The process of sand casting is a fascinating journey from the raw materials to the final shape of a metal part. Let’s explore the step-by-step process of sand casting:
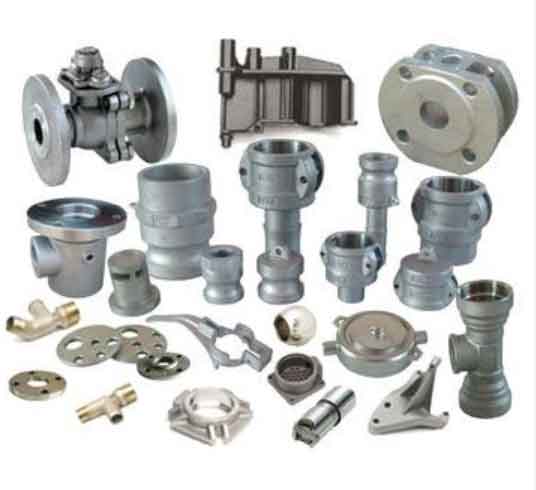
- Pattern Creation:
- The process begins with the creation of a pattern, which is a replica of the desired part.
- Skilled pattern makers create patterns using materials such as wood, plastic, or metal.
- The pattern is slightly larger than the final part to account for the metal shrinkage during cooling.
- Mold Preparation:
- A mold consists of two halves: the cope (top) and the drag (bottom).
- The mold is made by packing specially prepared sand around the pattern.
- Green sand, a mixture of sand, clay, and water, is commonly used for mold making.
- The sand is compacted around the pattern to create the mold cavity, ensuring proper detail and dimensional accuracy.
- Core Placement (if needed):
- Cores are sand shapes inserted into the mold to create internal features or cavities in the final casting.
- Cores are made separately and positioned within the mold to form the desired internal shape of the part.
- Cores are typically made of sand mixed with binders and can be hardened by baking or other curing methods.
- Gating and Riser Design:
- Gating refers to the system of channels that allow the molten metal to flow into the mold cavity.
- Risers, also known as feeders, are additional cavities that act as reservoirs for molten metal to compensate for shrinkage during solidification.
- Proper gating and riser design ensure smooth metal flow, minimize turbulence, and help prevent defects like shrinkage or porosity.
- Melting and Pouring:
- The metal is melted in a furnace to the required temperature and composition.
- Once molten, the metal is poured into the mold cavity through the gating system.
- Care must be taken to ensure a controlled and even pour to fill the mold completely and avoid defects.
- Solidification and Cooling:
- After pouring, the molten metal cools and solidifies within the mold cavity.
- The solidification time depends on the metal type and its mass, and it is essential to prevent premature mold opening, which could lead to defects.
- Cooling rate and the use of insulating materials or controlled cooling techniques can influence the microstructure and properties of the casting.
- Shakeout and Cleaning:
- Once the metal has solidified, the mold is broken open, and the casting, along with the sand, is removed. This process is known as shakeout.
- The casting is separated from the excess sand, which is recycled for future use.
- The casting may require cleaning to remove any remaining sand, fins, or other imperfections.
- Finishing Operations:
- After cleaning, the casting may undergo additional finishing operations, depending on the desired specifications.
- Finishing operations may include grinding, machining, shot blasting, or surface coating to achieve the desired surface finish, dimensional accuracy, and appearance.
- Inspection and Quality Control:
- The castings undergo inspection and quality control measures to ensure they meet the required standards.
- Visual inspection, dimensional checks, and non-destructive testing methods like X-ray or ultrasound are employed.
- Mechanical testing, such as tensile, hardness, or impact tests, may also be conducted to evaluate the casting’s mechanical properties.
- Post-Casting Operations:
- Depending on the application and requirements, post-casting operations like heat treatment, surface coating, or machining may be performed to enhance the casting’s properties or achieve final specifications.
Sand casting is a captivating process that combines traditional craftsmanship with advanced techniques. It allows for the production of a wide range of metal parts, from simple to highly complex, with versatility and cost-effectiveness.