Abstract
According to the casting structure, size and existing 3D printing equipment and other conditions, the overall 3D printing scheme of the lathe worktable casting sand mold was planned, the pouring system, assembly box, melting process and key parameters of the worktable castings were determined, and the common casting defects in the production process of the worktable castings were analyzed and prevented. At present, mass production has been stable in quality. Machine worktable castings with high yield.
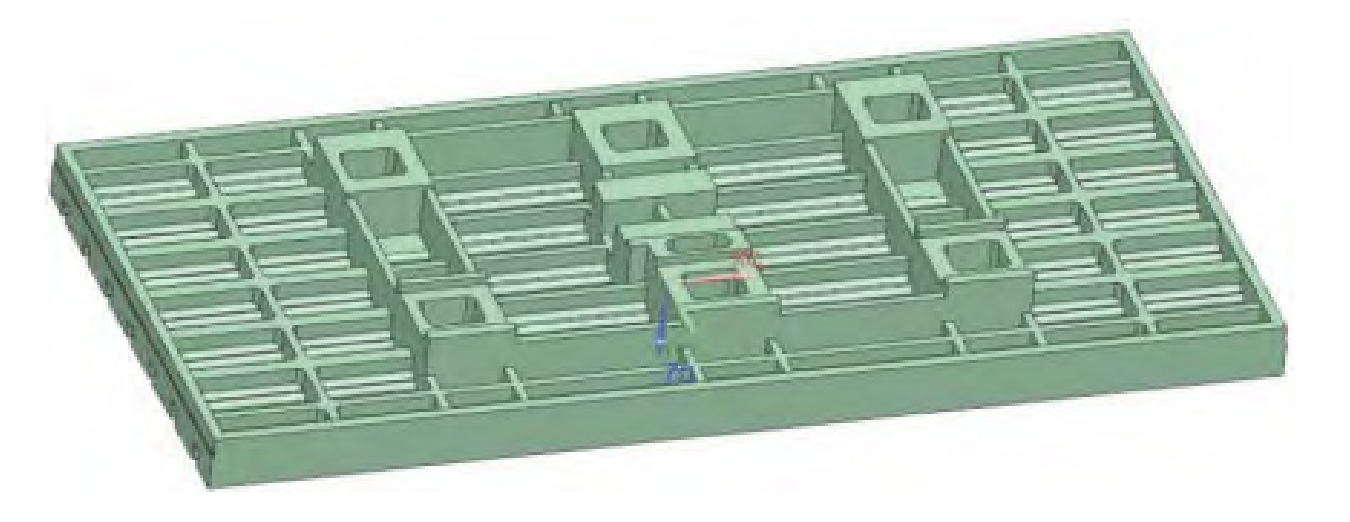
1. Casting Process Design and Trial Production
Process | Details |
---|---|
Casting Process Scheme Determination | – Overall 3D printing of sand mold considering workpiece size and equipment. – Placement of chills in the design to ensure quality. |
Pouring System Design | – One long side for iron liquid inlet, the other for pressure edge riser. – Total pouring time within 25s, area ratio of pouring system: ∑s直:∑s极:∑s内=1:1.6:0.8. |
Tooling Design | – Design a cavity plate as a large chill. – Dimensions: 6000mm×2500mm×300mm, with specific groove and slot designs. |
Sand Mold Printing | – Print size of 3D printing equipment: 2500mm×1500mm×1000mm. – Parameters of 3D printed silica sand and resin addition amount. |
Boxing | – Water – based coating flow coating process, twice, with sand mold moisture content ≤0.3% after drying. |
Melting and Pouring | – Raw materials and their proportions, melting temperature, and inoculation process. |
2. Prevention of Casting Defects in Worktable Casting
Defect Type | Causes | Prevention Measures |
---|---|---|
T – type Groove Bottom Shrinkage Porosity | Thick T – type groove forms a hot spot and lacks effective feeding. | – Use sand – separating chills to adjust the temperature field. – Increase the carbon equivalent. |
Porosity | – Thick wall leads to slow solidification and nitrogen segregation. – Local humidity in the mold causes hydrogen – nitrogen reaction. | – Dry the sand mold with moisture content ≤0.3%. – Control the nitrogen content in the charge and use the same material for recycling. |
3. Conclusion
- 3D printing technology improves the surface quality and dimensional accuracy of ‘worktable casting’.
- It also significantly improves the efficiency of boxing and has environmental and other advantages.
- With the increase in personalized ‘worktable casting’ in the market, the advantages of 3D printing casting in delivery time and quality will become more prominent.