The control of molten iron temperature is generally divided into two aspects: one is the control of molten iron temperature, the other is the control of pouring temperature. This section will discuss and analyze the two aspects of delivery.
The temperature of molten iron is usually used to measure the superheat temperature of molten iron. The effects of superheat temperature and holding time on graphite morphology were studied. It is believed that when the superheat temperature T is less than 1400 ° C and the temperature is kept for 30 minutes, the content of type A, type D and type T will not change much; when the superheat temperature T is in a certain range (1400-1455 ° C), type A will start to decrease and type D and type T will increase slowly; while when the superheat temperature T is more than 1455 ° C, the decrease speed of type A and the increase speed of type D and type T will increase sharply. The reason for the phenomenon is that the change of oxygen content in molten iron causes: when the superheat temperature T < 1450 ° C, the oxygen content in molten iron increases to 1400 ° C and reaches the maximum value; when t > 1500 ° C, the oxygen content decreases dramatically.
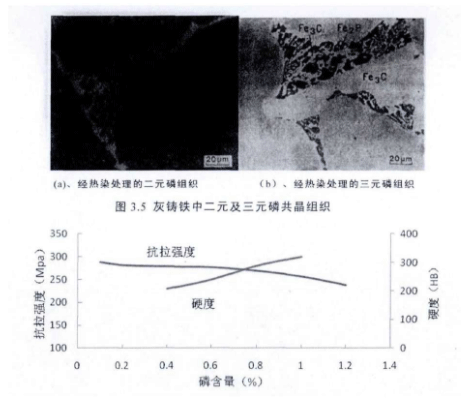
The superheat temperature also affects the quantity and size of eutectic. The higher the superheat humidity is, the more the sulfide as the nucleation grain melts during the heat preservation period, the more the sulfide nucleation decreases, the lower the nucleation ability of graphite and the less the amount of eutectic in molten iron. At the same time, due to the change of oxygen content in molten iron with superheat temperature, the number of nuclei in SiO2 matrix decreased gradually after t > 1500 ° C. These two reasons determine that with the increase of subcooling temperature, the total number of eutectic clusters changes in a downward trend, only at 1450 ° C to 1500 ° C, the number of eutectic clusters is basically unchanged. For the convenience of research, the pouring temperature in the figure is 1350 ° C, and the number of eutectic clusters is measured by pieces / cm2.
Similarly, the refinement of primary austenite is related to the superheat temperature. With the increase of superheat temperature, primary austenite has a process of refining first and then coarsening, and the volume fraction of austenite dendrite increases. When the superheat temperature is 1500 ℃, the refinement of primary austenite reaches the ultimate.
With the change of superheat temperature, the microstructure of material can also be certified by the change of mechanical properties of cast iron. It has been proved by experiments that when T < 1500 ° C, the tensile properties and hardness of gray cast iron increase with the increase of superheat temperature, and the mechanical properties of gray cast iron reach the best when it reaches 1500’c. However, when t > 1500 ℃, the tensile strength and hardness of gray cast iron decrease gradually.
However, the influence of superheat temperature on the shrinkage defect tendency of castings needs two considerations: on the one hand, in a certain range, i.e. 1350 ° c-1450 ° C, the fluidity of molten iron increases with the increase of superheat temperature; on the other hand, the shrinkage rate of molten iron also increases with the increase of superheat temperature, and its shrinkage tendency increases. At the same time, the increase of superheat temperature also increases the tendency of hot cracking.
Therefore, based on the consideration of shrinkage defects and mechanical properties of castings, it is believed that the lower limit of temperature of molten iron is about 1380 ° C-1400 ° C, while that of inoculated cast iron is 1420 ° c-1450 ° C, which can basically meet the requirements of casting properties and quality. However, the upper limit of its temperature is relatively complex. For example, for some castings with small and uniform wall thickness, in order to avoid shrinkage defects or even skin piercing at the position with small wall thickness, it is necessary to improve the molten iron fluidity. The upper limit of its molten iron temperature is generally taken as 1500 ° C. However, the upper limit of molten iron temperature is generally below 1400 ° C due to the factors of shrinkage prevention and thermal cracking prevention.
In addition, the porosity of castings can be reduced by increasing the spot temperature. We think that the reason for the porosity of cast iron is that the bubbles formed by the gas in the molten iron are blocked by the oxide film on the surface of the liquid surface and cannot be discharged. On the one hand, increasing the pouring temperature can increase the pressure of the gas discharged from the molten iron, on the other hand, it can also push the time of forming the oxide film on the liquid surface, which makes it difficult to form the oxide film on the surface of the molten iron.
Therefore, the pouring temperature should not be too high or too low in order to prevent shrinkage and reduce porosity. Because of the different production conditions, the view of the mask temperature is also different. Some data even think that the best pouring temperature is from 1395 ° C to 1420 ° C. However, according to the author’s work experience, generally the Taozhu temperature is about 1260 ° C to 1370 ° C, and the actual choice of the temperature is determined according to various considerations.