Innovation plays a crucial role in the steel castings manufacturing industry, driving advancements in processes, materials, and product development. Here are some insights from top manufacturers on the role of innovation in steel castings manufacturing:
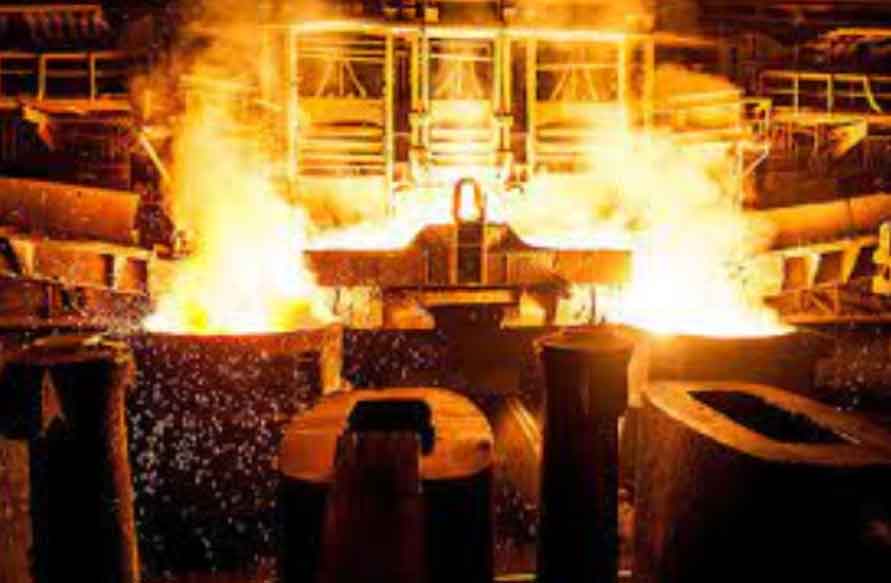
- Process Innovation: Top manufacturers continuously strive to innovate their casting processes to improve efficiency, reduce costs, and enhance quality. They invest in research and development to develop and implement advanced casting techniques such as computer-aided design (CAD), computer-aided engineering (CAE), and simulation tools. These technologies help optimize casting designs, improve process parameters, and minimize defects, leading to higher precision and productivity.
- Material Development: Innovation in material development is a key focus for steel castings manufacturers. They work closely with material suppliers and research institutions to explore new alloys, improve existing ones, and develop specialized materials to meet specific industry requirements. Advancements in alloy composition, heat treatment processes, and surface coatings enable manufacturers to produce castings with superior mechanical properties, corrosion resistance, and durability.
- Design Optimization: Leading manufacturers understand the importance of design optimization in achieving high-quality steel castings. They employ advanced software tools and simulation techniques to analyze casting designs, predict potential defects or weaknesses, and optimize the designs for improved manufacturability and performance. By utilizing virtual prototyping, manufacturers can reduce development time, minimize iterations, and enhance overall product quality.
- Collaborative R&D: Top manufacturers actively engage in collaborative research and development initiatives with customers, suppliers, universities, and research institutions. These partnerships foster knowledge exchange, idea generation, and technology transfer. Collaborative R&D efforts enable manufacturers to stay at the forefront of innovation, address industry challenges, and develop new solutions that meet evolving market demands.
- Automation and Robotics: Automation and robotics play an increasingly significant role in steel castings manufacturing. Leading manufacturers embrace automation technologies to streamline production processes, enhance productivity, and improve safety. Robotic systems are utilized for tasks such as mold handling, pouring, core placement, and finishing operations. Automation not only increases efficiency but also enables manufacturers to maintain consistency and accuracy in their casting processes.
- Sustainability and Environmental Impact: Innovation in steel castings manufacturing is also driven by the need for sustainability and reducing environmental impact. Top manufacturers focus on developing eco-friendly processes that minimize energy consumption, waste generation, and emissions. They explore alternative materials, implement recycling programs, and adopt green technologies to make their operations more sustainable. Innovations in the area of energy-efficient melting furnaces, waste heat recovery systems, and emission control technologies are of particular importance.
- Continuous Improvement: Innovation is a continuous process for top manufacturers in the steel castings industry. They foster a culture of continuous improvement and encourage employees at all levels to contribute ideas and suggestions for process optimization, quality enhancement, and cost reduction. Regular training and skill development programs are implemented to keep the workforce updated on the latest technologies and best practices, fostering an environment of innovation and excellence.
By embracing innovation in processes, materials, and design, top manufacturers in the steel castings industry can deliver high-quality products, improve operational efficiency, and meet the evolving needs of their customers.