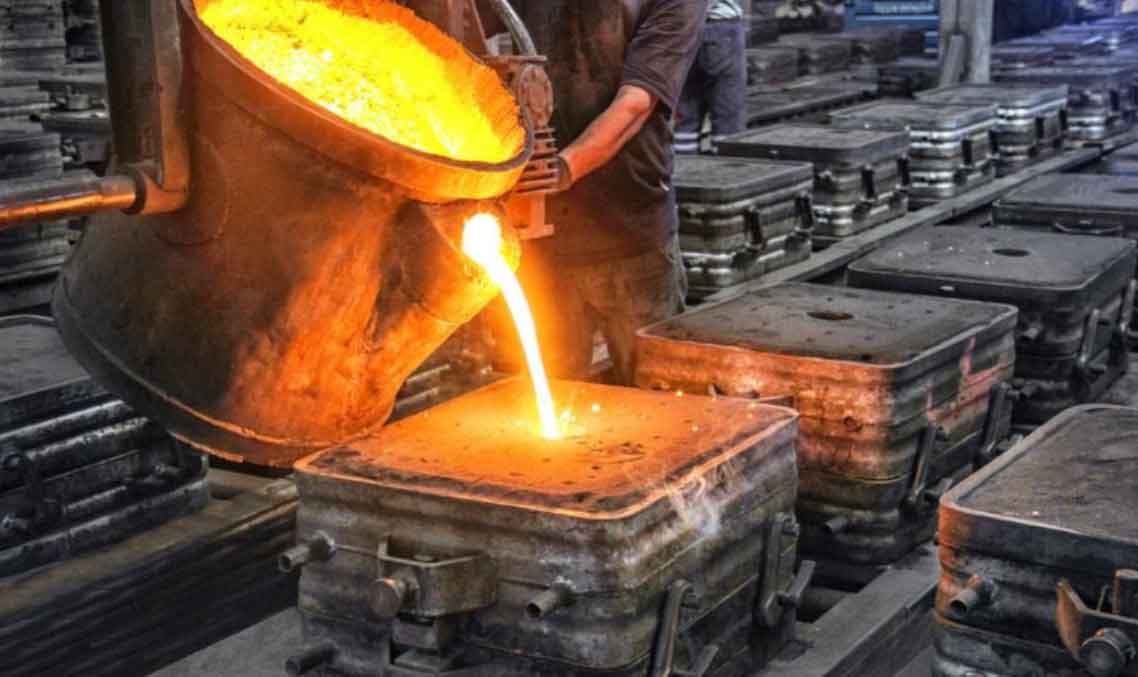
Here are some trends and forecasts for the future of sand casting manufacturing:
1. Adoption of Digitalization and Industry 4.0:
- Sand casting foundries are expected to embrace digitalization and Industry 4.0 technologies to improve process efficiency, data analysis, and automation. The integration of advanced sensors, real-time monitoring, and data analytics will enable better process control and optimization.
2. Advanced Simulation and Modeling Tools:
- The use of advanced simulation and modeling tools in sand casting will continue to grow. Foundries will rely on these tools to optimize mold design, gating systems, and solidification processes, leading to improved casting quality and reduced development time.
3. Sustainable and Eco-Friendly Practices:
- There will be an increased focus on sustainability in sand casting manufacturing. Foundries will explore eco-friendly binder systems, waste reduction, and energy-efficient processes to minimize environmental impact and comply with evolving regulations.
4. Integration of Additive Manufacturing:
- Additive manufacturing, such as 3D printing, will play a role in sand casting. 3D printing can be used for rapid prototyping, producing complex cores and patterns, and creating custom tooling, reducing lead times and costs.
5. Advancements in Sand Reclamation:
- Sand reclamation technologies will continue to evolve, enabling foundries to recycle and reuse sand more effectively. This will help reduce material waste and production costs.
6. Automation and Robotics:
- The use of automation and robotics will increase in sand casting manufacturing to handle tasks such as mold handling, core assembly, and post-casting finishing. This will enhance productivity and improve workplace safety.
7. Lightweight Materials for Automotive and Aerospace:
- As industries seek lightweight materials for improved fuel efficiency and performance, sand casting foundries may see increased demand for castings using lightweight alloys, such as aluminum and magnesium, in automotive and aerospace applications.
8. Customization and Low-Volume Production:
- Sand casting’s flexibility will continue to attract applications requiring customized components and low-volume production. Foundries will cater to specialized industries with unique requirements.
9. Digital Connectivity and Remote Collaboration:
- Digital connectivity will facilitate remote collaboration between foundries and customers, allowing real-time communication, data sharing, and virtual inspections.
10. Advancements in Quality Control and Non-Destructive Testing:
- Quality control methods, including non-destructive testing techniques, will advance to ensure the highest casting quality and to meet stringent industry standards.
It’s important to note that the future of sand casting manufacturing will be influenced by technological advancements, market demands, and environmental considerations. As the manufacturing landscape evolves, sand casting foundries will continue to adapt to new challenges and opportunities to remain competitive in the global market.