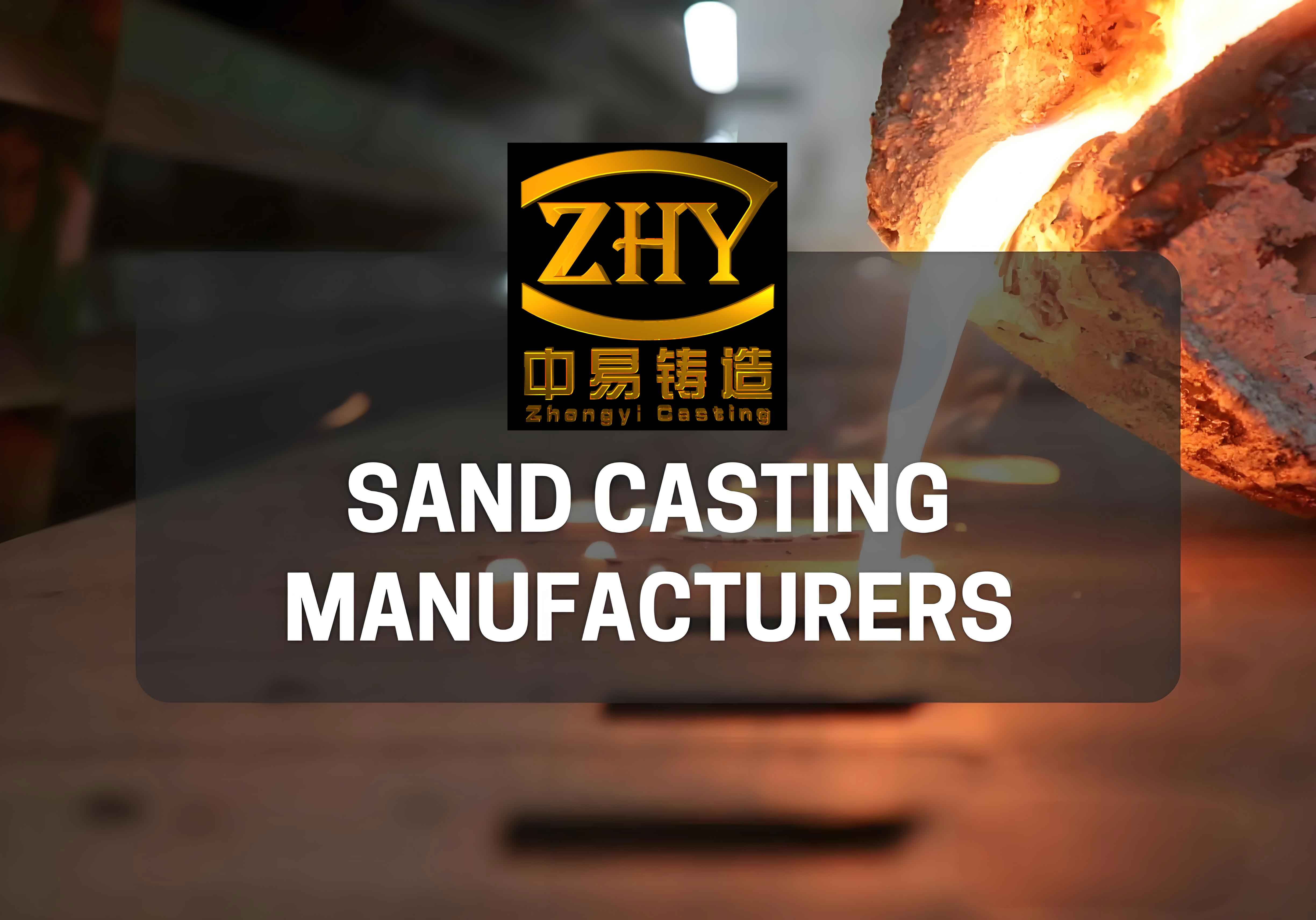
Research and Development (R&D) plays a pivotal role in advancing sand casting manufacturing techniques. As the demand for high-quality, cost-effective, and complex castings continues to grow across various industries, sand casting manufacturers invest heavily in R&D to innovate and improve their processes. This article explores the critical role of R&D in enhancing sand casting manufacturing techniques and highlights key advancements driven by research and development efforts.
The Importance of R&D in Sand Casting Manufacturing
R&D is essential for sand casting manufacturers to stay competitive, meet client needs, and adapt to industry changes. Through R&D, manufacturers can develop new methods, materials, and technologies that enhance the efficiency, quality, and sustainability of sand casting manufacturing.
Key Benefits of R&D in Sand Casting Manufacturing
- Process Optimization: Improving existing processes to enhance efficiency and reduce costs.
- Quality Improvement: Developing techniques to produce higher quality castings with fewer defects.
- Material Innovation: Discovering new materials and alloys that offer better performance and cost-effectiveness.
- Sustainability: Creating environmentally friendly processes and reducing waste.
- Complexity Handling: Advancing techniques to produce more intricate and detailed castings.
Table 1: Key Benefits of R&D in Sand Casting Manufacturing
Benefit | Description |
---|---|
Process Optimization | Enhancing efficiency and reducing costs |
Quality Improvement | Producing higher quality castings with fewer defects |
Material Innovation | Discovering new materials and alloys |
Sustainability | Creating environmentally friendly processes |
Complexity Handling | Producing more intricate and detailed castings |
Advancements in Sand Casting Manufacturing Driven by R&D
1. Process Optimization
R&D efforts in process optimization focus on streamlining sand casting manufacturing to improve productivity and reduce costs.
Techniques for Process Optimization
- Automation: Implementing automated systems for mold making, pouring, and handling to increase precision and reduce human error.
- Simulation Software: Using advanced simulation software to model and optimize casting processes before physical production.
- Lean Manufacturing: Applying lean manufacturing principles to eliminate waste and improve process efficiency.
List 1: Techniques for Process Optimization
- Automation of mold making and pouring.
- Use of advanced simulation software.
- Implementation of lean manufacturing principles.
2. Quality Improvement
Improving the quality of castings is a primary goal of R&D in sand casting manufacturing. Research efforts focus on reducing defects and enhancing the overall quality of the final product.
Techniques for Quality Improvement
- Advanced Inspection Methods: Utilizing non-destructive testing methods such as X-ray and ultrasonic testing to detect and address defects early.
- Enhanced Mold Materials: Developing and using superior mold materials that reduce surface defects and improve dimensional accuracy.
- Process Control: Implementing rigorous process control measures to maintain consistency and quality throughout the production cycle.
Table 2: Techniques for Quality Improvement
Technique | Description |
---|---|
Advanced Inspection Methods | Non-destructive testing to detect defects early |
Enhanced Mold Materials | Using superior materials to improve casting quality |
Process Control | Maintaining consistency and quality |
3. Material Innovation
R&D in material innovation aims to discover and develop new materials that enhance the properties of castings, such as strength, durability, and corrosion resistance.
Examples of Material Innovation
- High-Performance Alloys: Developing new alloys that offer superior mechanical properties and performance.
- Composite Materials: Creating composite materials that combine the benefits of multiple materials to achieve desired properties.
- Eco-Friendly Materials: Researching environmentally friendly materials that reduce the environmental impact of sand casting manufacturing.
List 2: Examples of Material Innovation
- Development of high-performance alloys.
- Creation of composite materials.
- Research into eco-friendly materials.
4. Sustainability
R&D efforts in sustainability focus on reducing the environmental impact of sand casting manufacturing through innovative processes and materials.
Sustainable Practices in Sand Casting Manufacturing
- Recycling Sand: Developing methods to reclaim and reuse sand to reduce waste.
- Energy Efficiency: Implementing energy-efficient technologies and processes to reduce energy consumption.
- Emission Reduction: Creating processes that minimize emissions and environmental pollutants.
Table 3: Sustainable Practices in Sand Casting Manufacturing
Sustainable Practice | Description |
---|---|
Recycling Sand | Reclaiming and reusing sand to reduce waste |
Energy Efficiency | Implementing energy-efficient technologies |
Emission Reduction | Minimizing emissions and environmental pollutants |
5. Complexity Handling
Advancing techniques to handle more complex and intricate castings is a key area of R&D in sand casting manufacturing.
Techniques for Complexity Handling
- Precision Molding: Developing precision molding techniques that allow for the creation of highly detailed and complex castings.
- 3D Printing: Utilizing 3D printing technology to create intricate molds and cores that are difficult to produce with traditional methods.
- Advanced Casting Methods: Researching and implementing advanced casting methods such as investment casting and additive manufacturing to produce complex geometries.
List 3: Techniques for Complexity Handling
- Precision molding for detailed castings.
- 3D printing for intricate molds and cores.
- Advanced casting methods for complex geometries.
Case Study: R&D Advancements in Automotive Sand Casting
An automotive components manufacturer invested in R&D to enhance their sand casting manufacturing techniques. The following table outlines the advancements made and the resulting benefits.
Table 4: Case Study – R&D Advancements and Benefits
Advancement | Description | Benefit |
---|---|---|
Process Automation | Implemented automated mold making and pouring | Increased precision and reduced errors |
Advanced Alloys | Developed high-strength aluminum alloys | Improved durability and performance of parts |
Simulation Software | Used simulation software to optimize casting process | Reduced defects and improved quality |
Sustainable Practices | Recycled sand and used energy-efficient technologies | Lowered environmental impact and costs |
3D Printing | Utilized 3D printing for complex molds | Enabled production of intricate components |
Conclusion
R&D is a driving force behind the continuous advancement of sand casting manufacturing techniques. By investing in research and development, sand casting manufacturers can optimize processes, improve quality, innovate with new materials, enhance sustainability, and handle complex castings with greater precision. These advancements not only meet the evolving needs of clients across various industries but also ensure that sand casting manufacturers remain competitive in a rapidly changing market. Through sustained R&D efforts, the future of sand casting manufacturing holds great promise for even greater innovation and excellence.