High quality and high strength gray cast iron should have fine and uniform A-type graphite and fine flake pearlite matrix structure. This kind of structure usually needs to appear in relatively low carbon equivalent cast iron, but this kind of cast iron liquid iron
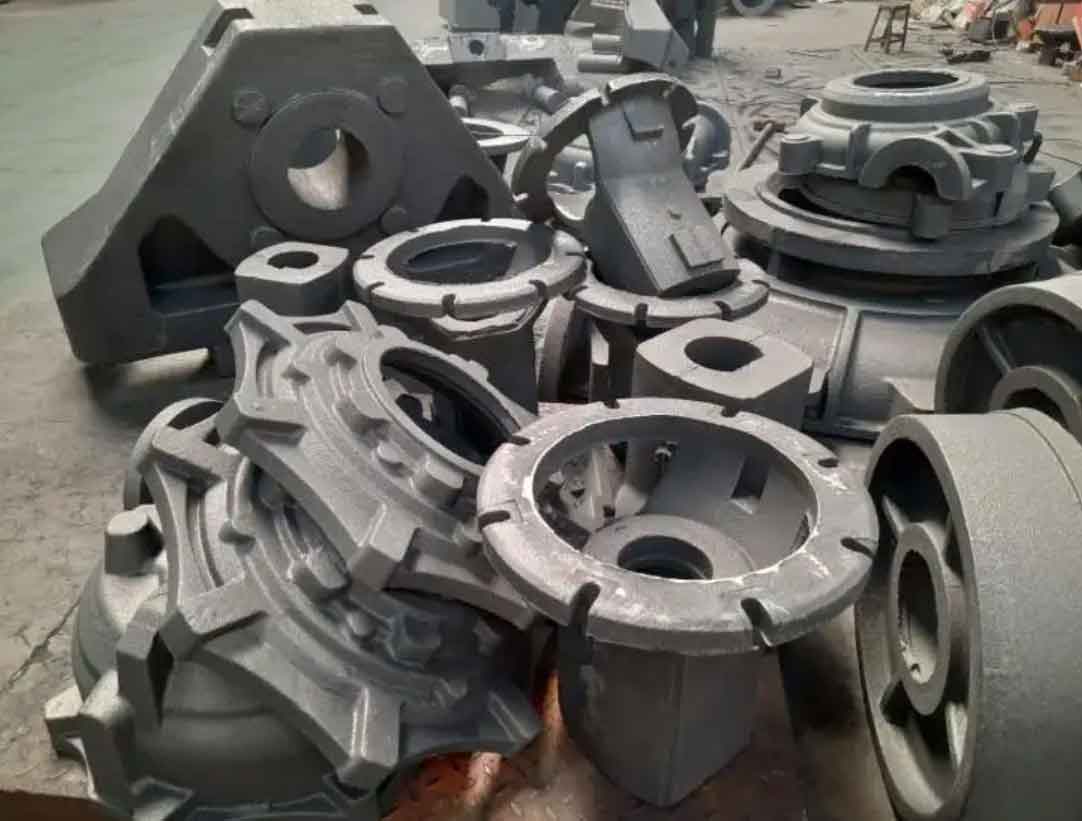
General eutectic undercooling is large, and it is easy to produce white mouth. For such cases, inoculation treatment is needed to obtain refined graphite and matrix structure, while avoiding white mouth. The main functions of inoculants are as follows:
- promote graphitization, effectively reduce the white tendency of molten iron, and weaken or eliminate the white at the thin wall.
- refine the fine crystal structure, refine the graphite, weaken the generation tendency of supercooled graphite and paragenetic ferrite, and can well obtain medium or fine A-type graphite.
- promote and refine the formation of pearlite and improve the matrix structure.
- improve the section sensitivity of castings.
- improve the mechanical properties and processability of cast iron.
Inoculants can be divided into graphitization and stabilization inoculants. Graphitizing inoculants mainly improve the ability of C to convert to graphite, reduce the tendency of whitening, and increase the number of eutectic groups. Stabilizing inoculant can increase and refine pearlite, improve strength and slow down incubation decay time. The figure shows the effect of two inoculants on the strength of cast iron with different carbon equivalent. In the production of high-strength gray cast iron, graphitizing stabilizing inoculants (composite inoculants) need to be used. The reasonable combination of the two can not only obviously improve and refine the microstructure of cast iron, but also have a good effect in prolonging inoculation time and improving uniformity.