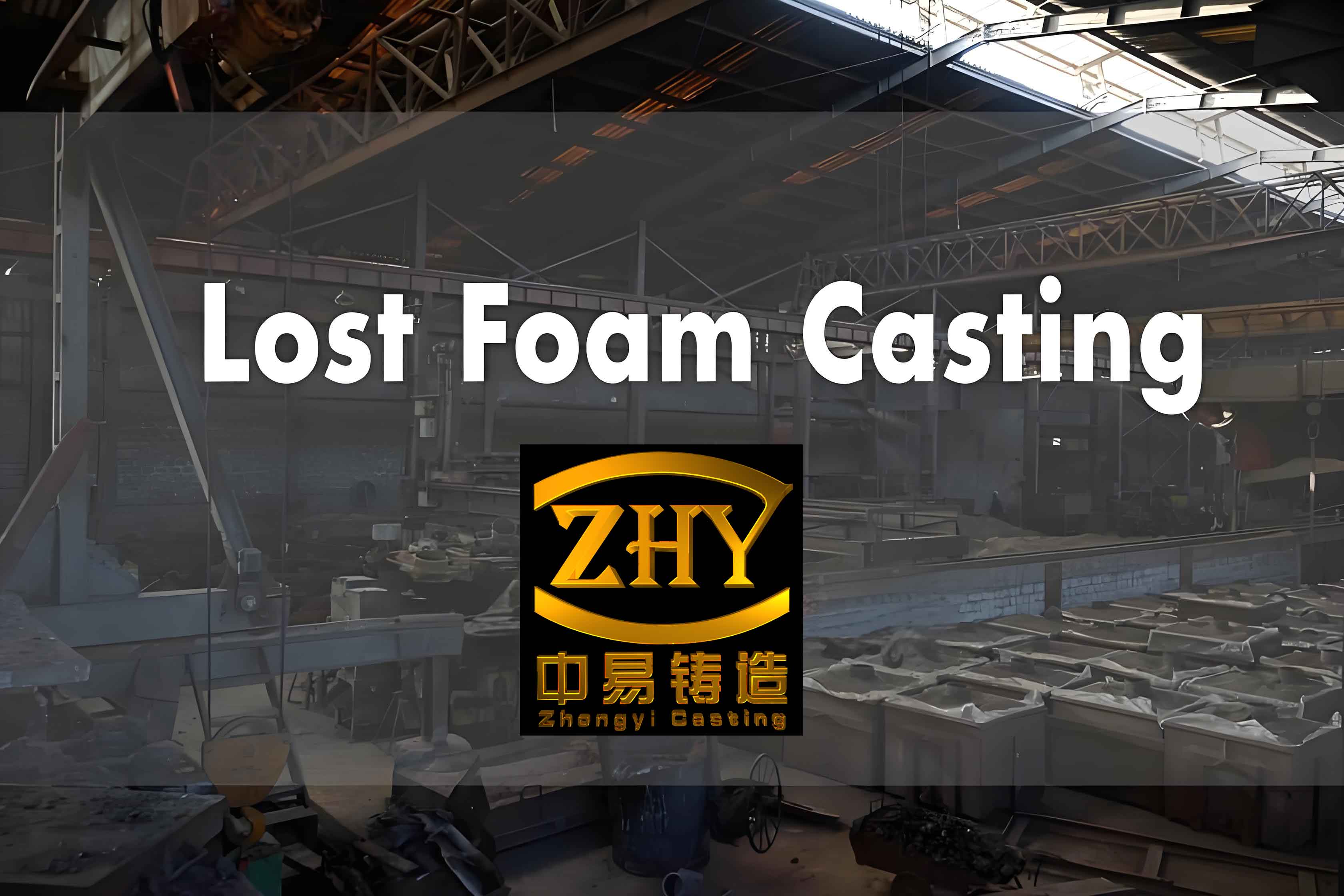
Lost foam casting is a modern and versatile casting technique that allows for the creation of complex metal components with high precision. While the lost foam casting process itself is crucial for producing high-quality parts, post-casting treatments such as heat treatment and surface finishing are equally important for enhancing the mechanical properties and surface characteristics of the final product. This article delves into the significance of heat treatment and surface finishing in lost foam casting, exploring their processes, benefits, and applications.
Lost Foam Casting Overview
Lost foam casting involves creating a foam pattern that is coated with a refractory material and placed in a sand mold. When molten metal is poured into the mold, the foam pattern vaporizes, leaving behind a metal casting that mirrors the original foam design. This method is advantageous for producing components with intricate shapes and thin-walled sections, making it suitable for a wide range of industries.
Steps in Lost Foam Casting
- Foam Pattern Creation:
- A foam model is crafted from polystyrene foam, either by machining or molding.
- Pattern Assembly:
- The foam pattern is assembled with gating systems if required.
- Coating:
- The foam pattern is coated with a refractory material to form a thin shell.
- Mold Preparation:
- The coated foam pattern is placed in a sand mold, and sand is packed around it.
- Metal Pouring:
- Molten metal is poured into the mold, causing the foam pattern to vaporize and be replaced by the metal.
- Mold Breakout:
- Once the metal has solidified, the sand mold is broken away to reveal the metal casting.
- Finishing:
- The casting is cleaned, and any excess material is removed to achieve the final product.
Heat Treatment in Lost Foam Casting
Heat treatment is a critical post-casting process that involves heating and cooling metal castings to alter their microstructure and enhance their mechanical properties. Different heat treatment techniques can be applied to lost foam cast components to achieve specific properties such as improved strength, hardness, and ductility.
Types of Heat Treatment
- Annealing:
- Process: Heating the casting to a specific temperature, holding it for a period, and then slowly cooling it.
- Benefits: Reduces internal stresses, improves ductility, and refines grain structure.
- Applications: Commonly used for castings that require improved machinability and reduced hardness.
- Normalizing:
- Process: Heating the casting to a temperature above its critical range, followed by air cooling.
- Benefits: Produces a uniform grain structure, enhances mechanical properties, and improves toughness.
- Applications: Suitable for castings that need improved mechanical properties and structural uniformity.
- Quenching:
- Process: Rapid cooling of the casting from a high temperature by immersing it in a quenching medium such as water, oil, or air.
- Benefits: Increases hardness and strength by forming a martensitic microstructure.
- Applications: Used for components that require high hardness and wear resistance, such as gears and shafts.
- Tempering:
- Process: Reheating the quenched casting to a lower temperature, followed by controlled cooling.
- Benefits: Reduces brittleness, increases toughness, and refines the microstructure.
- Applications: Applied to castings that have undergone quenching to improve their toughness and reduce internal stresses.
- Solution Heat Treatment:
- Process: Heating the casting to a temperature where alloying elements are fully dissolved, followed by rapid cooling to retain the solution structure.
- Benefits: Enhances strength and corrosion resistance by creating a homogeneous microstructure.
- Applications: Commonly used for aluminum and titanium alloys in aerospace and automotive applications.
Heat Treatment Type | Process Description | Benefits | Applications |
---|---|---|---|
Annealing | Heating and slow cooling | Reduces stresses, improves ductility | Machinability, reduced hardness |
Normalizing | Heating above critical range, air cooling | Uniform grain structure, enhances toughness | Improved mechanical properties, structural uniformity |
Quenching | Rapid cooling in quenching medium | Increases hardness and strength | High hardness and wear resistance (gears, shafts) |
Tempering | Reheating quenched casting, controlled cooling | Reduces brittleness, increases toughness | Toughness improvement after quenching |
Solution Heat Treatment | Heating to dissolve alloying elements, rapid cooling | Enhances strength and corrosion resistance | Aluminum and titanium alloys (aerospace, automotive) |
Surface Finishing in Lost Foam Casting
Surface finishing is an essential post-casting process that enhances the surface quality, appearance, and performance of metal castings. Various surface finishing techniques can be applied to lost foam cast components to improve their aesthetic appeal, corrosion resistance, and wear resistance.
Types of Surface Finishing
- Polishing:
- Process: Mechanically removing surface irregularities using abrasive materials to achieve a smooth and reflective finish.
- Benefits: Enhances aesthetic appeal, improves corrosion resistance, and reduces surface roughness.
- Applications: Suitable for decorative items, medical devices, and components requiring a smooth finish.
- Shot Blasting:
- Process: Propelling abrasive particles at high velocity onto the casting surface to remove scale, rust, and other contaminants.
- Benefits: Cleans and prepares the surface for further finishing, improves surface uniformity, and enhances adhesion for coatings.
- Applications: Used for castings that require a clean and uniform surface, such as automotive parts and machinery components.
- Electroplating:
- Process: Depositing a thin layer of metal onto the casting surface through an electrolytic process.
- Benefits: Enhances corrosion resistance, improves wear resistance, and provides a decorative finish.
- Applications: Commonly used for automotive parts, electrical components, and decorative items.
- Anodizing:
- Process: Electrochemically converting the metal surface into an oxide layer, typically for aluminum alloys.
- Benefits: Increases corrosion resistance, enhances surface hardness, and provides a decorative finish.
- Applications: Suitable for aerospace components, architectural applications, and consumer electronics.
- Painting and Powder Coating:
- Process: Applying a protective and decorative coating of paint or powder to the casting surface.
- Benefits: Provides a protective barrier against corrosion, enhances aesthetic appeal, and offers various color options.
- Applications: Used for automotive parts, industrial equipment, and consumer goods.
Surface Finishing Type | Process Description | Benefits | Applications |
---|---|---|---|
Polishing | Mechanically removing surface irregularities | Enhances aesthetic appeal, improves corrosion resistance | Decorative items, medical devices, smooth finish components |
Shot Blasting | Propelling abrasive particles at high velocity | Cleans surface, improves uniformity, enhances adhesion | Automotive parts, machinery components |
Electroplating | Depositing a thin layer of metal through an electrolytic process | Enhances corrosion and wear resistance, decorative finish | Automotive parts, electrical components, decorative items |
Anodizing | Electrochemically converting surface into an oxide layer | Increases corrosion resistance, enhances hardness | Aerospace components, architectural applications, consumer electronics |
Painting and Powder Coating | Applying protective and decorative coatings | Provides corrosion protection, aesthetic appeal | Automotive parts, industrial equipment, consumer goods |
Benefits of Heat Treatment and Surface Finishing
Enhanced Mechanical Properties
Heat treatment processes such as annealing, quenching, and tempering significantly improve the mechanical properties of lost foam cast components. These treatments enhance the material’s strength, hardness, ductility, and toughness, making the castings suitable for demanding applications.
Improved Surface Quality
Surface finishing techniques like polishing, shot blasting, and electroplating enhance the surface quality of cast components. These methods improve the casting’s aesthetic appeal, reduce surface roughness, and provide a clean and uniform surface, essential for further finishing processes.
Corrosion and Wear Resistance
Heat treatment and surface finishing processes such as anodizing and electroplating enhance the corrosion and wear resistance of metal castings. These treatments create protective layers on the casting surface, preventing corrosion and extending the component’s lifespan.
Aesthetic Enhancement
Surface finishing techniques like polishing, painting, and powder coating significantly enhance the aesthetic appeal of cast components. These methods provide a decorative finish, offer various color options, and improve the overall appearance of the castings.
Versatility and Application
The combination of heat treatment and surface finishing processes allows for the production of high-performance cast components suitable for various industries, including automotive, aerospace, medical, and consumer goods. The enhanced properties and surface quality make these castings ideal for applications requiring high strength, durability, and aesthetic appeal.
Benefits | Heat Treatment | Surface Finishing |
---|---|---|
Enhanced Mechanical Properties | Improves strength, hardness, ductility, toughness | |
Improved Surface Quality | Enhances aesthetic appeal, reduces roughness | |
Corrosion and Wear Resistance | Creates protective layers | Enhances corrosion and wear resistance |
Aesthetic Enhancement | Provides decorative finish, color options | |
Versatility and Application | Suitable for demanding applications | Ideal for various industries |
Conclusion
Heat treatment and surface finishing are integral post-casting processes that significantly enhance the properties and performance of lost foam cast components. Heat treatment techniques such as annealing, quenching, and tempering improve the mechanical properties of the castings, making them suitable for demanding applications. Surface finishing methods like polishing, shot blasting, and electroplating enhance the surface quality, aesthetic appeal, and corrosion resistance of the castings.
By understanding and optimizing these post-casting processes, manufacturers can produce high-quality metal components with superior properties and surface characteristics, meeting the diverse needs of industries ranging from automotive and aerospace to medical and consumer goods. The combination of lost foam casting, heat treatment, and surface finishing ensures the production of durable, reliable, and visually appealing castings, contributing to the overall efficiency and success of manufacturing operations.