1 Introduction to rapid prototyping manufacturing technology
Rapid prototyping technology is a kind of technology that appeared and rose in the 1980s. This technology originated from the United States and developed rapidly in the world. The principle of this technology is the principle of discrete stacking. In the process of using this technology, advanced technologies such as laser technology and computer technology are used. The material processing method is used for automatic conversion from model to entity, and the converted products have high precision.
2 Main rapid prototyping technology
Compared with other rapid sand casting technologies, SLS (selective laser sintering) technology is characterized by no need of any mechanical auxiliary equipment, high flexibility, good stability, and is suitable for manufacturing complex shape sand mold (core), which is one of the more mature rapid prototyping technologies at present. See Figure 1 for SLS working principle.
Driven by the CAD slicing model, the powder laying device lays powder layer by layer, and the laser beam selectively solidifies the powder to form each cross-section until it is superposed into a solid.
At present, there are two methods of SLS direct sand mold manufacturing, direct sintering process and indirect sintering process. In 2003, the direct sintering process of silica sand was studied by National University of Singapore. It was put forward that a small amount of Al2O3 in silica sand can reduce the melting point of the sand surface, so it can be sintered without binder. The laser power of this method is 140 ~ 200W, but the forming speed is slow, the manufacturing cycle is long, and it requires high equipment, so it has not been widely used.
Like SLS process, 3DP also makes parts by bonding powder into a whole. The difference is that it is not bonded by laser melting, but by the adhesive sprayed by the nozzle. Its detailed working principle is as follows: (1) 3DP’s feeding mode is the same as SLS, when feeding, powder is laid on the printing platform by horizontal roller; (2) The colored glue is delivered to the print head for storage by pressurization; (3) the printing process is similar to that of a 2D ink-jet printer. First, the system will mix the colored glue according to the color of the three-dimensional model and spray it selectively on the powder plane. When the powder meets the glue, it will stick to the solid; (4) after the first layer of bonding, the printing platform will drop, The water pressure pressing rod will pave the powder again, and then start the bonding of a new layer, and print layer by layer until the whole model is bonded; (5) after printing, recover the unbonded powder, blow out the powder on the surface of the model, and soak the model with transparent glue again, at this time, the model will have a certain strength.
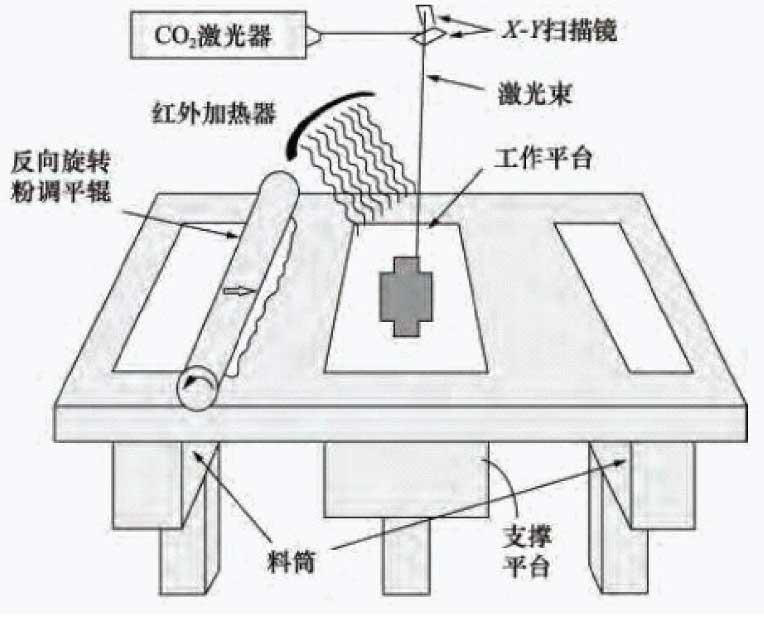
3 Advantages and disadvantages of 3DP process
(1) It has the advantages of fast molding speed, relatively low price, and the powder is bonded by binder instead of sintering in protective atmosphere by other processes.
(2) Full color 3D printing with gradient color can be realized, which can perfectly reflect the designer’s design intention on color.
(3) No supporting materials are needed in the printing process, which not only eliminates the support, but also reduces the use cost.
(4) It can print large pieces.
(5) The mechanical properties of the product are poor, and the strength and toughness are relatively low. Generally, the product can only be used for sample display and cannot be used for functional test.
4 Transfer coating technology
4.1 Introduction to transfer coating technology
Transfer coating technology appeared in the 1970s, which was first proposed by Komatsu in Japan, and the research on this technology in China began in the 1990s. In this technology, the paint is directly sprayed, then sand filled and compacted, and finally solidified. When the mold is lifted, the paint can be directly transferred to the surface of the sand mold, and finally the precise paint sand mold is produced.
4.2 Advantages of transfer coating technology
Transfer coating technology has a strong advantage. Using this technology will not affect the size of the casting. At the same time, the coating can be perfectly copied without some surface defects. It can obtain clean and precise casting. Compared with the ordinary sand casting, its cost is only a little higher. However, its quality improvement is great. It also greatly improves the production efficiency.
In conclusion, we can see that precision sand casting technology has attracted wide attention because of its unique advantages since its birth. The rapid prototyping manufacturing technology in precision sand casting technology can ensure the external accuracy of the casting, and the main rapid prototyping technology includes stereoscopic light curing, layered solid manufacturing, selective laser sintering and deposition molding. Transfer coating technology is used to ensure the internal quality of castings, and this technology also has great advantages. It is hoped that the introduction of all kinds of precision sand casting technology in this paper can arouse the attention of relevant personnel and better develop and apply this technology.