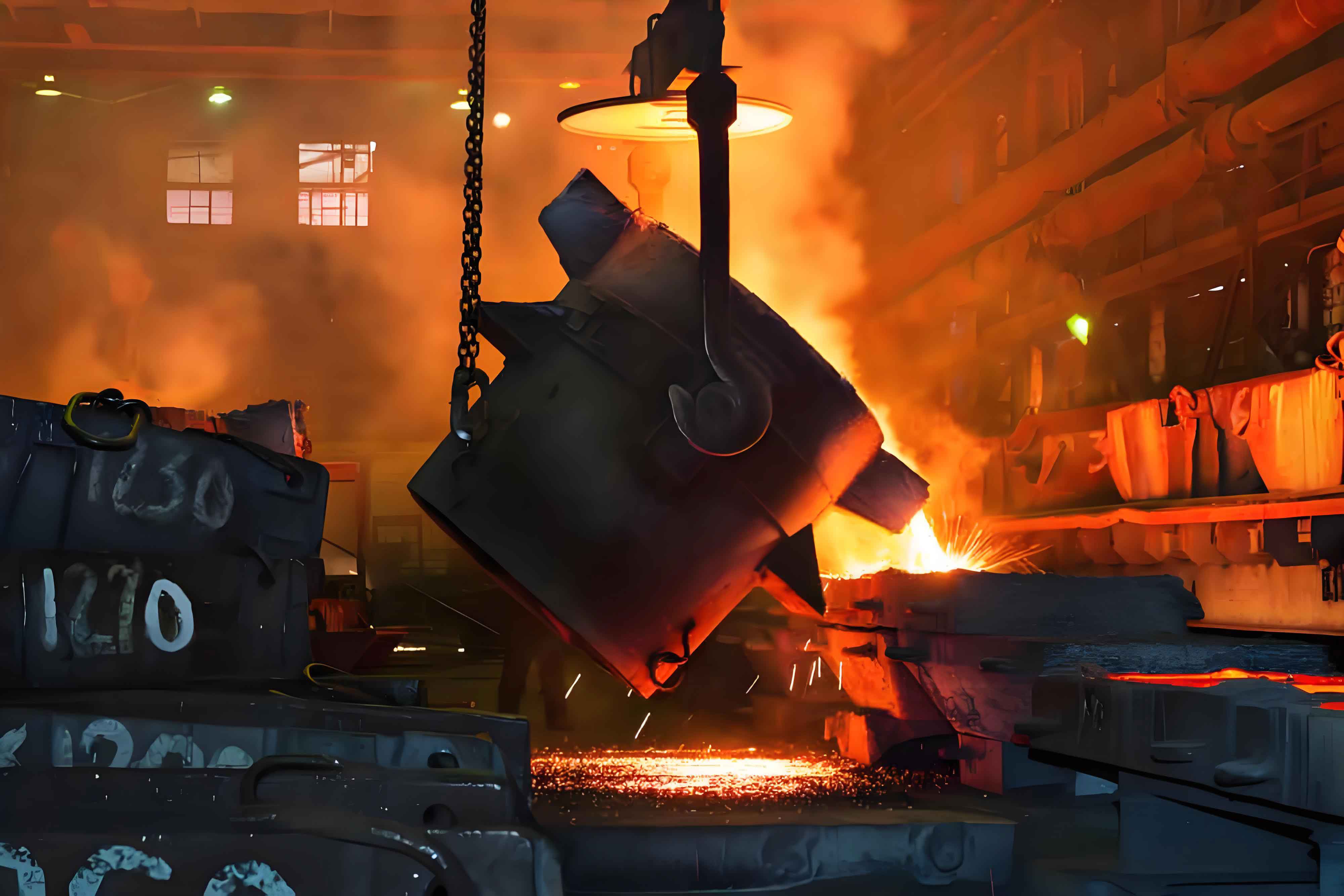
Grey cast iron is a widely used material in various industries due to its excellent castability, machinability, and vibration damping properties. However, its mechanical properties and durability can be significantly enhanced through the application of various heat treatment processes. This article explores the role of heat treatment in improving the durability of grey cast iron, detailing the types of heat treatment processes, their effects on the material’s microstructure, and the resulting improvements in mechanical properties.
Introduction to Grey Cast Iron
Grey cast iron, named for the grey color of its fractured surface, is a type of cast iron characterized by its graphite flake microstructure. This microstructure imparts excellent vibration damping and thermal conductivity properties, making grey cast iron ideal for applications such as engine blocks, machine bases, and brake discs. However, the presence of graphite flakes also contributes to its relatively low tensile strength and brittleness.
Composition of Grey Cast Iron
Grey cast iron typically consists of:
- Carbon: 2.5-4.0%
- Silicon: 1.0-3.0%
- Manganese: 0.2-1.0%
- Sulfur and Phosphorus: Less than 0.1%
Heat Treatment Processes for Grey Cast Iron
Heat treatment processes are employed to alter the microstructure of grey cast iron, thereby enhancing its mechanical properties and durability. The most common heat treatment processes for grey cast iron include annealing, normalizing, quenching, and tempering.
Annealing
Annealing involves heating grey cast iron to a specific temperature, holding it at that temperature for a period, and then slowly cooling it.
- Process: Heating to 800-900°C, holding for several hours, followed by slow cooling in a furnace.
- Benefits: Reduces internal stresses, increases ductility, refines grain structure.
- Applications: Improves machinability and reduces hardness for components such as gears and engine blocks.
Normalizing
Normalizing is a heat treatment process that involves heating grey cast iron to a temperature above its critical range, followed by air cooling.
- Process: Heating to 850-950°C, holding for a period, followed by air cooling.
- Benefits: Produces a uniform microstructure, enhances mechanical properties, increases toughness.
- Applications: Used for components requiring improved mechanical properties and structural uniformity, such as machine frames and crankshafts.
Quenching
Quenching involves rapidly cooling grey cast iron from a high temperature by immersing it in a quenching medium such as water, oil, or air.
- Process: Heating to 850-950°C, followed by rapid cooling in a quenching medium.
- Benefits: Increases hardness and strength, forms a martensitic microstructure.
- Applications: Suitable for components that require high hardness and wear resistance, such as wear plates and cutting tools.
Tempering
Tempering is a heat treatment process that involves reheating quenched grey cast iron to a lower temperature, followed by controlled cooling.
- Process: Reheating to 250-500°C, holding for a period, followed by air cooling.
- Benefits: Reduces brittleness, increases toughness, refines microstructure.
- Applications: Applied to quenched components to improve toughness and reduce internal stresses.
Heat Treatment Process | Temperature Range (°C) | Cooling Method | Primary Benefits | Applications |
---|---|---|---|---|
Annealing | 800-900 | Slow cooling | Reduces stresses, increases ductility | Gears, engine blocks |
Normalizing | 850-950 | Air cooling | Enhances mechanical properties | Machine frames, crankshafts |
Quenching | 850-950 | Rapid cooling | Increases hardness and strength | Wear plates, cutting tools |
Tempering | 250-500 | Air cooling | Reduces brittleness, increases toughness | Quenched components requiring improved toughness |
Effects of Heat Treatment on Grey Cast Iron Microstructure
Heat treatment processes alter the microstructure of grey cast iron, which in turn affects its mechanical properties and durability. The primary microstructural changes induced by heat treatment include the transformation of graphite flakes, refinement of grain structure, and formation of different phases such as ferrite, pearlite, and martensite.
Transformation of Graphite Flakes
During heat treatment, the size, shape, and distribution of graphite flakes in grey cast iron can be modified. Annealing tends to round off the sharp edges of graphite flakes, reducing stress concentrations and improving ductility. Normalizing and quenching can refine the graphite structure, enhancing the material’s strength and toughness.
Grain Structure Refinement
Heat treatment processes such as annealing and normalizing refine the grain structure of grey cast iron. Finer grains result in improved mechanical properties, including increased strength, hardness, and toughness. Quenching followed by tempering can produce a fine martensitic structure, significantly enhancing hardness and wear resistance.
Phase Transformation
Heat treatment induces phase transformations in grey cast iron, leading to the formation of different microstructural constituents:
- Ferrite: A soft and ductile phase that improves machinability.
- Pearlite: A mixture of ferrite and cementite that enhances strength and hardness.
- Martensite: A hard and brittle phase formed during quenching, providing high hardness and wear resistance.
Heat Treatment Process | Microstructural Changes | Resulting Phases | Mechanical Property Improvements |
---|---|---|---|
Annealing | Rounds off graphite flakes, refines grains | Ferrite, pearlite | Increased ductility, improved machinability |
Normalizing | Refines graphite structure, fine grains | Ferrite, pearlite | Enhanced strength, toughness |
Quenching | Refines graphite structure, forms martensite | Martensite | Increased hardness, wear resistance |
Tempering | Refines martensitic structure | Tempered martensite | Reduced brittleness, increased toughness |
Benefits of Heat Treatment in Grey Cast Iron
Heat treatment offers numerous benefits in improving the durability and mechanical properties of grey cast iron. These benefits include increased strength, hardness, toughness, wear resistance, and overall performance.
Increased Strength and Hardness
Heat treatment processes such as quenching and tempering significantly increase the strength and hardness of grey cast iron. The formation of martensite during quenching provides high hardness, while tempering reduces brittleness and enhances toughness.
Improved Toughness and Ductility
Annealing and normalizing improve the toughness and ductility of grey cast iron by refining the grain structure and reducing stress concentrations. These processes make the material more resistant to impact and deformation, extending its service life.
Enhanced Wear Resistance
The increased hardness and refined microstructure resulting from heat treatment enhance the wear resistance of grey cast iron. Components such as wear plates and cutting tools benefit from improved durability and longer service life.
Reduced Internal Stresses
Annealing and tempering reduce internal stresses in grey cast iron, preventing the formation of cracks and other defects. This improves the reliability and performance of cast components in demanding applications.
Benefits of Heat Treatment | Resulting Improvements |
---|---|
Increased Strength and Hardness | Enhanced strength and hardness, improved wear resistance, suitable for high-stress applications |
Improved Toughness and Ductility | Better impact resistance, reduced brittleness, extended service life |
Enhanced Wear Resistance | Increased durability, longer service life of components exposed to wear and abrasion |
Reduced Internal Stresses | Prevention of cracks and defects, improved reliability and performance |
Applications of Heat-Treated Grey Cast Iron
Heat-treated grey cast iron finds applications in various industries where enhanced mechanical properties and durability are required. Some common applications include:
Automotive Industry
- Engine Blocks: Heat-treated grey cast iron engine blocks exhibit improved strength, hardness, and wear resistance, ensuring long-lasting performance.
- Brake Discs: Enhanced wear resistance and thermal stability make heat-treated grey cast iron ideal for brake discs.
- Crankshafts: Improved toughness and fatigue resistance extend the service life of crankshafts.
Machinery and Equipment
- Machine Frames: Increased strength and toughness make heat-treated grey cast iron suitable for heavy-duty machine frames.
- Gear Housings: Improved durability and wear resistance ensure reliable performance of gear housings.
- Press Plates: Enhanced hardness and wear resistance extend the service life of press plates.
Industrial Applications
- Pumps and Valves: Heat-treated grey cast iron offers improved corrosion resistance and durability for pumps and valves.
- Pipe Fittings: Enhanced strength and toughness make heat-treated grey cast iron ideal for high-pressure pipe fittings.
- Industrial Tools: Improved hardness and wear resistance ensure the longevity of industrial tools.
Industry | Applications |
---|---|
Automotive | Engine blocks, brake discs, crankshafts |
Machinery and Equipment | Machine frames, gear housings, press plates |
Industrial | Pumps and valves, pipe fittings, industrial tools |
Conclusion
Heat treatment plays a crucial role in improving the durability and mechanical properties of grey cast iron. Through processes such as annealing, normalizing, quenching, and tempering, the microstructure of grey cast iron can be refined, resulting in increased strength, hardness, toughness, and wear resistance. These improvements extend the service life and reliability of grey cast iron components, making them suitable for a wide range of demanding applications in the automotive, machinery, and industrial sectors. By leveraging the benefits of heat treatment, manufacturers can produce high-quality grey cast iron components that meet the rigorous requirements of modern engineering and manufacturing.