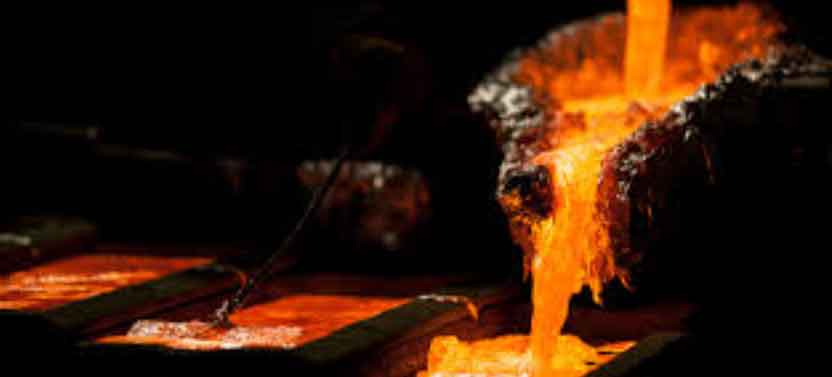
The sand casting industry continues to evolve and adapt to new technologies, materials, and market demands. Leading manufacturers are driving advancements and shaping the future of sand casting through various trends and innovations. Here are some key advancements and trends from leading manufacturers:
- Digitalization and Industry 4.0: Manufacturers are embracing digital technologies and automation to improve the efficiency and accuracy of sand casting processes. This includes the use of advanced simulation software for mold filling and solidification analysis, as well as real-time monitoring systems for process control and optimization.
- 3D Printing and Additive Manufacturing: Additive manufacturing, including 3D printing, is being integrated into the sand casting process. This technology allows for the production of complex sand molds and cores with intricate geometries, reducing the need for traditional pattern-making and enabling faster prototyping and customization.
- Advanced Sand Binder Systems: Manufacturers are exploring advanced binder systems that offer improved performance and environmental sustainability. This includes the development of eco-friendly binders with reduced emissions, improved sand reclamation properties, and enhanced casting quality.
- Lightweight Casting Solutions: With increasing demands for lightweight components in various industries, manufacturers are focusing on lightweight casting solutions. This involves the development of innovative alloys, such as aluminum and magnesium alloys, and the optimization of casting designs to achieve weight reduction while maintaining structural integrity.
- Green Sand Reclamation: Green sand reclamation technologies are gaining momentum as manufacturers seek to reduce waste and optimize sand usage. Advanced sand reclamation systems are being employed to efficiently reclaim and recycle used sand, minimizing the need for new sand and reducing the environmental impact of sand casting.
- Sustainable Material Choices: Manufacturers are exploring sustainable material options for sand casting. This includes the use of recycled materials, such as recycled steel and alloys, as well as the adoption of eco-friendly binders and additives that minimize the environmental footprint of the casting process.
- Collaboration and Partnerships: Leading manufacturers are fostering collaboration and partnerships with research institutions, universities, and other industry stakeholders to drive innovation in sand casting. By working together, they are able to share knowledge, exchange ideas, and accelerate the development of new technologies and processes.
These advancements and trends are shaping the future of sand casting, making it a more efficient, sustainable, and versatile casting method. By staying informed about these developments and partnering with leading manufacturers, industries can benefit from the latest advancements in sand casting technology and achieve high-quality castings for their applications.