Steel castings manufacturers play a crucial role in modern industry by providing high-quality and precision-engineered components for various applications. Steel castings are widely used across industries due to their exceptional strength, durability, and versatility. Here are some key aspects that highlight the importance of steel castings manufacturers:
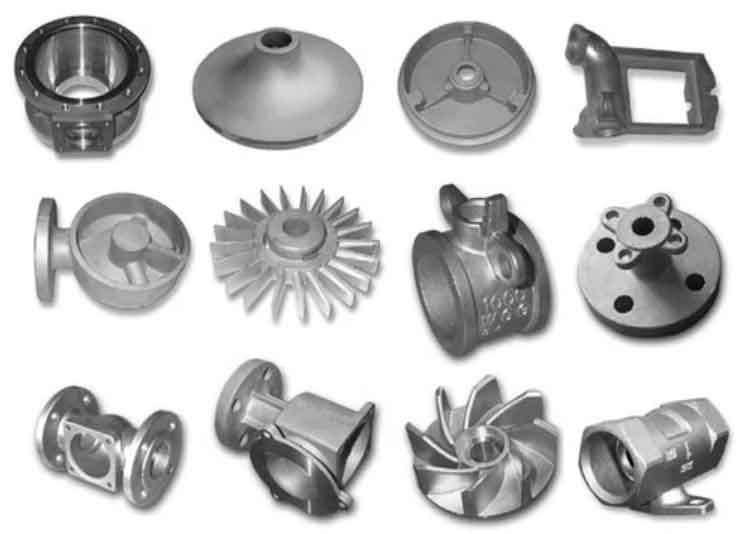
- Diverse Applications: Steel castings find applications in a wide range of industries, including automotive, aerospace, oil and gas, construction, mining, power generation, and many others. They are used to manufacture critical components such as engine parts, turbine blades, pump casings, gears, valves, and more.
- Strength and Durability: Steel castings are known for their exceptional mechanical properties, including high tensile strength, hardness, and impact resistance. This makes them ideal for applications that require reliable performance under demanding conditions.
- Precision Engineering: Steel castings manufacturers employ advanced technologies, such as computer-aided design (CAD) and simulation, to create precise and intricate molds. This precision ensures that the castings meet tight tolerances and dimensional accuracy requirements.
- Customization: Steel castings can be tailored to meet specific requirements of different industries and applications. Manufacturers can produce castings in various shapes, sizes, and configurations, allowing for custom-made components that fit the exact needs of their customers.
- Cost-Effectiveness: Despite the complexity of the casting process, steel castings offer cost-effective solutions for many applications. The ability to produce complex shapes in a single piece reduces the need for additional machining and assembly, leading to overall cost savings.
- Material Selection: Steel castings manufacturers can work with a wide range of steel alloys, each with specific properties suited to different applications. This flexibility allows them to choose the most appropriate material to achieve the desired mechanical properties and corrosion resistance.
- Quality Assurance: Leading steel castings manufacturers implement stringent quality control measures to ensure the highest level of quality in their products. Advanced non-destructive testing (NDT) methods are used to inspect castings for internal defects, ensuring that only flawless components reach the market.
- Innovation and Advancements: Steel casting technology continues to evolve, with constant innovation in materials, casting techniques, and process automation. Manufacturers invest in research and development to stay at the forefront of the industry and meet the evolving needs of their customers.
- Sustainable Practices: Many steel castings manufacturers prioritize sustainability by adopting environmentally friendly practices, such as using recycled materials and optimizing energy consumption during the casting process.
- Contributing to Global Economy: Steel castings manufacturers play a vital role in supporting various industries, contributing to the growth of the global economy. Their products enable the efficient and reliable operation of critical machinery and infrastructure.
Overall, steel castings manufacturers are integral to the success of modern industry. Their expertise in precision engineering, material selection, and quality assurance ensures the production of high-performance components that drive innovation and progress in a wide range of sectors.