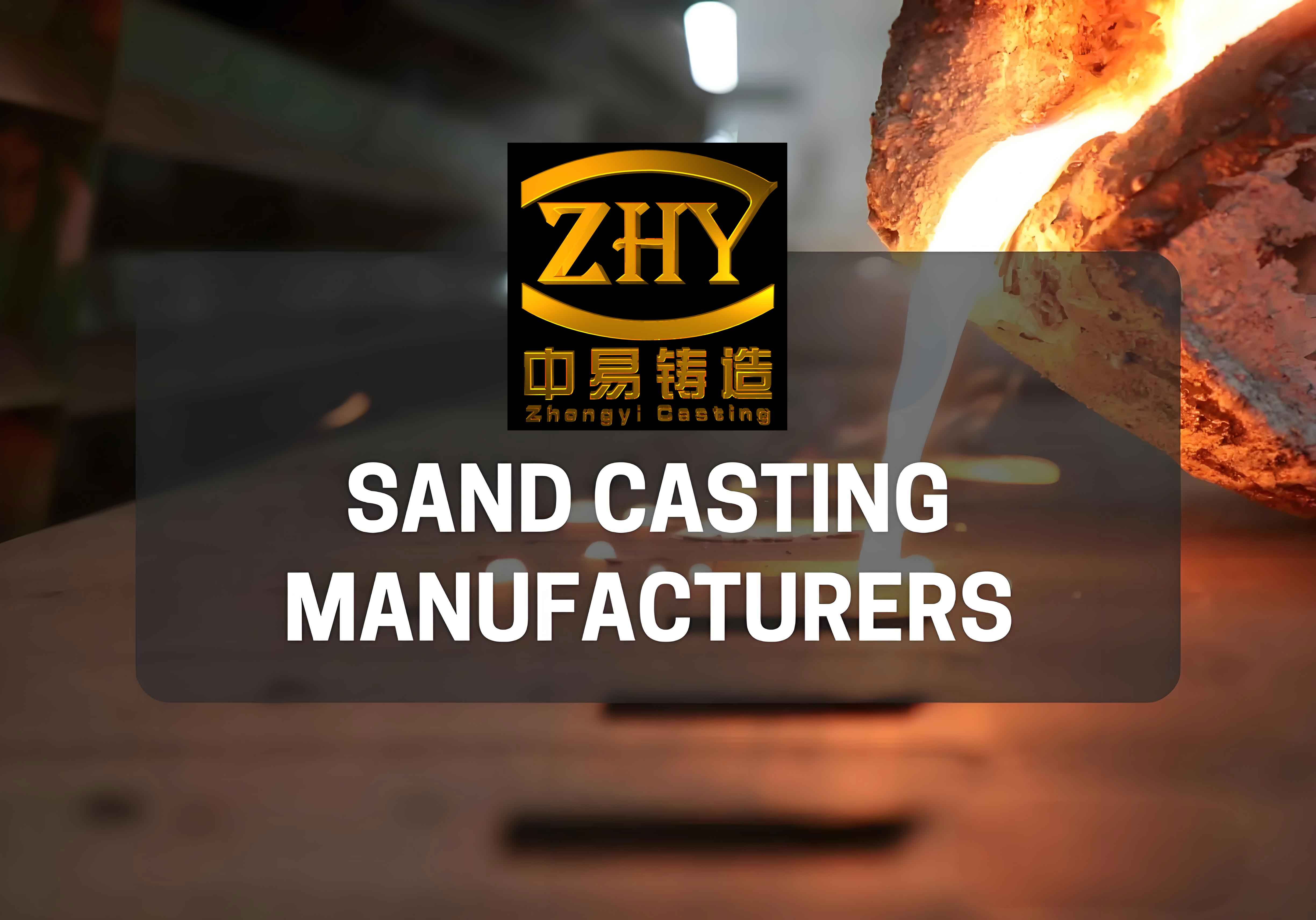
Sand casting has been a fundamental manufacturing process for centuries, allowing for the creation of complex metal parts through the use of sand molds. As technology has evolved, so too has the sand casting process. Automation, in particular, has played a crucial role in transforming modern sand casting manufacturers, enhancing efficiency, precision, and overall productivity. This article explores the various ways automation is revolutionizing the sand casting industry, highlighting its benefits, challenges, and future prospects.
Introduction to Sand Casting
Sand casting involves creating a mold from sand and pouring molten metal into it to form the desired shape. The process is versatile, allowing for the production of large and complex parts that would be difficult or impossible to make using other methods. Traditional sand casting techniques, while effective, often require significant manual labor and are prone to human error. This is where automation steps in, offering a range of benefits that can significantly improve the manufacturing process.
Benefits of Automation in Sand Casting
- Increased Efficiency:
- Automated systems can operate continuously, reducing downtime and increasing the overall throughput of a sand casting manufacturer.
- Machines can perform repetitive tasks faster and with greater consistency than human workers, leading to higher production rates.
- Enhanced Precision and Quality:
- Automation minimizes human error, ensuring that each cast part meets exact specifications.
- Advanced robotic systems can handle delicate tasks, such as mold preparation and metal pouring, with a high degree of accuracy.
- Cost Reduction:
- While the initial investment in automation technology can be substantial, the long-term savings are significant due to reduced labor costs and increased productivity.
- Automated systems also reduce the likelihood of costly mistakes and rework.
- Improved Safety:
- Automation reduces the need for human workers to perform dangerous tasks, such as handling hot metals and heavy molds.
- Safety systems can be integrated into automated processes to monitor and mitigate potential hazards.
Key Areas of Automation in Sand Casting
Mold Making
Automated mold-making machines can create precise molds quickly and efficiently. These machines use computer-aided design (CAD) data to ensure that each mold is an exact replica of the desired part. Automated mold making not only speeds up the production process but also improves the consistency and quality of the molds.
Core Making
Cores are used in sand casting to create internal cavities within cast parts. Automated core-making machines can produce complex cores with a high degree of accuracy. These machines can handle various core materials and binders, ensuring optimal performance for different casting applications.
Metal Pouring
Automated pouring systems can control the flow of molten metal into the molds with precision. These systems can adjust the pouring speed and temperature to ensure optimal casting conditions, reducing the risk of defects and improving the overall quality of the cast parts.
Shakeout and Finishing
Once the metal has solidified and the casting is complete, automated shakeout systems can remove the sand from the cast parts efficiently. Automated finishing systems can then perform tasks such as grinding, trimming, and polishing, ensuring that the final parts meet the required specifications.
Automation Technologies in Sand Casting
Technology | Description | Benefits |
---|---|---|
Robotics | Robots are used for tasks such as mold making, core making, and metal pouring. | High precision, reduced labor costs |
CNC Machines | Computer Numerical Control (CNC) machines create molds and cores with exact dimensions. | Enhanced accuracy, consistent quality |
AI and Machine Learning | Artificial Intelligence (AI) and machine learning algorithms optimize the casting process. | Improved efficiency, predictive maintenance |
IoT Devices | Internet of Things (IoT) devices monitor and control various aspects of the casting process. | Real-time monitoring, improved safety |
Challenges of Automation in Sand Casting
Despite the numerous benefits, there are challenges associated with integrating automation into sand casting manufacturers.
- High Initial Investment:
- The cost of purchasing and implementing automated systems can be prohibitive for small and medium-sized manufacturers.
- Technical Complexity:
- Automation technologies require specialized knowledge for installation, operation, and maintenance, necessitating ongoing training and support.
- Integration Issues:
- Integrating new automated systems with existing manufacturing processes and equipment can be complex and time-consuming.
Future Prospects of Automation in Sand Casting
The future of automation in sand casting manufacturers looks promising, with advancements in technology poised to further enhance the process. Emerging trends include:
- Increased Use of AI and Machine Learning:
- AI and machine learning will play a more significant role in optimizing casting processes, predicting maintenance needs, and improving overall efficiency.
- Greater Adoption of IoT:
- IoT devices will become more prevalent, providing real-time data and analytics to monitor and improve the sand casting process.
- Development of Advanced Materials:
- New materials and binders for mold and core making will be developed, offering improved performance and sustainability.
Conclusion
Automation is revolutionizing the sand casting industry, bringing numerous benefits to modern sand casting manufacturers. From increased efficiency and precision to enhanced safety and cost savings, automated systems are transforming the way cast parts are produced. While challenges remain, the future of automation in sand casting is bright, with ongoing advancements set to further improve the process and drive the industry forward.
By embracing automation, sand casting manufacturers can stay competitive in an increasingly demanding market, delivering high-quality products with greater efficiency and consistency. As technology continues to evolve, the role of automation in sand casting will only become more integral, shaping the future of manufacturing for years to come.