In recent years, with the improvement of casting technology, cast steel nodes have achieved good plasticity, toughness, and weldability due to their material saving and aesthetic effects of intersecting nodes, as well as avoiding residual welding stress problems in multi rod intersecting welding connections, It has become an important node widely used in large-span building spatial structures both domestically and internationally. The aesthetic requirements of current bridge structures are becoming increasingly high, and many landscape bridges with novel shapes and complex structures are constantly emerging. Among them, there are also designs of intersecting nodes with complex stress in the structure. This article innovatively applies cast steel nodes to the design of large-scale intersecting nodes in a certain highway landscape bridge, It is both aesthetically pleasing and avoids the problem of residual stress in the welding of intersecting nodes, which can provide reference for similar projects.
1、 Material of cast steel nodes
Cast steel is divided into cast carbon steel and cast low alloy steel according to their chemical composition. Due to its poor hardenability and mechanical properties, as well as the inability to strengthen large cross-section components through heat treatment, cast carbon steel is currently mainly made of low alloy steel. Its main alloying elements are manganese Mn, silicon Si, chromium Cr, etc. These elements not only improve the strength of the material, but also greatly improve the plasticity of cast steel Flexibility and weldability.
At present, the domestic bridge engineering community generally believes that the cast steel material is poor and the weldability with the connecting structure is unreliable. Therefore, the design of connection nodes in bridge engineering usually uses welding of pipe fittings (or plates), and there are no engineering examples of using cast steel nodes. This understanding is mainly due to the current domestic steel casting standard “Carbon Steel Castings for Welded Structures” (GB7659-87) which has too low requirements for cast steel materials. This standard has relatively loose control over the S and P content of materials (<0.04%), no limit on the carbon equivalent of materials, and a lower impact value of materials; This standard also requires lower dimensional tolerances for steel castings and surface quality of castings; Castings produced according to this standard are far from meeting the requirements of steel castings for bridge welding structures.
However, there are many international standards for steel casting materials, such as the international standard IS03755, the Japanese standard JISG5102, the American standard ASTMA216, and the German standard DIN17182. The German standard (EU standard) has the strictest requirements for the chemical composition content and mechanical performance indicators of steel castings. This standard strictly controls the content of C and harmful elements S and P: the content of C is controlled within the range of 0.15% -0.2%, which is about 0.05% lower than other national standards; S. The P content is controlled below 0.025%, while other national standards are controlled below 0.045%.
Brand | C | Si | Mn | P | S | Cr | Mo | Ni |
GS-16Mn5 | 0.15-0.20 | ≤0.60 | 1.00-1.50 | ≤0.020 | ≤0.015 | ≤0.30 | ≤0.15 | ≤0.40 |
GS-20Mn5 | 0.17-0.23 | ≤0.60 | 1.00-1.50 | ≤0.020 | ≤0.015 | ≤0.30 | ≤0.15 | ≤0.40 |
At present, many large steel casting plants in China mainly refer to the German DIN17182 standard to produce cast steel for building structures, making cast steel joints widely used in large-span building spatial structures. The chemical composition and mechanical performance requirements of the materials in this standard are shown in Table 1 and Table 2, respectively.
Brand | Heat treatment status | Casting wall thickness (mm) | Yield strength (MPa) | Tensile strength (MPa) | Elongation rate (%) | Impact energy (J) |
GS-16Mn5 | Normalizing | ≤50 >50≤100 | ≥260 ≥230 | 430-600 430-600 | ≥25 ≥25 | ≥65 ≥45 |
GS-20Mn5 | Normalizing | ≤50 >50≤100 >100≤160 >160 | ≥300 ≥280 ≥260 ≥240 | 500-650 500-650 480-630 450-600 | ≥22 ≥22 ≥20 | ≥55 ≥40 ≥35 |
GS-20Mn5 | Quenching and tempering | ≤50 >50≤100 >100≤1600 | ≥360 ≥300 ≥280 | 500-650 500-650 500-650 | ≥24 ≥24 ≥22 | ≥70 ≥50 ≥40 |
2、 Types and characteristics of cast steel joints
2.1 Types of cast steel nodes
The common types of cast steel nodes include tree shaped cast steel nodes, hinged cast steel nodes, and hybrid cast steel nodes. Among them, the tree shaped cast steel node is shown in Figure 1, which is used to replace the node where the main pipe intersects with multiple branch pipes. Butt welds are used instead of intersecting welds, which disperses the welds and reduces welding stress concentration. Articulated cast steel nodes are commonly used at the end connections of members (such as supports), which can simplify the nodes and have a beautiful appearance. The hybrid cast steel node has the common characteristics of tree shaped cast steel nodes and hinged cast steel nodes.
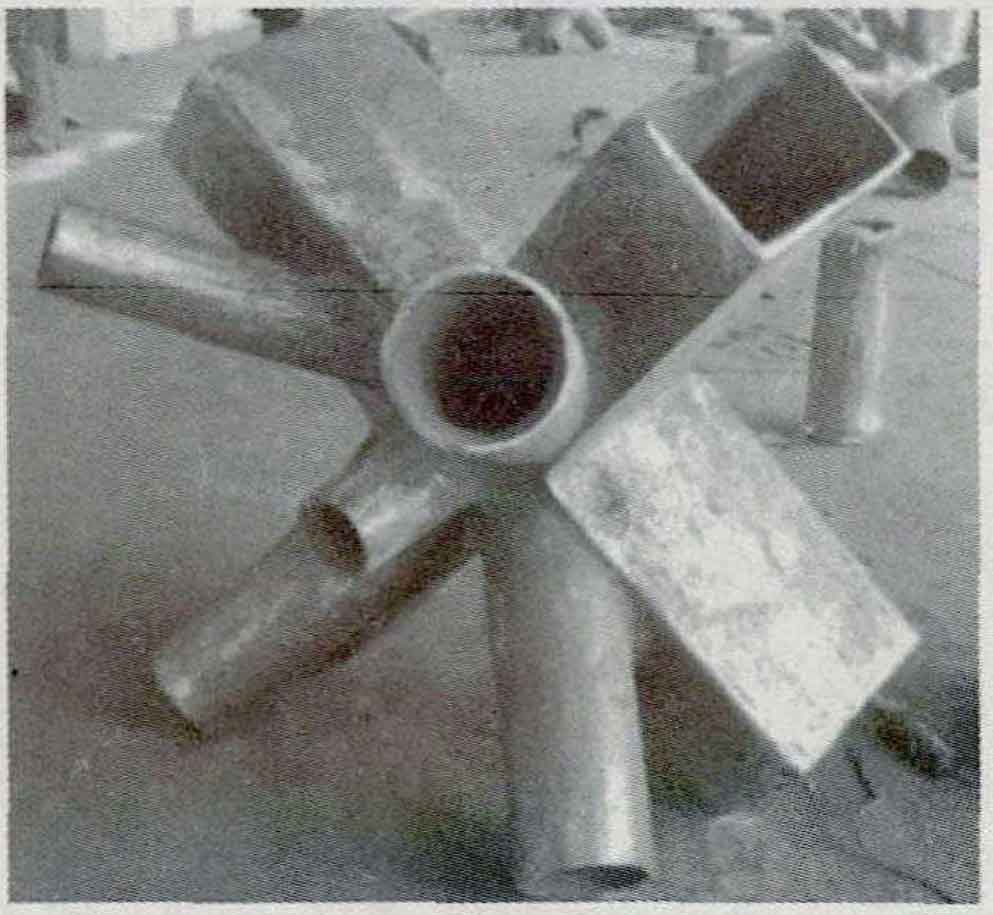
2.2 Characteristics of cast steel nodes
Compared with ordinary pipe intersecting welded joints, cast steel joints have the following characteristics:
(1) Cast steel nodes have beautiful shapes and strong adaptability, and can produce nodes with complex shapes and inner cavities according to actual needs; The most reasonable cross-sectional shape can be adopted according to the stress conditions, thereby improving the stress distribution of nodes.
(2) Cast steel nodes are generally semi-solid nodes, even if they are all hollow, they are thicker than steel pipes or steel plates. Therefore, it has high bearing capacity and strong resistance to deformation.
(3) Cast steel nodes are cast as a whole in the factory, and compared to welded ball nodes and steel pipe intersecting nodes, stress concentration caused by intersecting line cutting and overlapping weld welding can be avoided.
(4) The chemical composition requirements for cast steel joints in welded structures are higher than those in other fields, and the content of C, S, and P is strictly limited to ensure that the material has good plasticity, toughness, and weldability.
(5) The application range of cast steel nodes is wide, and they are not limited by the position, shape, or size of the nodes. They can be used for both mid structure nodes and support nodes.
3、 Production and welding of cast steel nodes
3.1 Production process of cast steel nodes
The production process of cast steel nodes mainly includes three aspects: casting, heat treatment, and post-treatment of cast steel parts.
(1) The basic process of casting technology is:
Mold making – shaping – smelting – pouring.
The commonly used model for cast steel nodes is the wooden model, as shown in Figure 2. During the production process of the model, the dimensions, angles, and surface smoothness of each part of the model should be strictly controlled.
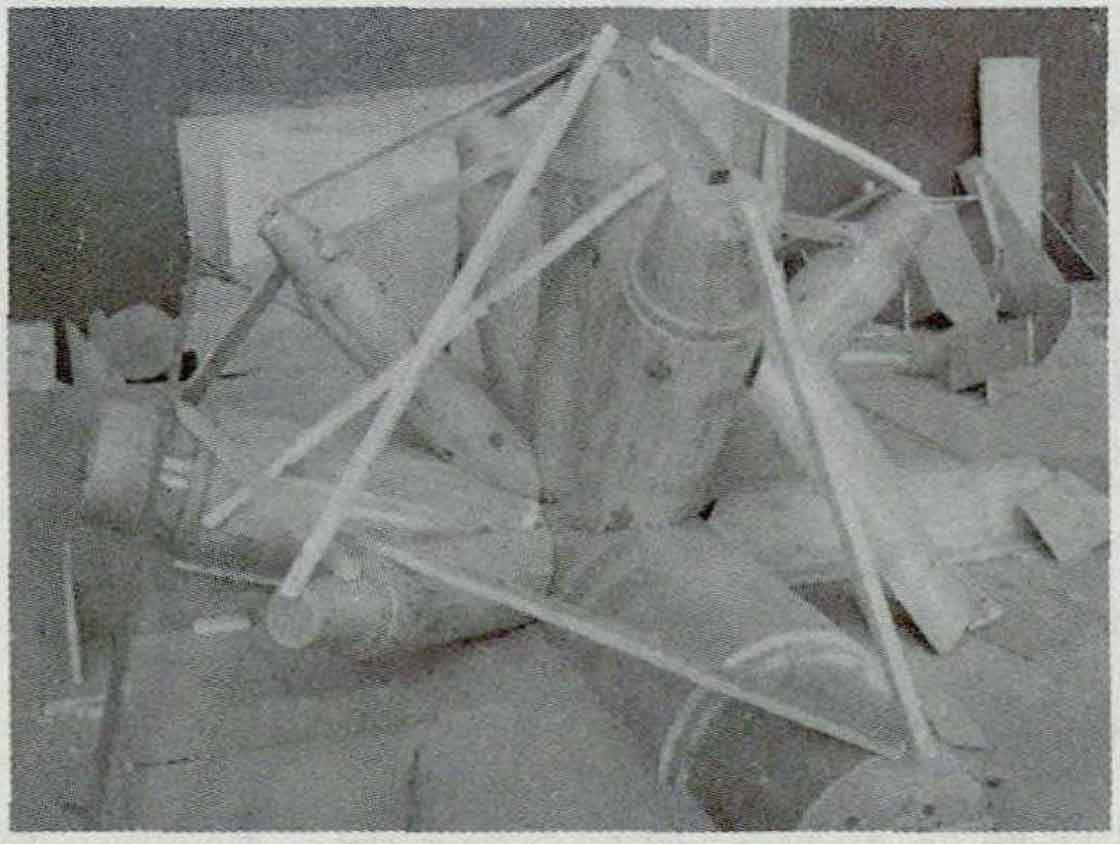
Node modeling usually adopts a sand molding process with high surface stability, as shown in Figure 3. In order to increase the resistance of molding sand to the erosion and erosion of molten metal, and to prevent sand sticking on the surface of castings, appropriate coatings should be applied to the surface of the mold.
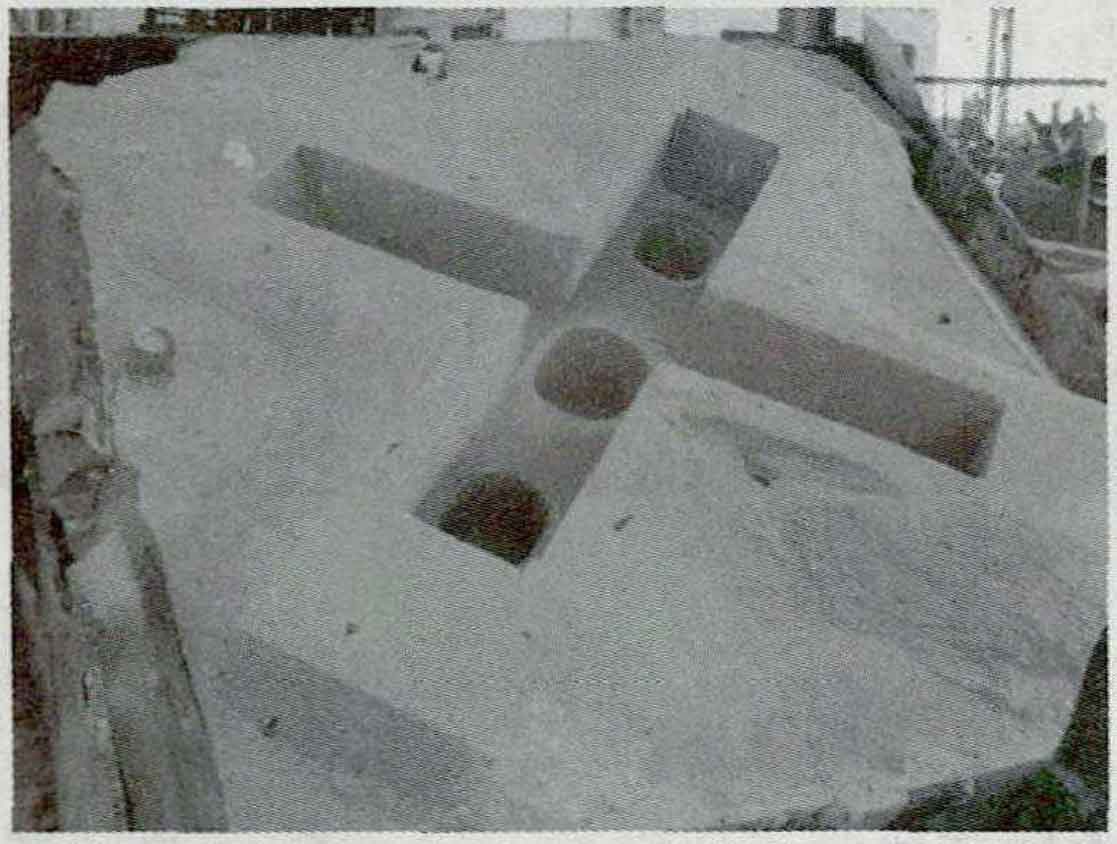
During the smelting process, the quality of steelmaking raw materials should be controlled, high-quality small and medium-sized scrap steel should be used, and after the steelmaking is melted, slag making and slag flow should be emphasized to facilitate low-temperature phosphorus removal. At the same time, desulfurization operations during the reduction period should be strengthened. The pouring of molten steel should ensure that the steel entering the mold cavity is stable, with a suitable upward speed, and there is no vortex phenomenon.
(2) Heat treatment
In order to improve the mechanical properties of steel castings and eliminate the casting stress generated during the casting process, heat treatment should be carried out on steel castings. According to DIN17182, heat treatment is carried out by normalizing+tempering or quenching+tempering according to the grade of the cast steel, with strict temperature range specified in the standard. The heating speed in the heat treatment process depends on the chemical composition, the cross-sectional size and shape of the cast steel node, and the insulation time depends on the maximum wall thickness of the cast steel node and the charging and stacking conditions.
(3) Post processing
The post-treatment of cast steel nodes includes sand cleaning, cutting the gating and riser system, removing local defects, welding repair, polishing, shot blasting, rust prevention treatment, etc.
The surface of the node should be cleaned, trimmed with burrs and burrs, and the sprue, sand sticking, iron oxide scale, and residual materials inside the cavity should be removed. Defects on the surface of nodes that do not affect their performance are allowed to be repaired by welding, but welding is not allowed when there are honeycomb shaped pores. Shot blasting or sandblasting for rust removal before surface coating.
3.2 Quality control of cast steel joints
Quality control is the basic guarantee for producing qualified cast steel nodes. To ensure the quality of cast steel joints, the following key controls are mainly implemented during the node casting process:
(1) Quality control of wooden formwork
The wooden mold adopts a three-dimensional coordinate system to detect the dimensions, angles, and surface smoothness of each part of the wooden mold, and the inspection report is archived for future reference.
(2) Material control
Control the content of each element according to the requirements of DIN17182 standard, provide reports on the chemical composition and mechanical properties of each furnace of steel, and prepare retest samples.
(3) Internal quality control
Nodes must not have defects that affect performance, such as shrinkage, porosity, porosity, cracks, etc. Perform ultrasonic testing if necessary.
4.、 Welding of cast steel nodes
Cast steel nodes produced according to the German DIN17182 standard have good welding performance due to strict control of the content of C, S, and P in the cast steel material. When welding between cast steel nodes and steel pipes, strict evaluation must be conducted on the selection of welding rods and welding processes. Welding rods are mainly selected based on the material properties of cast steel nodes and steel pipes, and should be dried before use. The welding process mainly involves strict control of specimen assembly, specimen calibration, reserved welding shrinkage, welding positioning, pre welding protection, cleaning, preheating, welding, insulation, inspection and other processes.
5、 Engineering Design Example
5.1 Project Overview
A certain highway overpass bridge adopts a double arch single tower double cable surface steel box girder cable-stayed bridge (Figure 4), with a span arrangement of 46m+46m and a bridge width of 11.8m (including wind nozzles). The cable tower is a steel tube concrete structure, with the main beam being a steel box girder structure and the tower beams hinged. The center beam of the bridge deck is 1.275m high, and the diameter of the cable tower column is 1.0m.
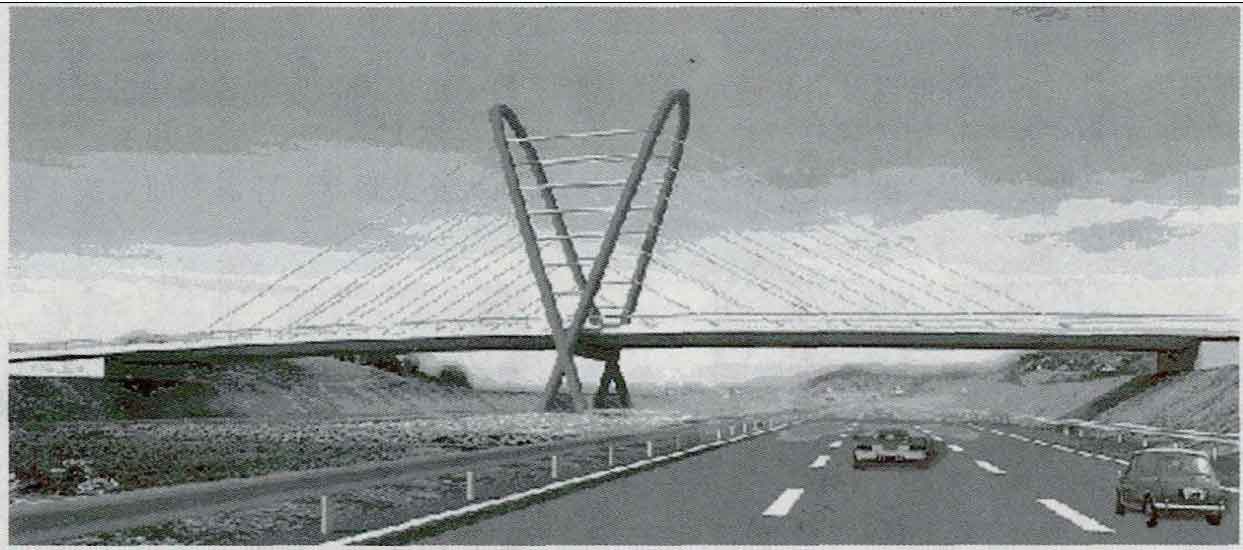
Among them, the design of the Sota tower column adopts a steel pipe concrete structure, with a steel pipe size of 1000X20, using Q345D steel, and injecting C50 micro expansion concrete into the pipe. The bridge tower and the lower expansion foundation are consolidated. The total height of the bridge tower above the foundation top is 29.15m, and the height of the tower above the bridge deck is 20.49m. The two tower legs intersect, and the direction of the bridge facade is X-shaped with an angle of 40 degrees. A total of 12 connecting steel pipes are installed at the corresponding positions of the cables, Made of Q345D steel and seamless steel pipe with a diameter of 00X10; At the intersection of the two tower columns, an I-shaped steel beam is installed, with a height of 1.46m and a flange width of 0.6m. It is welded with Q345D steel plate.
5.2 Design of cast steel nodes
From the perspective of the stress on the entire bridge structure, the intersection point of the main tower columns is a critical area with complex stress. If steel pipe intersecting welding is used, there will be problems of weld overlap and welding stress concentration, becoming weak parts of the structure. After research and expert verification, the final design was carried out using cast steel joints.
(1) Cast steel material
The material is controlled according to the GS_20Mn5 standard of the German standard DIN1782, with a yield strength greater than 250MPa, a tensile strength of 500-600MPa, an elongation of 24%, an impact energy greater than 40J, and a welding equivalent Ceq less than 0.42. Chemical composition C: 0.15% -0.18%; Si: < 0.60%; Mn: 1.0% -1.3%; P: < 0.015%; S: < 0.015%; Cr < 0.30%; Mo < 0.15%; Ni<0.40%.
(2) Design points
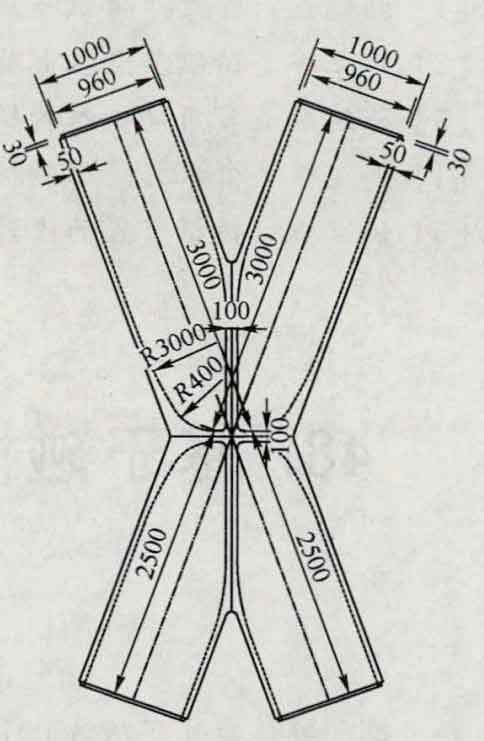
According to the results of the overall force analysis, the tower legs 3m above and 2.5m below the intersection of the tower columns were designed as cast steel nodes, as shown in Figure 5. The diameter of the cast steel node limb pipe is 1m, which is the same as the connected steel pipe; To ensure that the molten steel enters the inner cavity evenly and smoothly, and to ensure the solidification speed of the molten steel, the wall thickness of the cast steel node should not be too thin. The wall thickness of the hollow cast steel pipe is usually 1.5-3 times that of the connected steel pipe, and the wall thickness of the cast steel node limb pipe is 5cm, which is 2.5 times that of the connected steel pipe, Thickening treatment should be applied to the waist with concentrated stress at the node; To reduce self weight, the nodes are hollowed out internally and only the cross shaped partition is retained for force transmission, with a thickness of 10cm; To avoid sharp corners and facilitate sand cleaning, the inner and outer walls between the various limb pipes and partitions of the cast steel node are smoothly transitioned, and rounded corners are designed; A 2cm wide and 3cm high platform opening is left at the welding point between the limb pipe and the main tower steel pipe for easy docking with the main tower steel pipe; The cast steel node is located on the outer surface of the main tower crossbeam, 90cm above and 80cm below the intersection point, and is cast into a plane within a range of 40cm on the left and right sides. A 5cm long 11445X800X100X100 I-shaped section short limb is left to connect with the crossbeam; The weight of a single cast steel node is 16.1 tons.
(3) Stress analysis
After determining the geometric dimensions of the cast steel node, a spatial finite element program is used to analyze the stress of the cast steel node. Due to the thicker wall thickness of the cast steel nodes, solid elements were used for modeling; Due to the good plasticity of cast steel, its strength can be simplified as an ideal elastic-plastic model, and the strength criterion adopts the VonMises yield criterion. That is, when the VonMises stress at the calculation point exceeds the material strength, it is considered that the point has entered plasticity; The node load is considered based on the most unfavorable internal force combination calculated as a whole, and is applied to the upper end of the cast steel node and the side nodes connected to the crossbeam; Apply fixed constraints to the lower end of the cast steel node. After calculation and analysis, the waist of the cast steel node has a stress value of about 30MPa due to the presence of a solid partition; The maximum stress occurs on the limb tube, not exceeding 80MPa; The stress amplitude of the node under live load was also calculated, with a maximum stress amplitude of 22MPa; Therefore, the stress on cast steel nodes is within the elastic range, and fatigue failure will not occur, with a large safety reserve.
From the above analysis, it can be seen that the advantages of using cast steel nodes at the intersection of the main tower columns of this bridge are very obvious: firstly, it can significantly reduce the stress level. If tower column steel pipe intersection welding is used, the maximum VonMisses stress of the node exceeds 200MPa; In addition, the cast steel node avoids the problem of sharp angle welds and overlapping welds in the intersecting welding of steel pipes, and there is no residual welding stress.
6、 Suggestions and Outlook
(1) At present, the design method of cast steel nodes is not yet mature, and finite element analysis is an important approach. However, to ensure the safety of nodes, it is necessary to conduct node tests on cast steel nodes with complex structures and high stress, providing a basis for design.
(2) When cast steel nodes are used in bridge structures, the fatigue performance of the nodes should be analyzed.
(3) High attention should be paid to the welding of cast steel nodes and steel pipes, especially the welding process qualification test before welding, and measures such as preheating before welding and insulation after welding should be taken.
(4) The cost of cast steel nodes is relatively high. When designing, while meeting the stress requirements, the size of cast steel nodes should be minimized as much as possible and the excavation rate inside the nodes should be increased.
(5) The development of cast steel joints is still in its early stages in China, and there is still a significant gap compared to developed countries. There is an urgent need to establish standards and specifications for design, casting, and construction.
(6) With the continuous improvement of casting technology, cast steel joints will be increasingly widely used in China, and will be more favored by designers in structures with complex node structures.