The sand casting process is a widely used method for producing metal parts. It involves several steps from mold preparation to the creation of the final product. Here is an overview of the sand casting process:
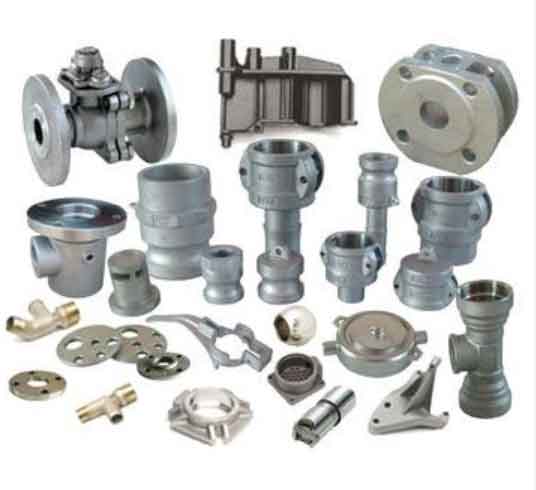
- Pattern Creation: The process begins with the creation of a pattern, which is a replica of the final part. The pattern is typically made of wood, plastic, or metal. It is shaped to match the desired geometry of the part, including features like holes, curves, and surface textures.
- Mold Preparation: A two-part mold is created using the pattern. The mold is made of high-quality sand mixed with a binder to hold its shape. The pattern is placed in a box, and sand is packed around it to create the first half of the mold, called the cope. The pattern is then removed, and the second half of the mold, called the drag, is created using the same process.
- Core Production: If the final part requires internal cavities or intricate shapes, cores are made separately using sand or other materials. Cores are placed in the mold to create the desired internal features of the part.
- Mold Assembly: The cope and drag molds are brought together and securely fastened. Channels, called gating and risers, are created in the mold to allow for the flow of molten metal and to prevent defects like shrinkage. The gating system ensures proper filling of the mold cavity and allows for the escape of gases.
- Melting and Pouring: The desired metal, typically aluminum, iron, or steel, is melted in a furnace at a specific temperature. Once the metal reaches the required temperature, it is poured into the mold through the gating system. The molten metal fills the mold cavity and solidifies.
- Cooling and Solidification: After pouring, the molten metal cools and solidifies within the mold. This process can take some time, depending on the size and complexity of the part. Proper cooling and solidification are crucial to ensure the desired metallurgical properties and prevent defects.
- Mold Removal: Once the metal has solidified, the mold is broken away to reveal the casting. The casting is removed from the mold, and any excess material, such as gates and risers, is removed through cutting or grinding.
- Finishing: The casting may undergo various finishing processes to achieve the desired surface finish and dimensional accuracy. This may include grinding, machining, polishing, or coating. The part is inspected for any defects or imperfections and undergoes quality control checks to ensure it meets the required specifications.
- Final Product: The finished casting is now ready for use or further assembly depending on its intended application.
The sand casting process offers versatility and flexibility for producing a wide range of metal parts. It is widely used in industries such as automotive, aerospace, construction, and more. The process can be adapted to accommodate various sizes, shapes, and complexities, making it a popular choice for producing both small and large-scale parts.