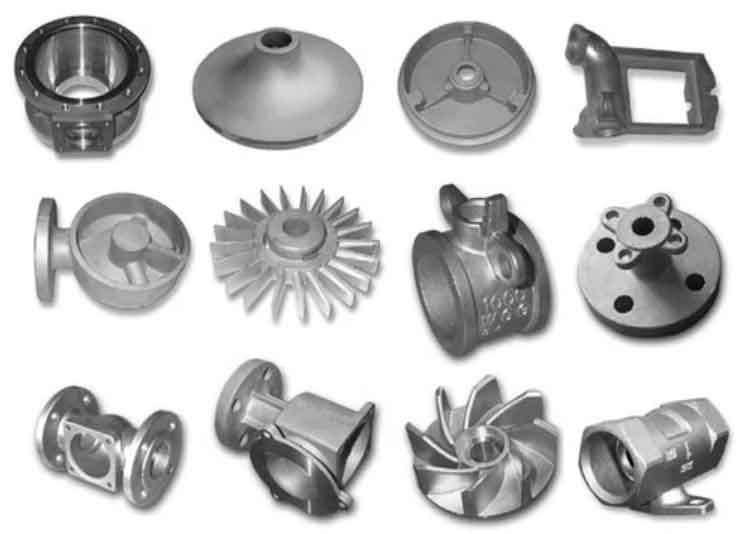
The science of steel castings is a fascinating blend of craftsmanship and cutting-edge technology that enables the creation of high-quality, intricate, and durable components for various industries. Steel castings are made through a complex process that involves precision engineering, metallurgy, and advanced manufacturing techniques. Let’s delve into the science behind steel castings and how it combines the artistry of craftsmanship with modern technological advancements:
- Metallurgy and Material Science: Steel castings manufacturers have a deep understanding of metallurgy and material science. They carefully select the right steel alloys with specific chemical compositions and mechanical properties to meet the requirements of each application. By manipulating alloy compositions and heat treatment processes, they can achieve desired characteristics like hardness, strength, corrosion resistance, and wear resistance.
- Computer-Aided Design (CAD) and Simulation: Steel castings start with the creation of 3D CAD models. Manufacturers use advanced simulation software to analyze the flow of molten metal during casting, predicting potential defects and optimizing the casting process. This digital approach ensures greater accuracy, reduces trial-and-error, and saves time and resources during production.
- Pattern Making and Molding: Craftsmanship comes into play during the pattern-making process. Skilled artisans create patterns in wood, metal, or other materials based on the CAD models. These patterns are used to produce sand molds. Today, modern technology like CNC machining is also used to create patterns with high precision.
- Sand Casting Process: Sand casting is the most common method used for steel castings. The process involves placing the pattern in a sand mold, removing the pattern, and pouring molten steel into the mold cavity. The molten metal solidifies, taking the shape of the pattern and forming the final casting.
- Precision Casting Techniques: In addition to sand casting, steel castings manufacturers may utilize other precision casting techniques such as investment casting (lost-wax casting) or die casting. These methods offer finer details and tighter tolerances for more intricate components.
- Heat Treatment and Quenching: After casting, steel components undergo heat treatment processes like annealing, normalizing, or quenching to achieve the desired metallurgical properties, such as hardness, toughness, and grain structure.
- Non-Destructive Testing (NDT): To ensure the quality of steel castings, manufacturers employ non-destructive testing techniques like X-ray, ultrasonic testing, magnetic particle inspection, or dye penetrant testing. These methods help identify internal defects without damaging the castings.
- Precision Machining: After casting and heat treatment, additional precision machining may be performed to achieve the final dimensions and surface finish required for the application.
- Quality Control and Inspection: Quality control is an essential aspect of steel castings manufacturing. Each casting undergoes rigorous inspection to ensure it meets the specified requirements and standards.
- Environmental Considerations: Modern steel castings manufacturers focus on sustainable practices to minimize their environmental impact. They implement energy-efficient technologies, recycle waste materials, and optimize production processes to reduce carbon footprint.
The science of steel castings combines the heritage of traditional craftsmanship with the advancements of modern technology to create components that are not only strong and durable but also intricate, efficient, and precisely tailored to meet the needs of diverse industries. This seamless integration of artistry and innovation enables the production of high-performance steel castings that drive progress in engineering and manufacturing fields.