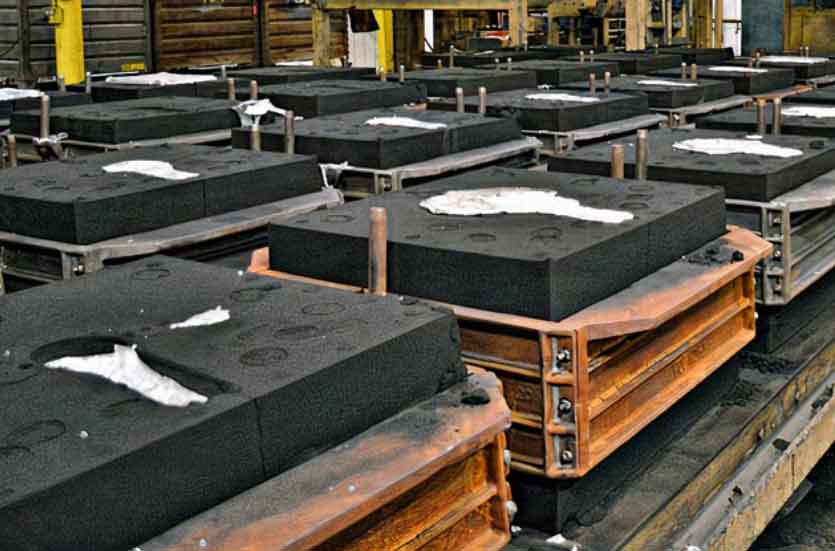
Resin sand casting is a remarkable process that allows for the transformation of imagination and creativity into tangible metal creations. It combines traditional craftsmanship with modern manufacturing techniques to bring ideas to life. Here’s a closer look at how resin sand casting works its magic:
- Design and Pattern Creation: The process starts with the design concept of the desired metal object. This can be a product design, prototype, or customized component. A pattern of the object is then created using various methods, such as carving, CNC machining, or 3D printing. The pattern serves as a replica of the final object to be cast.
- Mold Preparation: A mold is created around the pattern using a mixture of sand and resin. This mold-making process involves packing the sand mixture around the pattern to capture all the intricate details and features. The mold is typically made in two or more halves to facilitate pattern removal and casting.
- Pattern Removal and Mold Assembly: Once the mold has cured, the pattern is removed, leaving behind a cavity in the shape of the pattern within the sand mold. The mold halves are then carefully assembled, ensuring proper alignment and closure.
- Metal Casting: The prepared mold is securely closed, and molten metal is poured into the cavity through a gating system. The metal fills the void left by the pattern, adopting its shape and replicating its details. The molten metal solidifies within the mold.
- Cooling and Solidification: The casting is allowed to cool and solidify within the mold. During this stage, the metal undergoes a phase transformation from liquid to solid, taking on the shape of the mold and preserving the intricate details of the pattern.
- Mold Breakout and Finishing: Once the metal has solidified, the mold is broken open, revealing the solid metal casting. The casting is removed from the mold and undergoes various finishing processes, such as trimming excess material, removing any surface imperfections, and achieving the desired surface finish.
- Post-Casting Processes: Depending on the requirements of the final product, additional post-casting processes may be performed. These processes can include heat treatment, machining, surface coating, or any other necessary steps to achieve the desired specifications.
Through resin sand casting, designers and manufacturers can unleash their imagination and create a wide range of metal objects with intricate details and complex geometries. The process allows for customization, enabling unique designs and tailored solutions. Resin sand casting offers the flexibility to work with various metal alloys, making it suitable for a diverse range of applications across industries.
The magic of resin sand casting lies in its ability to turn abstract ideas into tangible, functional, and visually appealing metal creations. It bridges the gap between imagination and reality, enabling designers and manufacturers to bring their visions to life with precision, accuracy, and artistic expression. Whether it’s intricate jewelry, artistic sculptures, or industrial components, resin sand casting unlocks the potential for turning imagination into tangible creations.