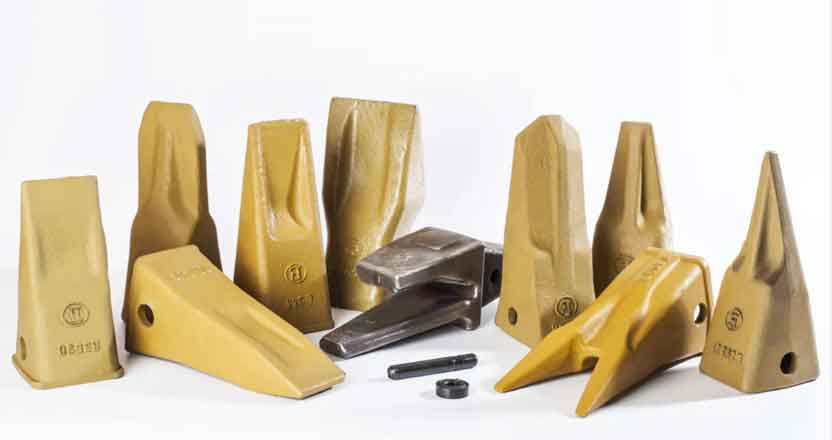
1. Introduction
In open-pit coal mines, electric shovels play a crucial role in the coal extraction process. However, the problem of bucket teeth falling off often occurs, which can lead to damage to crushers and other equipment, affecting the normal operation of the production line and causing economic losses. Therefore, the development of an effective bucket teeth detection system is of great significance. This article will focus on the application and development of bucket teeth detection technology in open-pit coal mines, including the necessity of the detection system, its development process, key technologies, and practical application effects.
2. The Necessity of Bucket Teeth Detection System
2.1 Wear and Damage of Bucket Teeth
Bucket teeth are an important part of the electric shovel bucket. During the operation of the electric shovel, the bucket teeth are constantly in contact with the coal and rock materials, subject to large impact forces and wear. If the bucket teeth are not detected and replaced in a timely manner, they may break or fall off, which will affect the working efficiency of the bucket and even damage the bucket itself.
Factors Affecting Bucket Teeth | Description |
---|---|
Impact Force | The bucket teeth are subjected to large impact forces when inserted into the materials, which may cause cracks or fractures. |
Wear | The continuous friction between the bucket teeth and the materials will cause wear, reducing the service life of the bucket teeth. |
2.2 Impact on Production Line
When the bucket teeth fall off, they may be mixed with the coal and transported to the crusher. If not detected in time, the fallen bucket teeth may cause blockages, damage to the crusher, or even belt tearing, affecting the normal operation of the entire production line.
Consequences of Bucket Teeth Falling Off | Description |
---|---|
Crusher Blockage | The fallen bucket teeth may block the crusher, preventing it from normal operation. |
Crusher Damage | The impact of the bucket teeth on the crusher may cause damage to its internal components. |
Belt Tearing | The bucket teeth may get stuck in the conveyor belt, causing it to tear. |
2.3 Safety Hazards
In addition to affecting the production line, the fallen bucket teeth may also pose a safety hazard to the operators. If the operators are not careful, they may be hit by the fallen bucket teeth, resulting in personal injuries.
Safety Hazards of Bucket Teeth Falling Off | Description |
---|---|
Operator Injury | The fallen bucket teeth may hit the operators, causing physical harm. |
3. Development of Bucket Teeth Detection System
3.1 Early Detection Methods
In the early stage, the detection of bucket teeth mainly relied on manual inspection. Operators need to regularly check the bucket teeth during the shutdown of the electric shovel to determine their wear and damage conditions. However, this method has many disadvantages, such as low efficiency, high labor intensity, and difficulty in detecting hidden damages.
Early Detection Methods | Advantages | Disadvantages |
---|---|---|
Manual Inspection | Simple operation, no need for special equipment | Low efficiency, high labor intensity, difficult to detect hidden damages |
3.2 Video Monitoring Technology
With the development of video technology, video monitoring systems began to be applied to the detection of bucket teeth. In 2008, the Baorixile Open-pit Coal Mine installed a “high-definition camera + monitor” video display device on the coal mining electric shovel. By observing the video screen in the cab, the absence of bucket teeth could be determined. However, due to the harsh mining environment, such as a large amount of dust, large stones, and viscous materials, the imaging effect of this device was very poor, and it was difficult to detect the absence of bucket teeth in a timely manner.
Video Monitoring Technology | Advantages | Disadvantages |
---|---|---|
High-definition Camera + Monitor | Can directly observe the bucket teeth | Poor imaging effect in harsh environment, difficult to detect in a timely manner |
3.3 Infrared Thermal Imaging Technology
In order to improve the detection effect in a harsh environment, infrared thermal imaging technology was introduced. In 2011, the Benxi Iron Mine replaced the high-definition camera with a far-infrared camera on the basis of the “high-definition camera + monitor”, realizing real-time monitoring of bucket teeth. The infrared thermal imaging technology is not affected by dust and light, and has a good imaging effect at night. However, the uncertainty of manual observation of the monitor still exists.
Infrared Thermal Imaging Technology | Advantages | Disadvantages |
---|---|---|
Far-infrared Camera | Good imaging effect at night, not affected by dust and light | Uncertainty of manual observation of the monitor still exists |
3.4 Computer Vision Technology
In recent years, computer vision technology has been widely used in the field of bucket teeth detection. In 2016, the Dexing Copper Mine purchased a WK – 35 electric shovel and installed an intelligent bucket teeth absence detection system. This system uses computer vision technology to compare the images collected by the thermal imager to determine the absence of bucket teeth and has an automatic alarm function. However, the pattern recognition algorithm of this system can only recognize several fixed features in the image, and the accuracy rate is only 70% due to various interference factors such as rock occlusion and cable occlusion. In 2017, the Dexing Copper Mine upgraded the pattern recognition algorithm, using computer vision technology for automatic analysis, identifying the number of bucket teeth, and judging whether the bucket teeth are absent. The accuracy rate of identification reached 96%.
Computer Vision Technology | Advantages | Disadvantages |
---|---|---|
Intelligent Detection System | Can automatically analyze and detect, with an alarm function | Pattern recognition algorithm has limitations, affected by interference factors, initial accuracy rate is low |
4. Key Technologies of “Infrared Thermal Imaging Camera + Computer Vision Technology” Bucket Teeth Detection System
4.1 Hardware Composition
The hardware of the “infrared thermal imaging camera + computer vision technology” bucket teeth detection system is composed of an infrared thermal imaging camera, an industrial control computer, and a monitor.
Hardware Components | Function |
---|---|
Infrared Thermal Imaging Camera | Captures thermal images of bucket teeth |
Industrial Control Computer | Processes and analyzes the images |
Monitor | Displays the detection results |
4.2 Function Module Composition
The system function modules include a thermal imager reading module, a video storage module, a bucket teeth absence detection module, and an alarm module.
Function Modules | Function |
---|---|
Thermal Imager Reading Module | Reads thermal images from the thermal imager and transmits them to other modules |
Video Storage Module | Stores the captured images for later review |
Bucket Teeth Absence Detection Module | Detects the absence of bucket teeth in the images |
Alarm Module | Alerts when bucket teeth are absent |
4.3 Bucket Teeth Detection Method
The bucket teeth detection method mainly includes two stages. In the first stage, the Viola – Jones Haar cascade classifier is used to detect the bucket teeth row in the original image. In the second stage, the convolutional neural network (CNN) is used to perform a two – class classification to determine whether the bucket teeth are absent.
Detection Stages | Method |
---|---|
First Stage | Use Viola – Jones Haar cascade classifier to detect bucket teeth row |
Second Stage | Use CNN for two – class classification to determine absence of bucket teeth |
5. Practical Application and Effect of Bucket Teeth Detection System
5.1 Application in Open-pit Coal Mines
The “infrared thermal imaging camera + computer vision technology” bucket teeth detection system has been widely applied in open-pit coal mines. For example, in the Heidaigou Open-pit Coal Mine, this system has been installed and used on the WK – 35 coal mining electric shovel, achieving good results.
5.2 Effect Evaluation
Since its installation and use in 2018, the bucket teeth detection system has shown excellent performance. It can accurately detect the absence of bucket teeth and issue an alarm in a timely manner. The system has a low failure rate and can provide accurate data for the replacement, statistics, and analysis of bucket teeth. It has effectively prevented accidents such as crusher blockage, crusher damage, and belt tearing, improving the production management level and equipment use efficiency on site.
Evaluation Index | Result |
---|---|
Detection Accuracy | High |
Alarm Timeliness | Timely |
Failure Rate | Low |
Data Support for Maintenance | Accurate |
6. Conclusion
The development of bucket teeth detection technology has gone through several stages from manual inspection to video monitoring, infrared thermal imaging, and finally computer vision technology. The “infrared thermal imaging camera + computer vision technology” bucket teeth detection system has effectively solved the problems of bucket teeth detection in open-pit coal mines, improving the production efficiency and safety of the mining process. In the future, with the continuous development of technology, the bucket teeth detection system is expected to be further improved and optimized to better meet the needs of the mining industry.