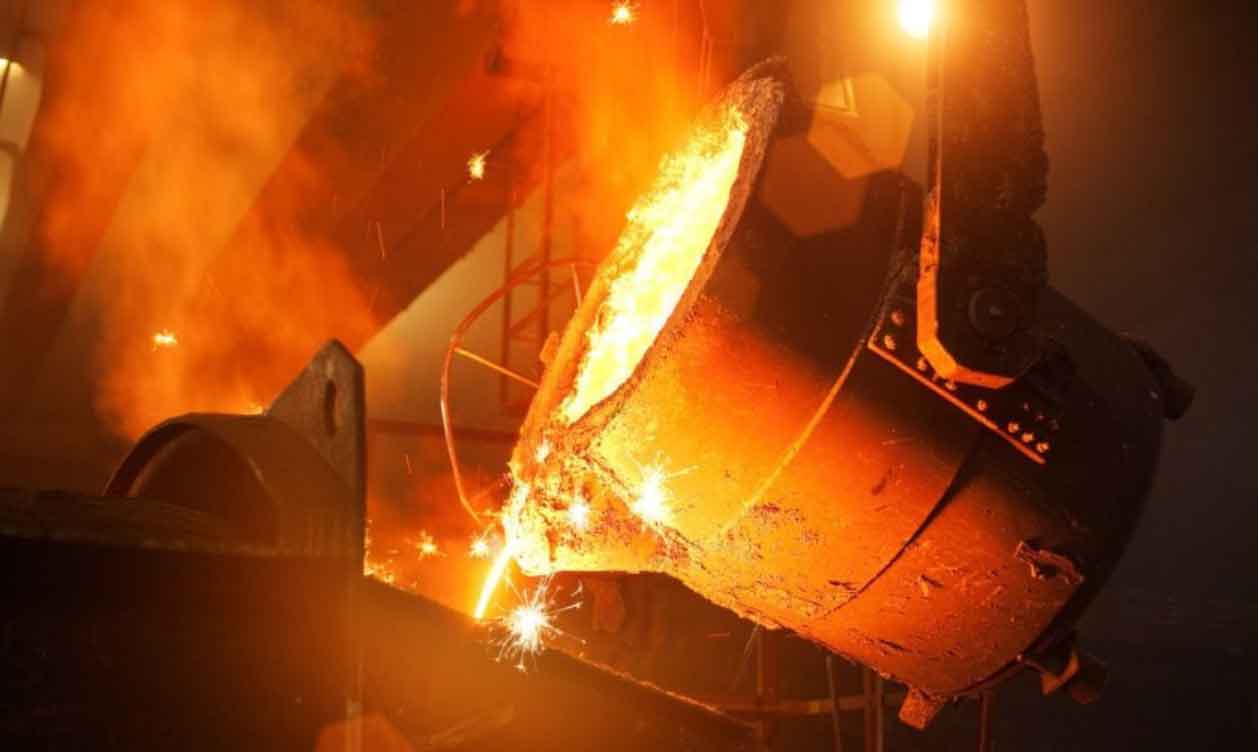
Steel casting is an environmentally sustainable manufacturing process that contributes to a greener future. It offers several advantages that align with sustainability goals and help reduce the environmental impact of metal production. Here are some ways in which steel casting promotes sustainability:
1. Material Efficiency:
Steel casting processes maximize material efficiency by using only the required amount of molten metal for each casting. Near-net shape casting techniques minimize material waste compared to traditional machining processes, where excess material is removed. This reduces the demand for raw materials and conserves valuable resources.
2. Recycling and Reusability:
Steel is highly recyclable and can be melted down and reused multiple times without compromising its properties. Steel castings can be recycled at the end of their lifecycle, reducing the need for virgin materials and minimizing waste. The recycling process consumes less energy compared to primary steel production, leading to lower carbon emissions.
3. Energy Efficiency:
Steel casting processes have become more energy-efficient over time. Foundries have implemented technologies and practices to optimize energy consumption and reduce greenhouse gas emissions. Energy-efficient furnaces, heat recovery systems, and process control systems contribute to lower energy consumption and a reduced carbon footprint.
4. Waste Reduction and Minimization:
Steel casting processes prioritize waste reduction and minimization. Advanced sand reclamation systems are employed to recycle and reuse casting sand, reducing the generation of waste. Additionally, the use of precise molds and optimized gating systems minimizes defects and scrap, leading to less material waste and better overall production efficiency.
5. Emissions Control and Environmental Compliance:
Steel casting foundries adhere to stringent environmental regulations and emission control standards. Advanced emission control systems, including dust collection units and filtration systems, are employed to capture and reduce emissions of particulate matter and harmful gases. This ensures compliance with environmental regulations and protects the air quality in surrounding areas.
6. Green Sand Casting:
Green sand casting, a popular method in steel casting, uses naturally bonded sand molds that are environmentally friendly. The sand can be easily reclaimed and reused, reducing the need for new sand and minimizing waste generation. The use of green sand molds also eliminates the need for chemical binders, further reducing environmental impact.
7. Life Cycle Assessment (LCA):
Life cycle assessment is increasingly being employed in steel casting to evaluate the environmental impact of the entire casting process, from raw material extraction to end-of-life recycling. By identifying environmental hotspots and implementing improvements at each stage, steel casting manufacturers can optimize their processes for reduced environmental impact.
8. Sustainable Design and Optimization:
Steel casting allows for the production of complex and lightweight components, which can contribute to energy efficiency and fuel savings in end-use applications. Through sustainable design practices, such as lightweighting and optimization of component performance, steel casting manufacturers can support greener and more fuel-efficient products.
By adopting sustainable practices and continuously improving processes, the steel casting industry contributes to a greener future. The efficient use of materials, energy optimization, waste reduction, recycling, and adherence to environmental regulations all contribute to the sustainability of steel casting as a manufacturing process.