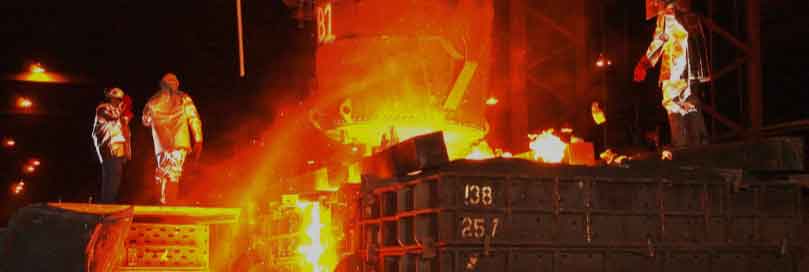
Foundry technology plays a significant role in improving the efficiency and sustainability of industrial processes. Foundries are facilities where metal is melted and cast into various shapes, such as components, machinery parts, and structural elements. By adopting advanced foundry technologies, industries can achieve several benefits in terms of energy efficiency, resource conservation, waste reduction, and environmental impact mitigation. Let’s explore these aspects further:
Energy Efficiency:
Foundry technology has evolved to incorporate energy-efficient practices. Modern foundries utilize advanced furnaces and melting techniques that optimize energy consumption. Induction furnaces, for example, are more efficient than traditional cupola furnaces as they can provide precise and localized heating, reducing energy waste. Additionally, technologies like regenerative burners help recover and reuse waste heat, further enhancing energy efficiency.
Resource Conservation:
Foundries have made significant strides in conserving resources through improved process control and material management. Advanced process modeling and simulation tools enable foundries to optimize parameters such as temperature, cooling rates, and material flow, reducing material waste and improving yield. Moreover, the recycling and reuse of metal scraps and by-products minimize the need for raw materials extraction, conserving natural resources.
Waste Reduction:
Foundry processes generate various types of waste, including sand, slag, and emissions. Sustainable foundry technologies focus on waste reduction and proper disposal. For instance, sand reclamation systems recover and recycle used sand, reducing the demand for new sand and minimizing waste generation. Similarly, advanced filtration and treatment systems mitigate air and water pollution, ensuring compliance with environmental regulations.
Emission Control:
Foundries have implemented measures to control emissions of particulate matter, volatile organic compounds (VOCs), and greenhouse gases. Technologies like baghouse filters, wet scrubbers, and electrostatic precipitators capture and remove pollutants from the flue gases generated during metal melting and casting processes. Additionally, the use of cleaner fuels and energy-efficient practices contributes to reducing carbon emissions.
Process Optimization:
Foundry technology advancements, such as computer-aided design (CAD) and computer-aided manufacturing (CAM), enable better process optimization. CAD/CAM systems facilitate the design and production of more intricate and lightweight components, reducing material usage and energy requirements. Furthermore, digital monitoring and control systems help optimize process parameters in real-time, improving quality, reducing defects, and minimizing rework.
Material Innovation:
Research and development in foundry technology have led to the development of new materials and alloys with improved properties. These advancements enable industries to use lighter and more durable materials, reducing the weight and energy consumption of products. For example, the automotive industry benefits from lightweight cast components that enhance fuel efficiency in vehicles.
Efficiency and sustainability are essential considerations for modern industrial processes, and foundry technology plays a crucial role in achieving these objectives. By embracing advanced technologies, optimizing processes, and adopting sustainable practices, foundries can significantly reduce their environmental impact, conserve resources, and enhance overall operational efficiency.