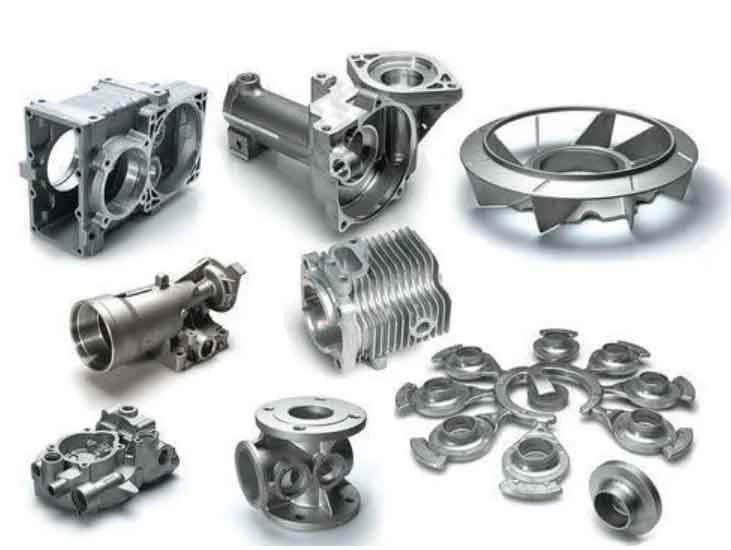
The performance of grey cast iron can be enhanced through the addition of specific alloying elements. These alloying elements modify the microstructure and properties of the cast iron, providing various benefits for specific applications. Here are some common alloying elements and their roles in enhancing the performance of grey cast iron:
- Silicon (Si):
- Role: Silicon is the most common alloying element in grey cast iron. It promotes the formation of graphite flakes during solidification, improving the cast iron’s machinability, thermal conductivity, and damping capacity.
- Benefits: Higher silicon content increases the formation of graphite, enhancing the self-lubricating properties and reducing the brittleness of the cast iron.
- Manganese (Mn):
- Role: Manganese enhances the strength and hardness of grey cast iron by promoting the formation of pearlite in the matrix. It also helps in deoxidation during the casting process.
- Benefits: Increased manganese content improves the mechanical properties and wear resistance of the cast iron.
- Nickel (Ni):
- Role: Nickel increases the hardness and toughness of grey cast iron and enhances its resistance to thermal shocks.
- Benefits: Cast iron with nickel exhibits improved impact resistance and thermal stability, making it suitable for applications subjected to sudden temperature changes.
- Chromium (Cr):
- Role: Chromium enhances the wear resistance and corrosion resistance of grey cast iron.
- Benefits: Cast iron with chromium is well-suited for wear-resistant applications, such as pump impellers and wear plates, where abrasion and erosion are prominent.
- Copper (Cu):
- Role: Copper improves the fluidity of the molten metal and aids in deoxidation during casting.
- Benefits: Copper can help in achieving better surface finish and casting quality.
- Vanadium (V):
- Role: Vanadium refines the grain structure, leading to improved mechanical properties and wear resistance.
- Benefits: Cast iron with vanadium exhibits increased strength, hardness, and wear resistance, making it suitable for wear-resistant components.
- Titanium (Ti):
- Role: Titanium combines with carbon to form titanium carbides, which improve the wear resistance of grey cast iron.
- Benefits: Cast iron with titanium has increased wear resistance and can withstand abrasive conditions.
It is essential to note that the effects of alloying elements can vary depending on their concentration and the overall composition of the grey cast iron. The selection of alloying elements should be based on the specific requirements of the application and the desired properties of the final product.
Alloying elements allow manufacturers to tailor the properties of grey cast iron to meet the demands of diverse industrial applications. By incorporating the right combination of alloying elements, grey cast iron can be optimized for wear resistance, strength, thermal conductivity, and other critical performance characteristics.