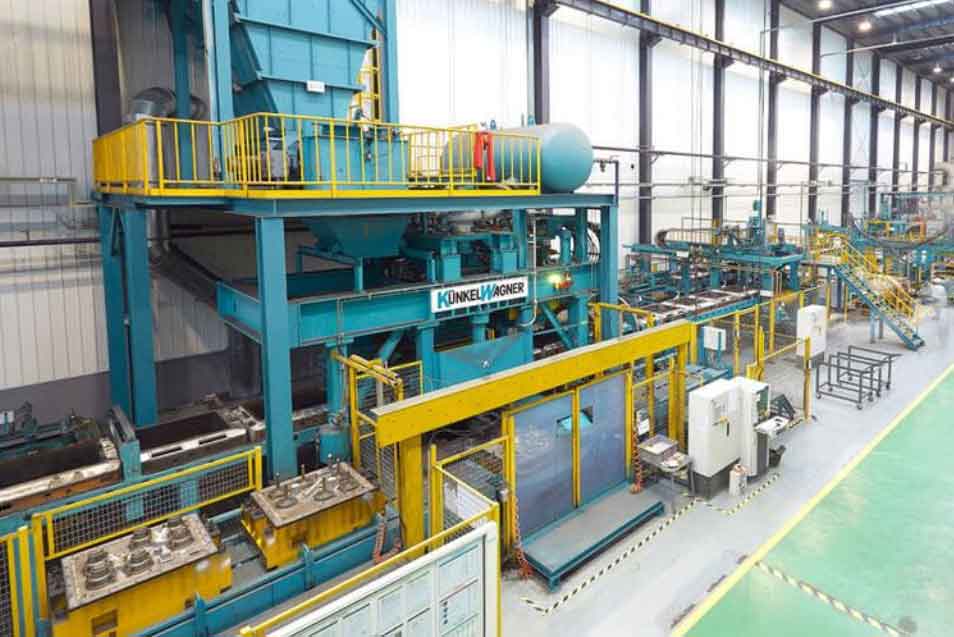
Investment casting, also known as precision casting or lost-wax casting, plays a crucial role in the aerospace and defense industries due to its ability to produce complex, high-precision components with excellent surface finishes. This casting method is particularly suited to manufacturing parts that must withstand extreme conditions and stresses, such as those found in aerospace and defense applications. Here’s a detailed analysis of the economic impact of investment casting on these industries:
1. Cost Efficiency
- Reduced Waste: Investment casting allows for tighter dimensional tolerances and a smoother surface finish compared to other casting methods. This precision reduces the need for secondary machining and finishing processes, leading to significant cost savings in material and labor.
- Tooling Costs: While the initial tooling costs for investment casting can be higher compared to other methods, the longevity of the molds and the reduced need for secondary processing can offset these costs over time, especially in high-volume production scenarios.
2. Design Flexibility and Innovation
- Complex Geometries: Investment casting is highly valued for its ability to produce components with complex geometries, internal passageways, and intricate details that would be difficult or impossible to achieve with other manufacturing processes.
- Material Variety: This method can utilize a wide range of alloys, many of which are crucial for aerospace and defense applications, such as titanium, Inconel, and specialized steel alloys. This versatility supports innovation in materials and design, driving advancements in aerospace and defense technology.
3. Supply Chain Simplification
- Reduced Assembly Requirements: The ability to cast complex parts as single pieces rather than assembling them from multiple smaller pieces not only reduces production time and costs but also enhances the integrity and strength of the components.
- Inventory Management: Simplifying the component count in assemblies helps streamline inventory management and logistics, reducing costs and improving supply chain efficiency.
4. Product Performance and Reliability
- High-Quality Standards: Investment casting produces parts with exceptional accuracy and consistency, which is paramount in aerospace and defense where component failure can have catastrophic consequences.
- Durability: Cast parts often exhibit superior mechanical properties and durability due to the fine grain structures that can be achieved, enhancing the performance and lifespan of critical components.
5. Lead Time Reduction
- Rapid Prototyping: The compatibility of investment casting with rapid prototyping technologies, such as 3D printed wax or resin patterns, significantly shortens the development cycle for new parts, allowing for faster iteration and refinement.
- Speed to Market: Faster prototype development and streamlined production processes enable quicker responses to market or operational demands, providing a competitive advantage in rapidly evolving industries like aerospace and defense.
6. Environmental Impact
- Material Efficiency: The precise casting process reduces material waste, which is economically beneficial and aligns with increasing environmental regulations in global manufacturing sectors.
- Energy Consumption: Although investment casting requires significant energy input, especially for melting and maintaining the temperature of high-performance alloys, ongoing improvements in furnace technology are helping to reduce these impacts.
7. Strategic Benefits
- Competitive Edge: By adopting advanced investment casting techniques, companies in the aerospace and defense sectors can maintain a technological edge over competitors, offering superior product quality and performance.
- Global Compliance: Meeting the stringent quality and safety standards required in these industries not only ensures compliance with global regulations but also opens up international markets, enhancing economic opportunities.
Investment casting, significantly impacts the economic landscape of the aerospace and defense industries by enhancing component quality, reducing production costs, and facilitating innovation. As these industries continue to demand higher performance and more complex components, the role of investment casting is likely to grow even further, reinforcing its economic importance.