Ductile iron casting, also known as nodular iron casting or spheroidal graphite iron casting, is a versatile material widely used in various industries due to its exceptional properties. Let’s explore the applications and advantages of ductile iron casting:
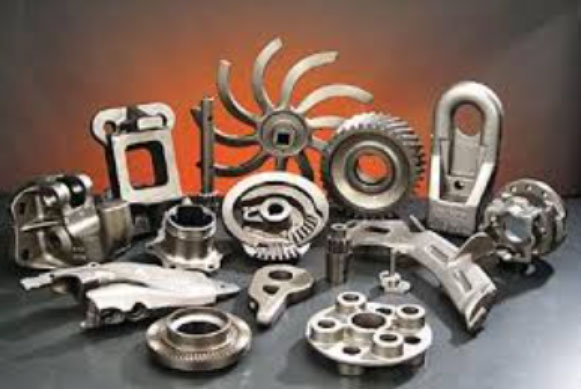
1. Automotive Industry: Ductile iron casting is extensively used in the automotive industry for engine components, transmission parts, suspension systems, brake components, and steering components. Its high strength, excellent wear resistance, and good machinability make it an ideal material for withstanding the demanding conditions of automotive applications.
2. Machinery and Equipment: Ductile iron casting finds applications in a wide range of machinery and equipment, including pumps, valves, hydraulic cylinders, gearboxes, machine frames, and agricultural equipment. Its high strength, toughness, and resistance to wear and impact make it suitable for heavy-duty applications that require reliable and durable components.
3. Pipe and Fittings: Ductile iron casting is commonly used in the production of pipes and fittings for water and wastewater systems, irrigation systems, and industrial piping. Its excellent corrosion resistance, high pressure-bearing capacity, and long service life make it a preferred choice for these applications.
4. Construction Industry: Ductile iron casting is utilized in the construction industry for structural components such as beams, columns, brackets, and connectors. Its strength, stiffness, and durability make it well-suited for supporting heavy loads and providing structural integrity in buildings and infrastructure projects.
5. Power Generation: Ductile iron casting plays a crucial role in the power generation sector. It is used in turbine housings, valve bodies, pump casings, and other components that require high strength, corrosion resistance, and dimensional stability in power plants.
6. Railway and Transportation: Ductile iron casting is employed in railway and transportation systems for components such as rail couplings, brake systems, suspension parts, and chassis components. Its ability to withstand heavy loads, vibration, and impact makes it suitable for these demanding applications.
Advantages of Ductile Iron Casting:
- High Strength and Durability: Ductile iron casting exhibits excellent strength and durability, providing reliable performance in various applications.
- Good Machinability: Ductile iron is relatively easy to machine, allowing for the production of complex shapes and precise components.
- Excellent Wear and Corrosion Resistance: Ductile iron casting offers good resistance to wear and corrosion, extending the lifespan of components in harsh environments.
- High Ductility and Toughness: Ductile iron has higher ductility and toughness compared to grey cast iron, making it more resistant to cracking or fracturing under impact or heavy loads.
- Cost-Effective: Ductile iron casting provides a cost-effective solution due to its lower material cost compared to some other alternatives, along with its long service life and low maintenance requirements.
- Design Flexibility: Ductile iron can be cast into a wide range of shapes and sizes, providing design flexibility for meeting specific application requirements.
Ductile iron casting’s versatility, strength, durability, and cost-effectiveness make it a preferred choice in a wide range of industries. Its ability to withstand demanding conditions, resistance to wear and corrosion, and ease of machining contribute to its widespread use in various critical applications.