Investment casting, also known as lost wax casting, is a complex process that requires careful attention to detail to achieve high-quality and dimensional accuracy in the final cast components. There are several factors and techniques involved in the investment casting process that contribute to the successful production of precise and flawless parts. In this response, we will explore some of the secrets and practices that help achieve high-quality and dimensional accuracy in investment casting.
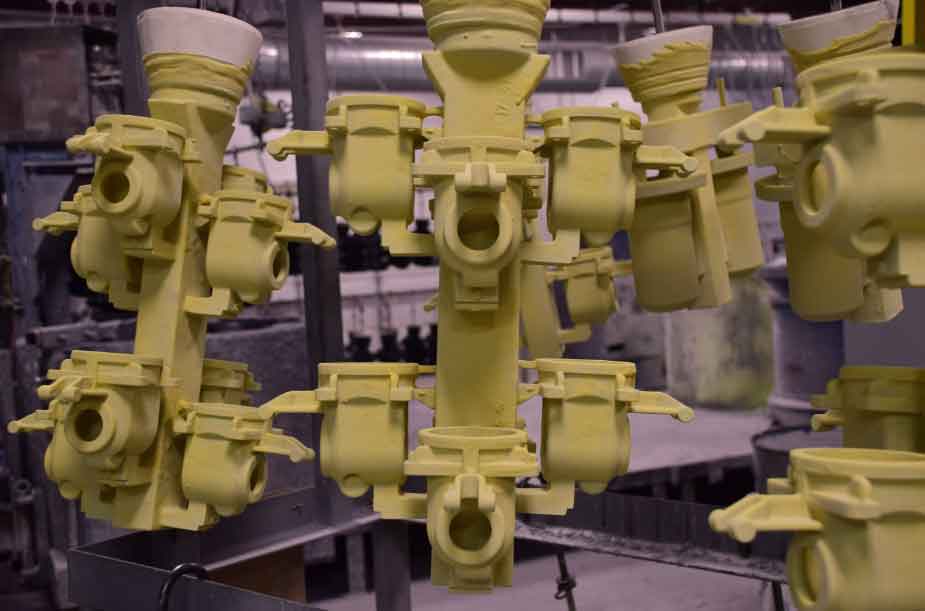
- Wax Pattern Production: The production of accurate and detailed wax patterns is crucial for maintaining dimensional accuracy in investment casting. Whether created through injection molding or manual wax sculpting, the wax patterns should faithfully replicate the design intent. Skilled artisans and technicians ensure that the patterns have consistent wall thickness, proper dimensions, and intricate features.
- Ceramic Shell Formation: The ceramic shell plays a significant role in maintaining dimensional accuracy. Each layer of the ceramic shell is built up carefully to achieve the desired thickness and strength. Proper control of the slurry composition, drying time, and application techniques is essential to ensure uniformity and integrity of the ceramic shell. This helps prevent shell distortion or cracking during the casting process.
- Wax Removal and Preheating: Thorough removal of the wax from the ceramic shell is critical to prevent any residual wax from interfering with the metal casting or causing defects. Controlled heating and ventilation during the wax removal stage help ensure that all traces of wax are eliminated. Additionally, preheating the ceramic shell before the metal pouring stage helps minimize thermal shock and maintain dimensional stability.
- Controlled Metal Pouring: The process of pouring molten metal into the ceramic shell requires precision and control to achieve dimensional accuracy. Factors such as metal temperature, pouring speed, gating system design, and fill direction are carefully optimized. Proper control of these parameters helps ensure complete filling of the mold cavity, avoiding shrinkage, distortion, or voids.
- Cooling and Solidification: The cooling and solidification process after metal pouring also affect dimensional accuracy. Proper cooling rates and techniques are employed to minimize thermal gradients and prevent warping or cracking. Controlled cooling ensures that the metal solidifies uniformly and achieves the desired mechanical properties.
- Shell Removal and Finishing: After solidification, the ceramic shell is carefully removed, and the cast component is subjected to various finishing processes. Finishing techniques, such as machining, grinding, polishing, and heat treatment, are employed to achieve precise dimensions, smooth surfaces, and desired surface finishes. Strict quality control measures, including dimensional inspections and non-destructive testing, are carried out at this stage to ensure the final component meets the required specifications.
- Process Optimization and Expertise: Achieving high-quality and dimensional accuracy in investment casting requires continuous process optimization and expertise. Skilled technicians, engineers, and metallurgists with in-depth knowledge of the investment casting process are involved in every stage. They analyze process parameters, conduct experiments, and make adjustments to optimize the process for specific components, materials, and design requirements.
- Quality Assurance and Testing: Throughout the investment casting process, rigorous quality assurance measures are implemented to identify and rectify any deviations or defects. Advanced inspection techniques, including dimensional metrology, visual inspections, X-ray imaging, and material testing, are employed to ensure compliance with the desired specifications.
In conclusion, achieving high-quality and dimensional accuracy in investment casting involves a combination of precise wax pattern production, careful ceramic shell formation, controlled metal pouring, proper cooling and solidification, meticulous finishing, process optimization, and thorough quality control. These practices, coupled with expertise and continuous improvement, contribute to the successful production of intricate and flawless metal components through investment casting.