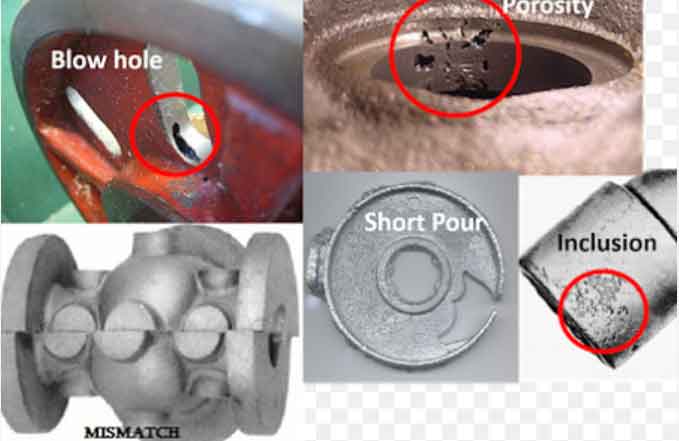
Casting defects can significantly affect the quality, reliability, and performance of metal components. Understanding the different types of casting defects, their impact on the final product, and implementing appropriate remediation measures is vital for achieving high-quality castings. This article takes a closer look at casting defects, explores their various types, discusses their impact, and provides remediation strategies.
Gas-related Defects:
- a) Porosity: Porosity refers to the presence of gas voids or pockets in the casting. It can lead to reduced strength, leakage, and compromised structural integrity. Remediation measures include proper degassing techniques, effective mold venting, and controlling melt cleanliness.
- b) Blowholes: Blowholes are larger cavities caused by entrapped gases. They can result in surface imperfections and weakened areas. Remedies include improving mold design, optimizing pouring practices, and implementing vacuum or pressure casting methods.
Solidification-related Defects:
- a) Shrinkage: Shrinkage defects occur due to uneven cooling and solidification, resulting in voids or shrinkage cavities. They can lead to dimensional inaccuracies and structural weaknesses. Remediation involves using proper riser design, controlling solidification rates, and employing feeding techniques such as hot topping.
- b) Hot Tears: Hot tears are cracks that occur during solidification due to high thermal stresses. They can cause severe component failure. Preventive measures include optimizing casting design, implementing controlled cooling techniques, and using alloys with reduced susceptibility to thermal cracking.
Metallurgical Defects:
- a) Inclusions: Inclusions are foreign materials trapped in the casting, such as oxides, slag, or refractory particles. They can weaken the structure and decrease mechanical properties. Remediation strategies involve using clean and high-quality raw materials, employing effective filtration systems, and maintaining proper furnace conditions.
- b) Segregation: Segregation refers to the uneven distribution of alloying elements, resulting in localized variations in material properties. It can lead to inconsistent mechanical properties and reduced performance. Prevention includes proper alloy selection, optimizing pouring practices, and employing controlled solidification techniques.
Surface Defects:
- a) Surface Roughness: Surface roughness defects include rough surfaces, scale, or irregularities. They can negatively impact aesthetics, functional characteristics, and ease of machining. Remediation involves proper mold surface preparation, controlling mold temperature, and ensuring optimal gating and pouring conditions.
- b) Cold Shots: Cold shots occur when solid particles become trapped in the casting, leading to voids or inclusions. They can compromise structural integrity and dimensional accuracy. Remedies include using clean and filtered molten metal, optimizing gating systems, and controlling pouring parameters.
Casting defects can arise from various sources and have different implications for the final product. Understanding the types of defects, their impact on component quality and performance, and implementing appropriate remediation measures are crucial for achieving defect-free castings. By focusing on factors such as gas-related defects, solidification-related issues, metallurgical concerns, and surface defects, manufacturers can enhance their casting processes, improve product quality, and meet customer expectations. Continuous process monitoring, quality control, and collaboration between foundry personnel and casting experts are essential for effective defect prevention and remediation in metal casting.