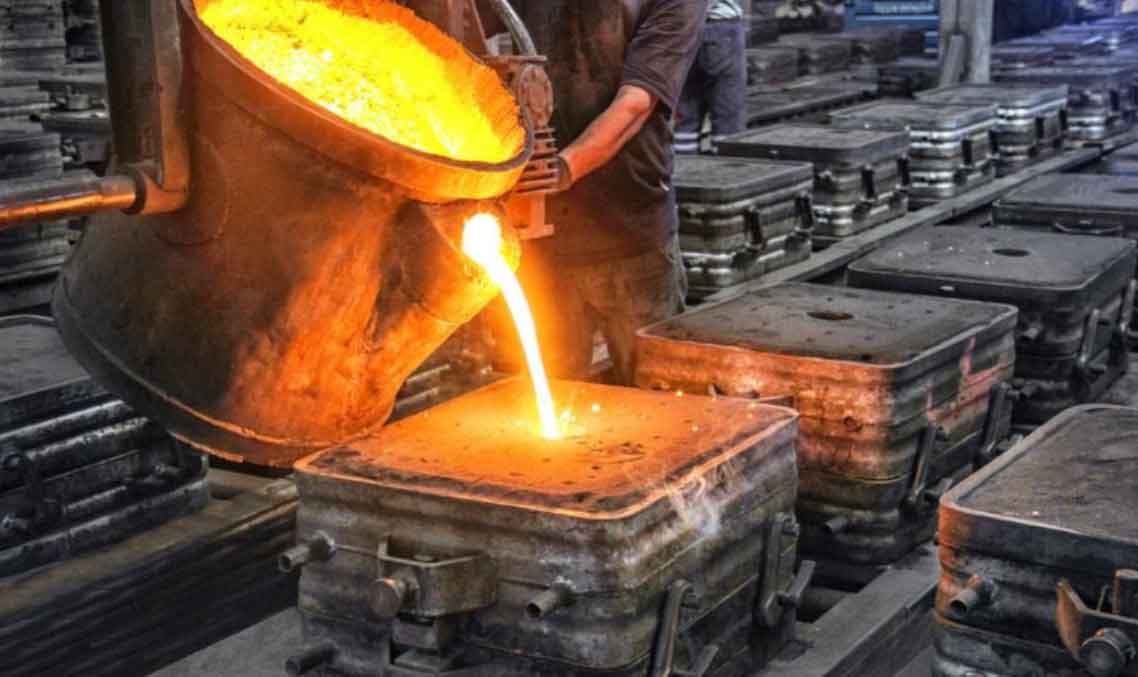
Digitalization has had a profound impact on sand casting manufacturing processes, transforming traditional practices into more efficient, data-driven, and technologically advanced operations. The integration of digital technologies into sand casting has led to improved productivity, enhanced quality control, streamlined workflows, and greater sustainability. Here are some key ways digitalization has influenced sand casting manufacturing processes:
1. Design and Simulation:
- Digital tools, such as computer-aided design (CAD) software and casting simulation software, enable engineers to create intricate casting designs, optimize geometries, and predict potential defects. This reduces the need for physical prototypes and minimizes design iterations, leading to faster development cycles.
2. Rapid Prototyping:
- Digitalization allows for rapid prototyping using techniques like 3D printing, enabling the quick production of complex patterns and molds. This expedites the design validation process and reduces lead times.
3. Automation and Robotics:
- Automation and robotics have been integrated into various stages of sand casting, such as pattern-making, mold handling, and finishing. This automation improves consistency, reduces manual labor, and enhances overall productivity.
4. IoT and Sensors:
- The Internet of Things (IoT) and sensor technologies are used to monitor and collect real-time data from casting equipment and processes. This data helps manufacturers identify patterns, optimize process parameters, and predict maintenance needs, leading to improved efficiency and reduced downtime.
5. Quality Control and Inspection:
- Digital technologies, including AI and machine vision, are employed for quality control and inspection. Automated inspection systems can identify defects and deviations quickly, ensuring casting conformity and minimizing scrap rates.
6. Data Analytics and Predictive Maintenance:
- Manufacturers use data analytics to analyze production data, identify trends, and make data-driven decisions. Predictive maintenance models help anticipate equipment maintenance needs, reducing unplanned downtime and maximizing equipment uptime.
7. Collaboration and Communication:
- Digitalization enhances collaboration and communication between stakeholders. Teams can share information, collaborate remotely, and make real-time decisions, improving efficiency and reducing miscommunication.
8. Energy Efficiency and Sustainability:
- Digital technologies can optimize energy usage and resource consumption in sand casting manufacturing, contributing to sustainability goals. By optimizing processes, manufacturers can reduce waste and minimize the environmental impact.
9. Process Optimization:
- Digitalization enables continuous process optimization. Manufacturers can use data insights to fine-tune process parameters, improve casting quality, and enhance overall efficiency.
10. Supply Chain Integration:
- Digitalization allows for seamless integration with supply chain partners, optimizing material sourcing and inventory management, and improving overall supply chain efficiency.
Overall, digitalization has revolutionized sand casting manufacturing processes, making them more agile, data-driven, and capable of delivering high-quality castings with reduced lead times. By leveraging digital tools and technologies, sand casting manufacturers can stay competitive, respond to market demands faster, and meet the evolving needs of customers in a rapidly changing industrial landscape.