The technological principle of pouring system for cylinder body iron castings is: conveying liquid metal to the inside of the mold steadily and timely; reducing the adverse effects of turbulence, air suction and oxidation of each component in the gating system to the greatest extent; with the functions of skimming slag and exhaust gas, the pouring and filling can be completed within the specified time. At the same time, the gating system should be able to cooperate with the feeding system to control the overall temperature gradient distribution of iron castings, and meet the requirements of simple operation, material saving and easy cleaning.
The classical casting theory is based on torielli’s small hole outflow theory and ozan formula. The core content is that the gate of the gating system flows out of the nozzle after the gating system is full, and the outflow head of the runner is the vertical distance from the liquid level in the gate cup to the center of the ingate. However, in the casting engineering of cylinder block, the actual cross-sectional area of each component in the gating system is similar, so the theory does not consider the control effect of gate ratio, an important parameter, on the flow of molten metal in the gating system. According to this characteristic, the theory of large hole outflow is defined as the area ratio of sprue to ingate less than 5, and the influence of area ratio of each component on filling dynamic parameters is evaluated.
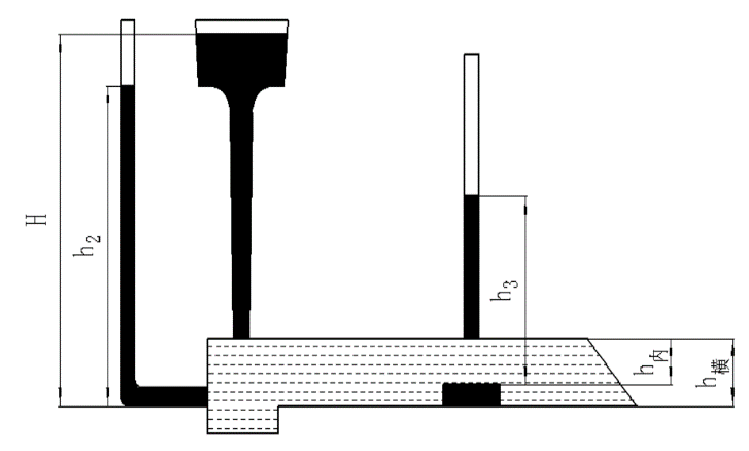
According to the theory of large orifice outflow, the outlet pressure head of ingate is less than the difference between the liquid level of gate cup and the liquid level of ingate, and the outflow velocity of ingate is related to the outlet head and the area ratio of sprue to ingate. The theoretical schematic diagram of large orifice outflow is shown in Fig. 1.
The effective section area ratio of sprue and runner is
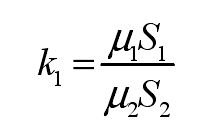
Where
μ 1, μ 2 — discharge coefficient of sprue and runner, μ 1 = 0.5 ~ 0.65, μ 2 = 0.5 ~ 0.65
K1 — effective section area ratio of sprue and runner
S1, S2 — effective section area of sprue and runner
The effective section area ratio of sprue and ingate is
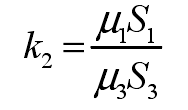
Where
μ 3 — discharge coefficient of ingate
K2 — effective section area ratio of sprue and ingate
S3 — effective section area of ingate
Actual head of ingate
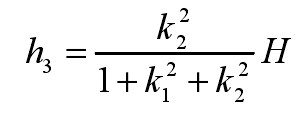
Average head
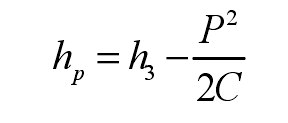
Where P and C are the cavity height above the runner and the total height of the casting cavity.