According to the relation diagram, for gray cast iron during cooling and solidification, at a certain temperature, the content of [%ti] When [%n] is above the stability curve of this temperature, tin will undergo crystallization or crystallization reaction. The Ti content of experimental cast iron is 0.045% (mass fraction, the same below). In combination with actual production, the solubility range of N in molten iron is generally 0 004-0.007%, for the content of N element, the average value is taken as 0.0055% in this paper, which is calculated in combination with the formula. When the temperature drops to 1368 ° C, tin crystals begin to appear in the molten iron. When the temperature continues to decrease, the undercooling of the melt further increases. From the thermodynamic point of view, the driving force for tin crystallization continues to increase, so more tin will be crystallized in the melt. Due to the increase of supercooling, the contents of [Ti] and [n] in the solution components are supersaturated.
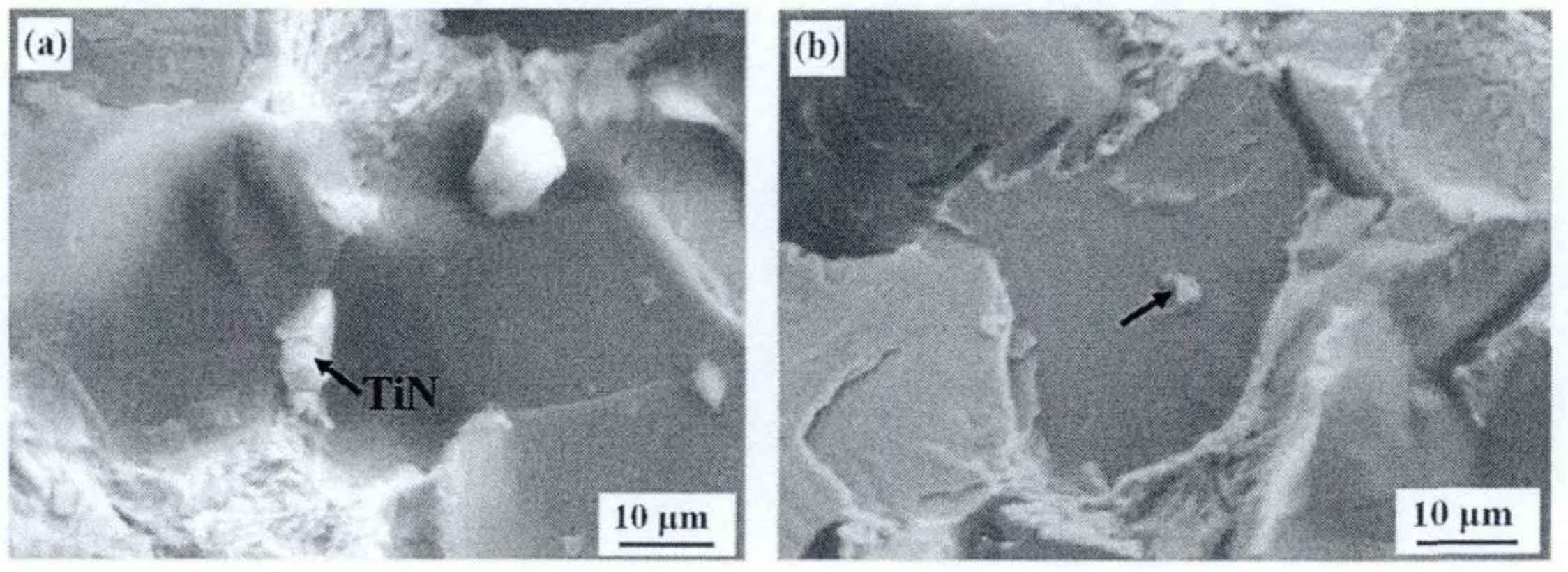
When the temperature is further cooled to the solidus temperature and the melt is completely transformed into austenite, then tin begins to precipitate from the undercooled austenite. It can be seen from the sectional view in figure (a) that tin particles are located at the austenite grain boundary and their size is slightly larger. It can be seen from the analysis that this kind of tin should be crystallized from the melt. When the casting breaks, the interface between tin phase and matrix is easy to be separated and become the crack source, which will seriously reduce the fracture strength of the cast iron. Tin in figure (b) is mainly produced by crystallization in supercooled austenite, because there is a subordinate orientation relationship between ferrite in pearlite and tin: (111) tin// (110) α . Therefore, this kind of tin is mainly attached to one side of the ferrite sheet for growth, and its bonding ability with the matrix structure is strong. As the nucleation and growth of such tin grains are carried out in supercooled austenite, the diffusion of elements will be greatly limited in the solid phase. Therefore, the size of tin grains in the crystallization process is smaller than that in the crystallization process (about 1-2 μ m) During the fracture process, this kind of tin with strong binding force will produce greater resistance to the grain growth, which will further strengthen the matrix of gray cast iron. Combined with the casting properties, the distribution and influence of the two types of tin particles can also be well corresponded.