1 Introduction
A twin-cylinder cylinder head is a twin-cylinder 250 displacement aluminum alloy twin-cylinder head produced by our company, made of A356, single piece of wool The weight of the billet is 5Kg, and the dimensions are 244mm× 228mm×114mm, the minimum wall thickness is 3.5mm, and the thickest point is 29mm (Figure 1). Its technical requirements do not allow the existence of defects that affect the use of cracks, porosity, shrinkage porosity, looseness, slag inclusion, bulging nodules, cold insulation and insufficient pouring; The specific air tightness testing requirements are as follows:
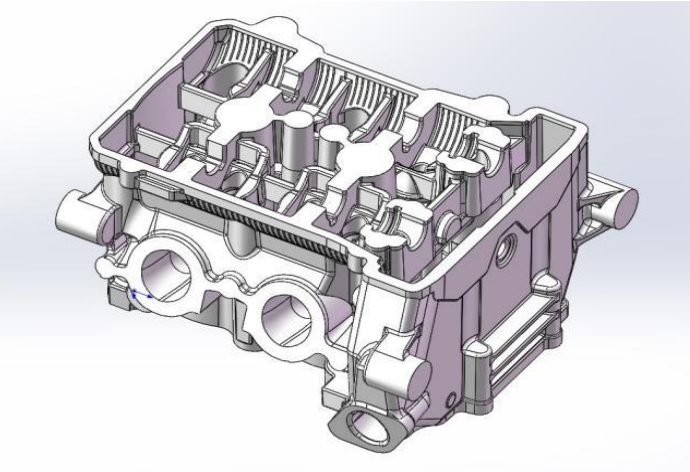
Figure 1 3D screenshot of the casting
The product was developed by our company in 2016 for an OEM in Chongqing, and the pass rate of the product in the early stage was very unsatisfactory, and the comprehensive pass rate of the product was only 71.92% from 2016 to 2018 through continuous optimization and improvement; From 2019 to 2020, the customer of this product had no orders for more than two years, and the company scrapped the mold of this product when it cleared its capital and verified production. In the second half of 2021, the customer has another order demand for the product, in this case, the company urgently started the design and production of the product mold, due to the low comprehensive pass rate of the product in the early stage, the casting team after analysis, the casting process of the product has been optimized and improved accordingly, and the comprehensive pass rate of the product produced by the redesigned mold has reached 91.78%.
2 The application of the optimal design of the casting process of the product
This cylinder head is a cylinder head with complex shape and structure produced by our company, which is composed of an integral waterway core, two intake and exhaust cores, an oil chamber core, and a cam chamber core. Through the careful analysis of the casting team, we have optimized the casting process as follows:
2.1 Optimization and improvement of pouring process and comparison before and after
The pouring process optimizes the design of the riser shape, and at the same time, the two sides of the intake and exhaust are directly formed by metal molds, so that the solidification time of the casting is shortened, and the optimized design directly reduces the amount of sand core, improves the production efficiency, and the key is to improve the comprehensive pass rate of the product.
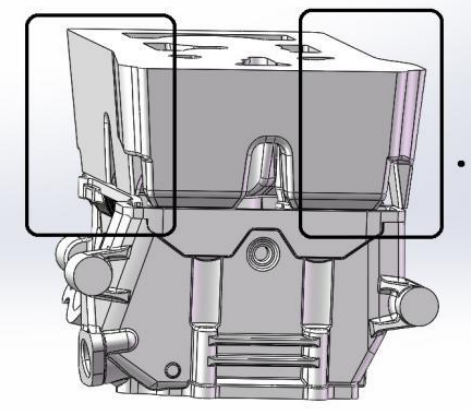
Optimize the pre-process
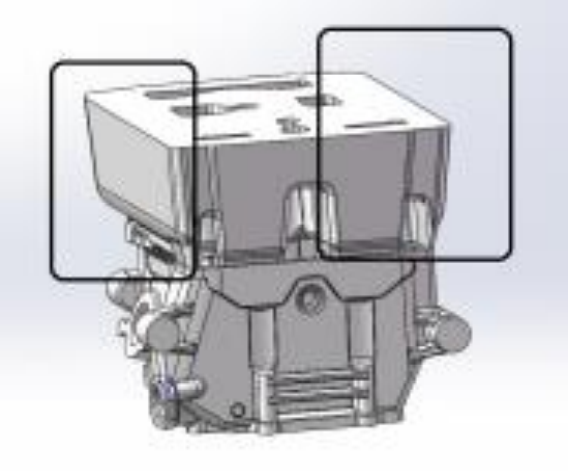
Optimize the post-process
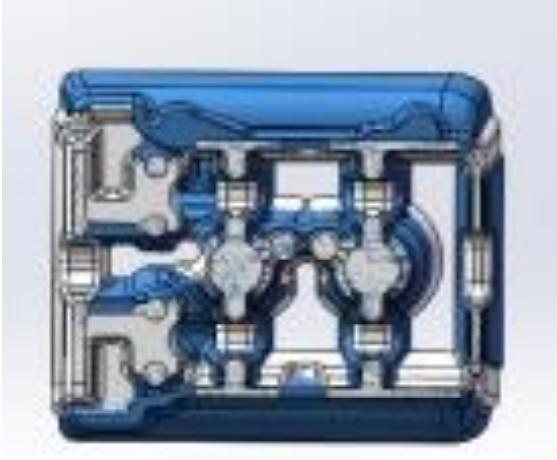
Before-and-after comparison
Figure 2 Comparison before and after optimization of the casting process
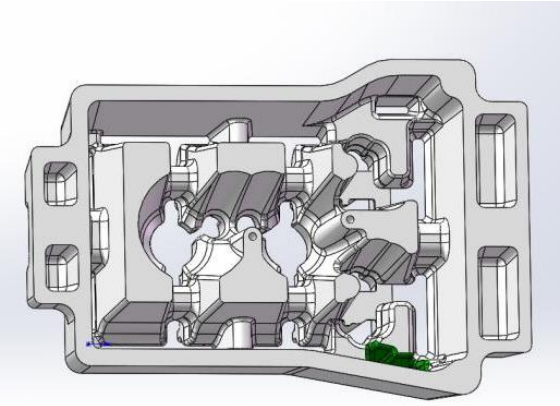
Optimized front cam core
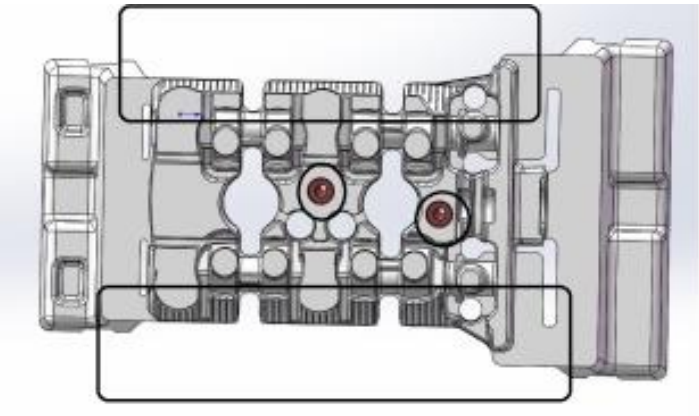
Optimized rear cam core
Figure 3 Cam core optimization scheme
2.2 Optimization and improvement of sand core exhaust in waterways (two places)
The waterway sand core and the oil chamber sand core of this product are optimized by convex and concave fit, and at the same time, the waterway core is poured in the oil chamber core The gas discharge channel is connected with the exhaust channel in the riser, so that the gas generated by the waterway sand core in the pouring process is completely discharged, and the waterway core itself adopts the negative pressure pumping method for air pumping.
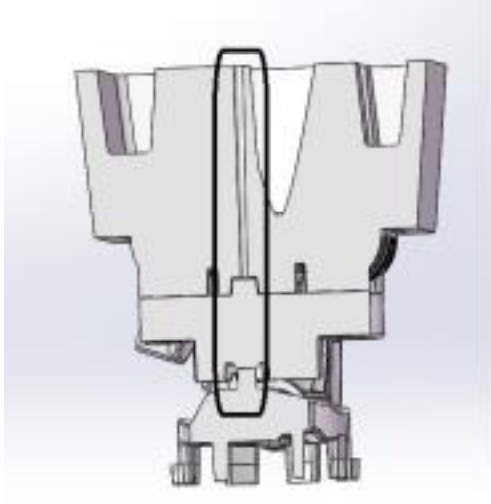
Optimized cam core combination for the front water chamber
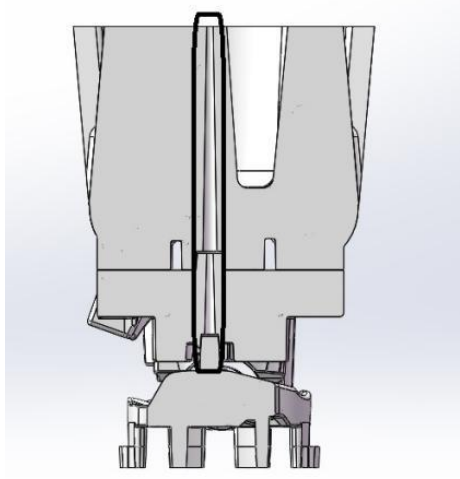
Optimized rear channel oil chamber cam core combination
Figure 4 Optimization scheme of sand core combination
3 Optimization, improvement and comparison of metal cores of pre-cast holes in tensioner holes
The optimized material of the metal core of the pre-cast hole of the tensioner hole is made of beryllium bronze, and the back of the metal core is air-cooled However, the method was carried out to completely improve the shrinkage defect of the tensioner hole
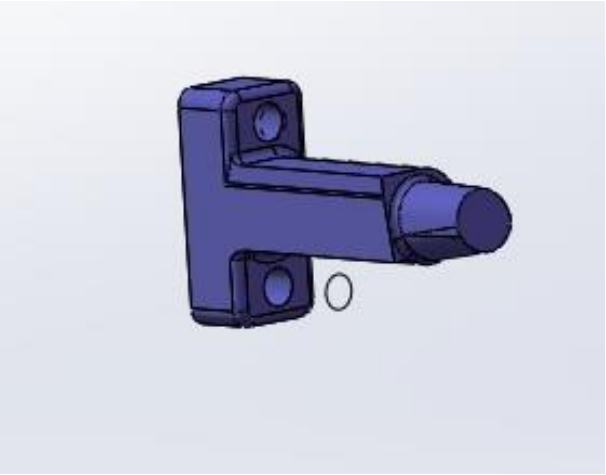
Beryllium bronze material is used after optimization
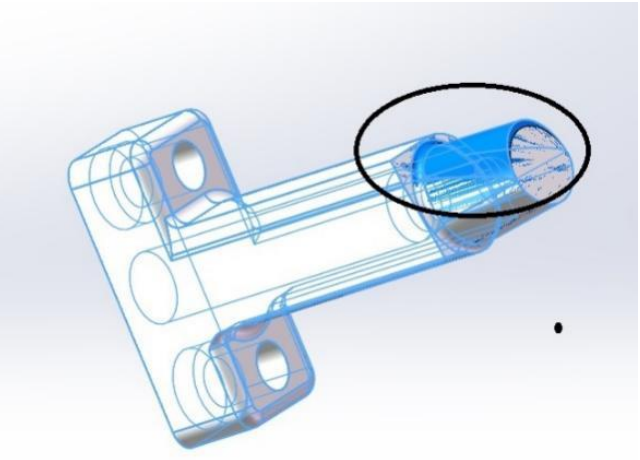
Comparison before and after optimization (reduction of local machining allowances)
Figure 5 Beryllium bronze is used for the metal core
4 Conclusion
By optimizing the above processes, improving the design and remaking the mold, the comprehensive pass rate of the product has been directly improved from 71.92%. to 91.78%. Process optimization needs to run through the entire casting process, and the qualification rate of some products is too low, so it is necessary to seek breakthroughs from the direction of casting process optimization.