Sand casting is experiencing a resurgence in the manufacturing industry due to its sustainable and reliable nature. Here are some key factors contributing to its renewed popularity:
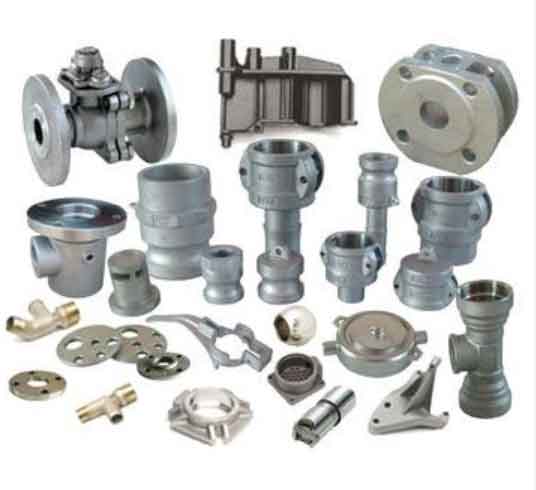
- Environmental Sustainability:
- Sand casting is inherently environmentally friendly compared to other manufacturing methods.
- Sand is a naturally occurring and abundant resource, making it a sustainable choice for mold production.
- Efforts are being made to reduce sand consumption through improved sand reclamation and recycling techniques, minimizing waste and conserving resources.
- The use of eco-friendly binders and additives further enhances the environmental sustainability of sand casting.
- Energy Efficiency:
- Sand casting generally requires lower energy consumption compared to other casting methods.
- Furnaces used for melting the metal can be designed for energy efficiency, reducing the environmental impact.
- Optimized processes and advancements in insulation techniques contribute to improved energy efficiency in sand casting.
- Material Efficiency:
- Sand casting allows for efficient use of materials.
- Sand molds and cores can be made precisely to match the required dimensions of the part, minimizing material waste.
- Additionally, sand can be recycled and reused multiple times, further reducing material consumption and waste generation.
- Versatility and Flexibility:
- Sand casting offers versatility and flexibility in producing a wide range of part sizes and complexities.
- It can accommodate both small and large-scale production, making it suitable for various industries and applications.
- The ability to produce complex geometries and internal features allows for the manufacturing of intricate parts with high precision.
- Reliability and Cost-Effectiveness:
- Sand casting is a proven and reliable manufacturing method with a long history of successful applications.
- It offers a cost-effective solution, particularly for small-scale production or when complex designs are required.
- Lower tooling costs, shorter lead times, and the ability to accommodate design changes contribute to its cost-effectiveness.
- Quality and Customization:
- Sand casting allows for the production of high-quality metal parts with excellent dimensional accuracy and surface finish.
- The process enables customization and the production of unique or specialized parts, meeting specific customer requirements.
- Advanced simulation tools and quality control measures ensure the reliability and consistency of sand castings.
- Collaboration and Craftsmanship:
- Sand casting often involves close collaboration between foundries, pattern makers, and casting engineers.
- Skilled craftsmanship and expertise play a vital role in achieving successful sand castings, ensuring optimal mold preparation, metal pouring, and post-casting processing.
- The combination of traditional craftsmanship and modern technologies creates a reliable and sustainable manufacturing process.
The resurgence of sand casting can be attributed to its sustainable nature, material and energy efficiency, versatility, reliability, and cost-effectiveness. As industries place more emphasis on sustainability and seek reliable manufacturing methods, sand casting provides a sustainable and dependable solution for producing high-quality metal parts.