – temperature Strength of the Coating | During the drying and molding processes, if the coating has insufficient low – temperature strength, micro – cracks will occur. These micro – cracks can expand during the pouring process under the action of the molten metal, causing the coating to break and fall off, resulting in “coating flakes” slag inclusion defects |
Wettability and Adhesion of the Coating | Foam plastics are non – polar materials, and water – based coatings are not easy to wet and penetrate. If the surfactant added to the coating fails, the wettability and adhesion of the coating will be poor, resulting in uneven coating thickness and even discontinuous coatings. Such coatings are easily washed into the casting by the molten metal, forming defects |
Drying and Baking Process of the Coating | An inappropriate coating formulation or an unsuitable binder can lead to insufficient low – temperature strength of the coating. During the drying process, micro – cracks may occur in the coating due to the inappropriate binder, increasing the possibility of “coating flakes” slag inclusion defects |
4.3 Molding Process
The insufficient compaction of the molding sand cannot provide sufficient support for the coating. During the filling process of the molten metal, the coating is easily broken under the action of the molten metal, resulting in the entry of “coating flakes” into the molten metal and forming slag inclusion defects. In addition, in the lost foam casting process, although the molding operation is simplified, the requirements for the molding process are not reduced. For some reverse – hand holes and other structures, if they are not filled tightly, the strength of the sand mold will be insufficient, which cannot effectively support the coating.
4.4 Product Structure
For products with complex structures, such as some mold base products with “I” – shaped or “Ji” – shaped structures, the flow state of the molten metal during the filling process is complex. At the positions where the cross – section of the molten metal flow changes suddenly, such as the intersection of the bottom flange and the rib plate, the flow rate of the molten metal will change suddenly. This can lead to the occurrence of phenomena such as turbulence and pressure loss of the molten metal, causing the coating to be damaged and resulting in “coating flakes” slag inclusion defects.
5. Iron – Filling Characteristics in Full – Mold Casting
5.1 Filling Pattern
In traditional cavity casting, the molten metal fills the mold from the bottom in a relatively regular way under the action of gravity. However, in full – mold casting, the flow of the molten metal is affected by the gasification and retreat of the foam plastic pattern. The flow of the molten metal is multi – dimensional and multi – directional, and it changes with the structure of the pattern and the gas pressure. Taking the bottom – return inner gate as an example, the molten metal diffuses and fills in all directions such as upward, left – right, and front – back. It is more affected by gas resistance than gravity. In the filling process, the pattern gradually disappears as the molten metal rises until the entire cavity is filled with molten metal. This filling mode is called pulsating filling of molten metal.
5.2 “Pressure Loss” Phenomenon
In the full – mold casting process, the iron – filling process is accompanied by the “pressure loss” phenomenon. When the cross – section of the molten metal flow changes suddenly, such as when it becomes smaller, the flow rate of the molten metal increases sharply, resulting in intensified turbulence of the molten metal, which is likely to entrain slag and gas. When the cross – section suddenly becomes larger, the flow rate of the molten metal decreases suddenly, and the gas gap in front of the molten metal is in an unbalanced state, showing an instantaneous pressure – loss state. This may cause the coating in this area to fall off under the scouring of the molten metal, and at the same time, the bubbles and slag entrained in the molten metal will gather here, increasing the risk of “coating flakes” slag inclusion defects.
6. The Role of Coatings in Lost Foam Casting
6.1 Required Functions
Required Functions | Explanation |
---|---|
Good Permeability | The pyrolysis products of the foam plastic should be able to escape from the cavity smoothly through the coating |
Low Gas Evolution | After the coating is dried and comes into contact with the molten metal poured into the cavity, it should not produce additional gas, which may cause the coating to fall off and affect the smooth filling of the molten metal |
Easy to Peel and Sinterable | It is conducive to the shake – out of the casting and subsequent cleaning |
Good Wettability and Adhesion | Since foam plastics are non – polar materials and are not easy to be wetted and penetrated by water – based coatings, surfactants are added to the coating to improve its wettability and adhesion |
Sufficient Strength | At room temperature, it can improve the strength and stiffness of the foam pattern to prevent damage during handling and molding. During pouring, it can withstand the high – temperature scouring and erosion of the molten metal |
6.2 Potential Causes of Coating Cracking
Potential Causes of Coating Cracking | Explanation |
---|---|
Excessive Suspending Agent or Thick Coating during Drying | During the drying process, if the amount of the suspending agent added is too large or the coating is too thick, drying cracks may occur |
Improper Operation during Molding | During the molding process, improper operations such as rough handling may cause micro – cracks in the coating, usually near the bearing points during handling, such as the flanges of mold products and the reverse – hand positions of weight – reducing holes |
Scouring by Molten Metal during Filling | The high – speed flowing molten metal during the filling process can directly scour the coating, causing damage to the coating |
Thermal Property Differences of Coating Components | Under the intense heat of the molten metal during the filling process, due to the different thermal property parameters of the coating components, cracks may occur |
Static Pressure of Molten Metal during Solidification | During the solidification process of the molten metal, the static pressure of the molten metal can also cause damage to the coating |
7. Specific Case Analysis
Taking a certain body – in – white stamping die casting produced by a factory as an example, we analyze the causes of “coating flakes” slag inclusion defects in detail.
7.1 Product Structure Impact
The mold base products of this type are mostly “I” – shaped or “Ji” – shaped structures. The defect – prone areas are concentrated on the back of the intersection of the bottom flange and the rib plate or the reverse – hand structure positions. When the molten metal fills from the bottom working surface to the rib plate, due to the sudden reduction of the cross – section, the flow rate of the molten metal increases sharply, resulting in intensified turbulence and entrainment of slag and gas. When the molten metal fills to the top flange surface, the cross – section increases, the flow rate of the molten metal suddenly decreases, and the gas gap in front of the molten metal is in an unbalanced state, which may cause the coating to fall off and the slag and gas to gather, forming defects. (See Figure 3 for the structure diagram of the “I” – shaped structure)
7.2 Pouring System Design
The unreasonable setting of the pouring system leads to the turbulence of the molten metal, causing instantaneous pressure loss and destroying the integrity of the coating. Under the scouring of the high – temperature molten metal, the coating breaks and enters the molten metal, and the bubbles and slag entrained in the molten metal gather together to form complex defects. When the reverse – rain – type hollow pouring system is used, the molten metal almost simultaneously starts to fill through each inner gate, which is likely to cause the confluence of multiple molten metal streams. These confluence areas are prone to defect generation.
7.3 Coating Itself Parameters
Foam plastics (both EPS and STMMA) are non – polar materials with low surface tension, and water – based coatings are not easy to wet and penetrate. Although surfactants are usually added to the coating to improve its wettability and adhesion, in the actual use process, the surfactant may fail, resulting in poor coating application, uneven coating thickness, and even discontinuous coatings. These defective coatings will enter the casting under the scouring of the high – temperature molten metal, generating “coating flakes” defects.
7.4 Coating Spraying and Drying Process Impact
An inappropriate coating formulation or an unsuitable binder can lead to insufficient low – temperature strength of the coating. During the drying process, micro – cracks may occur in the coating due to the inappropriate binder, which provides conditions for the generation of “coating flakes” slag inclusion defects.
7.5 Molding Process Impact
Although the full – mold casting process simplifies the molding operation, it does not mean that the operation requirements are reduced. On the contrary, due to the generally increased pouring temperature in full – mold casting, higher requirements are put forward for the molding process. For some reverse – hand holes, they must be filled tightly. A sand mold with sufficient strength can provide certain support and anti – scouring ability for the coating. The probability of “coating flakes” defects in a well – compacted sand mold is very low.
8. Improvement Measures for “Coating Flakes” Slag Inclusion Defects
8.1 Optimization of Pouring System Design
The design of the pouring system should aim to make the molten metal fill the mold smoothly and reduce the turbulence – caused slag and gas entrainment. When designing the pouring system, the sudden change of the cross – section should be considered to avoid the occurrence of the “instantaneous pressure – loss” phenomenon. For example, a reasonable inner gate layout and cross – section size can be determined through simulation analysis to ensure that the molten metal fills the mold evenly and with a proper flow rate. By improving the pouring system design, the filling speed and pressure of the molten iron can be increased, enabling the molten iron to fill the mold more smoothly.
8.2 Mastery of Molten Metal Flow and Filling Laws
In – depth research on the flow and filling laws of molten metal in lost foam casting is required. Through experiments and numerical simulations, the influence of various factors such as the structure of the foam pattern, the gasification speed, and the pouring process parameters on the flow of the molten metal can be analyzed. This can help casting engineers better understand the filling process of the molten metal and take corresponding measures to optimize the process, such as adjusting the pouring temperature, pouring speed, and the position of the inner gate according to the flow characteristics of the molten metal.
8.3 Selection of Suitable Coatings and Coating Processes
Choose coatings with excellent performance, including good permeability, low gas evolution, high strength, and good wettability and adhesion. At the same time, optimize the coating process, such as controlling the coating thickness, drying temperature, and drying time. For example, by using advanced coating spraying equipment and techniques, a uniform and continuous coating can be obtained. In addition, the binder in the coating should be selected reasonably to ensure that the coating has sufficient strength and good processability.
8.4 Setting of Riser and Vent
In the top dead – angle positions, local thick – walled parts, and areas where the molten metal converges or is difficult to fill, risers and vents should be set. Risers can collect slag and gas in the molten metal, and vents can ensure the smooth escape of gas generated during the pouring process, reducing the occurrence of “coating flakes” slag inclusion defects.
8.5 Strengthening of Process Control and Quality Management
Establish a complete process control system, strictly control the quality of raw materials, and ensure that the foam patterns, coatings, and molding sands meet the requirements. Strengthen the management of each production process, such as standardizing the operation of workers during the molding, coating, and pouring processes. In addition, regular quality inspections should be carried out on the castings to timely detect and correct potential quality problems.
9. Conclusion
Lost foam casting has unique advantages in modern casting production, but the “coating flakes” slag inclusion defect is a problem that restricts the quality improvement of castings. Through in – depth analysis of the causes of this defect, it can be seen that the pouring system design, coating performance, molding process, and product structure all have important impacts on the generation of defects. By taking corresponding improvement measures, such as optimizing the pouring system design, mastering the molten metal flow laws, selecting suitable coatings and coating processes, setting risers and vents, and strengthening process control and quality management, the “coating flakes” slag inclusion defect can be effectively reduced or even eliminated. This can improve the quality of lost foam castings, enhance the competitiveness of casting products in the market, and promote the healthy development of the casting industry. In the future, with the continuous development of casting technology, more in – depth research on lost foam casting defects and their improvement measures is expected to further improve the level of casting production.
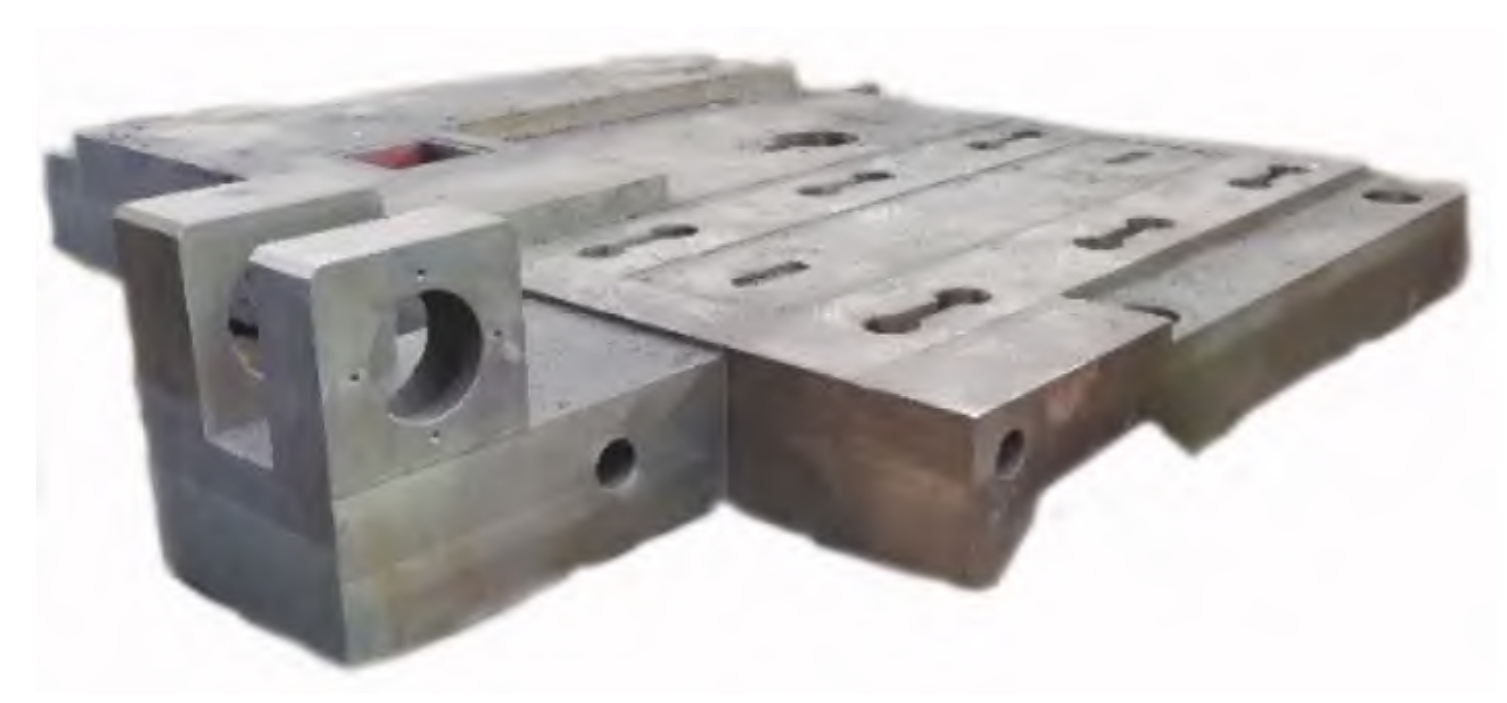