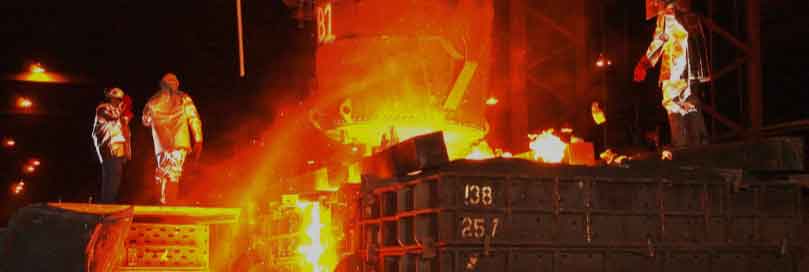
The sand casting industry is vast and comprises numerous manufacturers worldwide. While it is challenging to provide an exhaustive list of all sand casting manufacturers, I can offer an overview of some well-known and reputable companies in the industry:
- ZHY Casting:ZHY was founded in 2004, leading by a group of senior engineers with decades of experience and academic achievements in manufacturing industry.
- Waupaca Foundry: Waupaca Foundry is one of the largest iron foundries in the world, specializing in gray iron, ductile iron, and compacted graphite iron castings. They serve a wide range of industries, including automotive, agriculture, construction, and more.
- Alcast Technologies: Alcast Technologies is a leading aluminum sand casting foundry known for producing high-quality aluminum castings for various applications, including automotive, aerospace, and marine.
- Bodine Aluminum: Bodine Aluminum is a prominent aluminum sand casting company, providing custom castings for industries such as automotive, appliance, and industrial equipment.
- Carteret Die Casting Corporation: Carteret Die Casting is a family-owned company specializing in aluminum and zinc die casting, as well as sand casting, serving industries like electronics, lighting, and automotive.
- Casting Solutions: Casting Solutions is a full-service sand casting foundry that produces parts for industries ranging from automotive and agriculture to energy and construction.
- The C.A. Lawton Co.: Lawton specializes in large iron castings and offers a range of casting services, including green sand, air set, and shell mold casting.
- Bremen Castings: Bremen Castings is a foundry that primarily focuses on producing complex gray and ductile iron castings for diverse industries.
- Victaulic: Victaulic is a global manufacturer of mechanical pipe joining systems, and their sand casting capabilities allow them to produce components for their products.
- Fonderie Saguenay: Fonderie Saguenay is a Canadian foundry specializing in sand and permanent mold casting, producing parts for industries like mining, forestry, and energy.
- Badger Alloys: Badger Alloys is an aluminum and bronze sand casting foundry that serves various industries, including agriculture, construction, and marine.
It’s important to note that the list above represents just a few examples of sand casting manufacturers, and there are many other reputable companies worldwide. When choosing a sand casting manufacturer, consider factors such as their expertise, certifications, quality assurance processes, capabilities, and their ability to meet your specific requirements and production volumes. It’s also advisable to conduct further research and seek recommendations to find the best fit for your casting needs.
Chapter 1: Application of Coated Sand Casting Technology in Sand Casting Manufacturers
The coated sand casting technology is a highly anticipated national promotion technology project, and its application in sand casting manufacturers has gradually attracted widespread attention. This technology is highly favored for its significant advantages in energy conservation, material conservation, reduced production costs, and improved product quality. Especially in the field of casting production in industries such as automobiles, motorcycles, and construction machinery, coated sand casting technology has become a common production process. Sand casting manufacturers hope to apply this advanced technology to a wider range of export casting products through research and practice on the coating sand casting process of export front suspension connecting frame castings, in order to enhance the competitiveness of enterprises.
In the technical requirements and indicators of castings, sand casting manufacturers not only need to consider the surface quality and dimensional accuracy of the product, but also need to pay attention to the requirements of materials and other aspects. For example, as a safety connector on heavy-duty vehicles, the casting of the export front suspension connection frame is made of QT450-10 material and requires a surface roughness of 6.3 to 12.5 μ The dimensional accuracy error between m is only 0.50mm. In addition, there should be no defects such as porosity, sand inclusion, or shrinkage inside the castings, which puts higher requirements on the technical level of sand casting manufacturers.
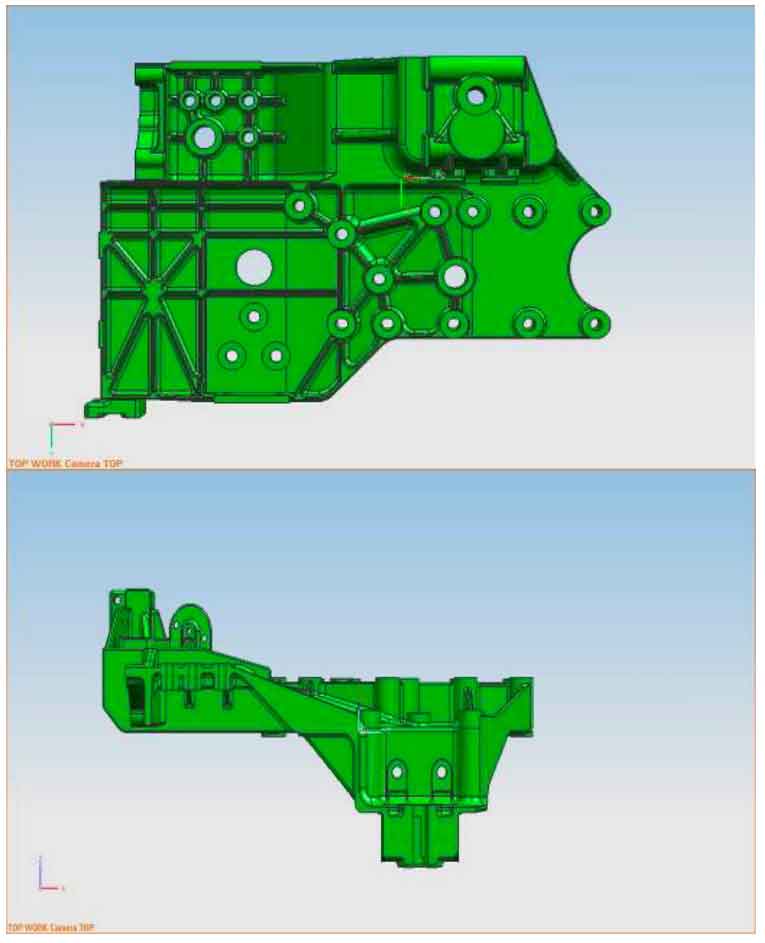
The coated sand casting process is a technique of covering a certain thickness of coated sand layer on the inner cavity of a metal mold to form a casting shell. Sand casting manufacturers continuously optimize their process plans through repeated process experiments and production validation to ensure that castings can achieve ideal conditions during the filling, solidification, and cooling processes. At the same time, the coated sand casting process can eliminate the factors that cause casting defects in castings, and improve the surface and internal quality of castings. Sand casting manufacturers choose coated sand as the sand for casting, which not only ensures the dimensional accuracy and surface roughness of castings, but also improves the strength of the mold, thereby further improving the quality of products.
In the design of coated sand casting process, sand casting manufacturers need to pay special attention to the solidification mode of the castings. For example, the wall thickness of the front suspension connection frame casting at the outlet is uneven, so it is particularly necessary to consider the balanced solidification of the casting in the process design. For this reason, sand casting manufacturers have designed a one-to-one process plan, using horizontal parting and horizontal pouring methods, and placing important surfaces of the castings in the lower mold to ensure the dimensional accuracy of the castings. In addition, in order to meet the liquid filling and contraction needs of castings, sand casting manufacturers have designed a reasonable pouring system and adopted non riser casting technology.
In the process of coated sand casting, fixture design plays a crucial role. Sand casting manufacturers need to design tooling such as metal molds, molding plates, and sandblasting devices to ensure the quality and dimensional accuracy of castings. For example, due to the large size of the casting for the export front suspension connection frame, special consideration needs to be given to the heating capacity in the design of the metal mold to ensure the instant solidification of the coated sand. In addition, in order to improve the appearance quality of castings, sand casting manufacturers have chosen finer grained coated sand and adopted appropriate melting equipment and casting materials.
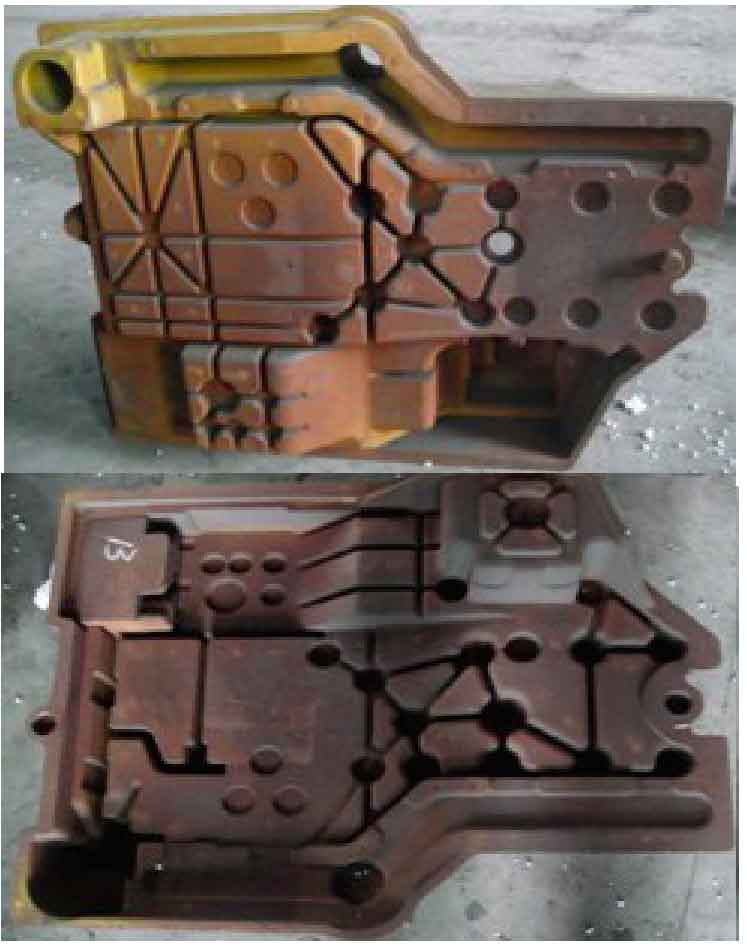
Production trial production is an important part of the coated sand casting process. Sand casting manufacturers produce thin-walled, high-precision, and high-quality export castings by selecting appropriate core shooters and coated sand shells, as well as controlling appropriate pig iron and spheroidizing agents. In the production process, sand casting manufacturers not only need to pay attention to the chemical composition and solidification process of castings, but also need to pay attention to the appearance and internal quality of castings to ensure that products meet export requirements.
By using coated sand casting technology, sand casting manufacturers can produce higher quality casting products and enhance their competitiveness. The coated sand casting technology can not only improve the surface quality and dimensional accuracy of products, but also reduce production costs and improve economic benefits. Therefore, it is necessary for sand casting manufacturers to continuously improve their processes and technological levels to meet market demands and gain more competitive advantages.
The application of coated sand casting technology is of great significance in the production practice of sand casting manufacturers. Through the production practice of export front suspension connecting frame castings, sand casting manufacturers can not only improve the internal and external quality of products, but also reduce production costs and enhance the market competitiveness of enterprises.
Sand casting manufacturers need to fully consider the characteristics and production process of castings when using coated sand casting technology. For example, in the process design of coated sand casting, sand mold manufacturers need to design the gating and exhaust systems reasonably based on the shape, wall thickness, and other characteristics of the castings to ensure that the castings can achieve ideal conditions during the filling and solidification process. Meanwhile, in tooling design, sand casting manufacturers need to select suitable metal molds and plates to ensure the dimensional accuracy and surface quality of castings.
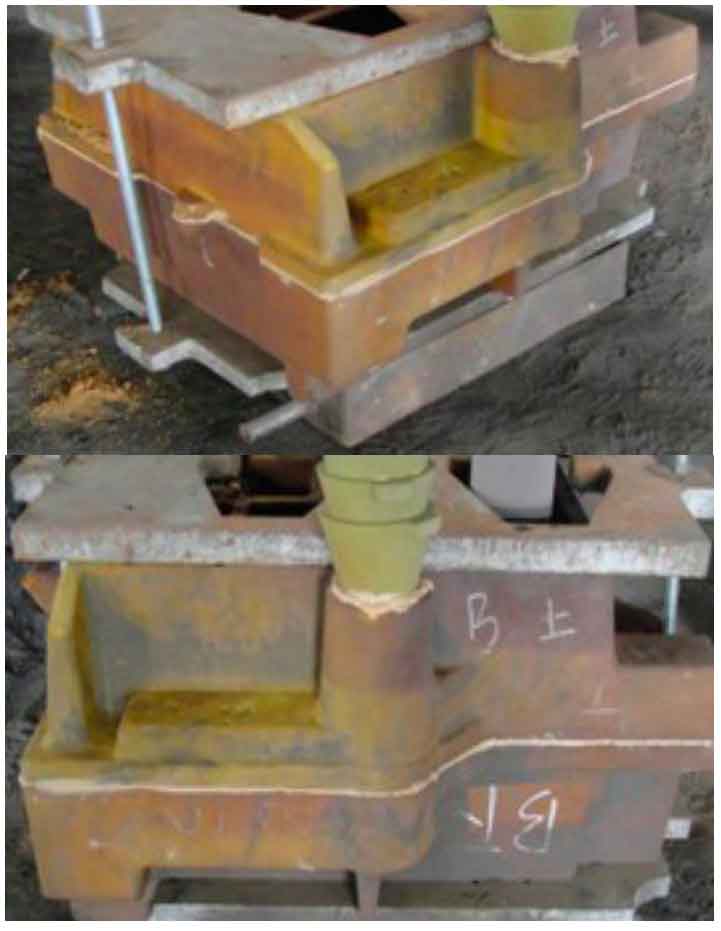
During the trial production stage, sand casting manufacturers need to select suitable pig iron and spheroidizing agents, and control the temperature of the melting equipment to ensure the chemical composition and solidification process of the castings. In addition, sand casting manufacturers also need to pay attention to the details of the production process, such as selecting appropriate coated sand particles and controlling the casting temperature to ensure the surface quality and dimensional accuracy of the castings.
By applying coated sand casting technology, sand casting manufacturers can not only produce high-quality casting products, but also improve production efficiency and reduce production costs. Therefore, promoting coated sand casting technology among sand casting manufacturers is of great significance, which can promote the development of the casting industry and enhance the competitiveness of enterprises.
Overall, the application of coated sand casting technology in sand mold casting manufacturers has broad development prospects. Sand casting manufacturers should continuously improve their processes and technological levels to adapt to changes in market demand and make greater contributions to the development of the casting industry.
Chapter 2: Sand sticking on the appearance of green sand castings
In the process of green sand casting, the appearance of castings with sand sticking may be caused by various factors. To improve this issue, sand casting manufacturers need to take a series of measures and continuously optimize their processes. In improving the process of green sand casting, sand casting manufacturers need to constantly explore innovation, optimize production processes, and improve product quality and production efficiency. The following is a detailed discussion on improvement measures:
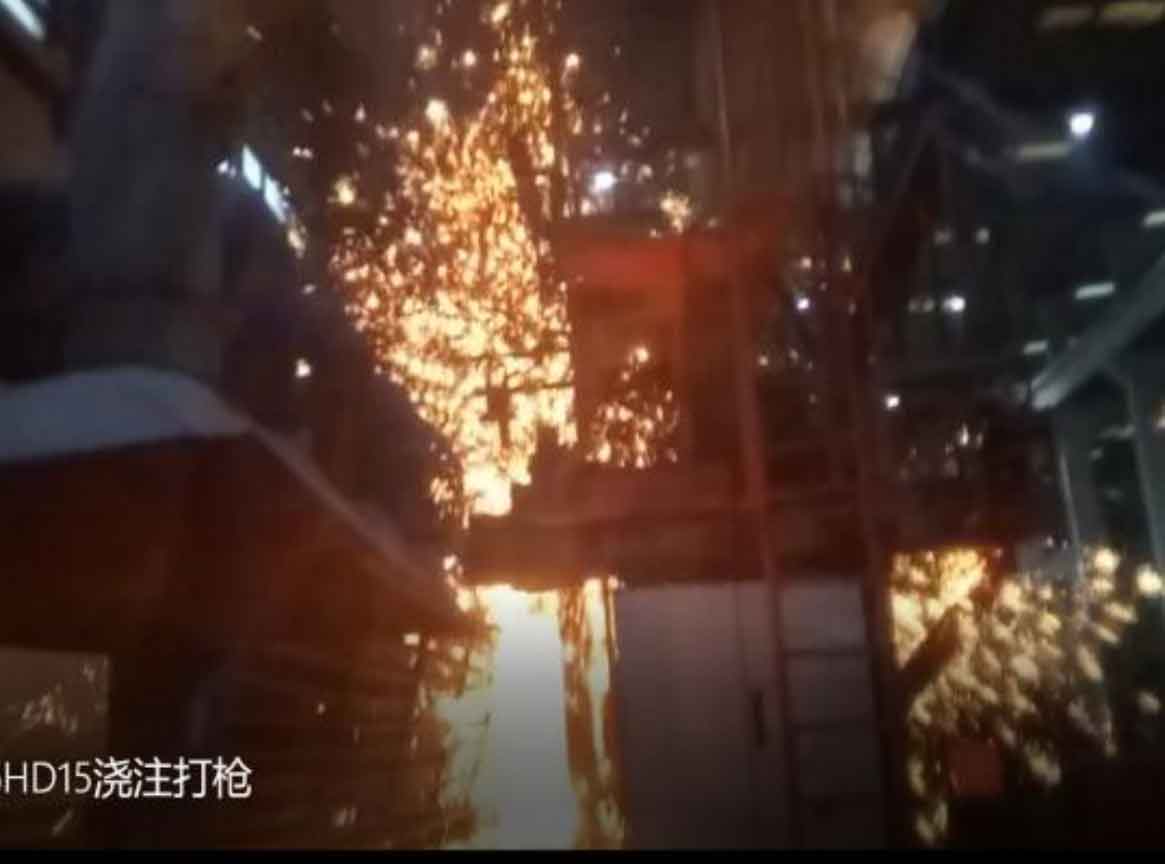
1. Analyze the background and process characteristics
Wet sand casting is a commonly used casting process, characterized by flexible molding methods, good strength performance, and low cost. However, as the production cycle increases and equipment ages, the problem of sand sticking gradually becomes apparent. For the cast iron cylinder blocks produced by ZHY Casting, the phenomenon of sand sticking has become quite obvious, especially in some complex shaped products.
2. Analysis of the causes of sand sticking formation
The problem of sand sticking is mainly caused by two aspects: high gas generation of molding sand and poor exhaust of casting mold. The high moisture content and gas generation in the molding sand cause a sudden increase in air pressure during the casting process, resulting in choking or explosion phenomena. At the same time, the internal exhaust of the mold cavity is not smooth, making it difficult for the gas to be discharged smoothly, leading to the phenomenon of sand sticking.
3. Improvement measures and experimental results
To reduce the problem of sand sticking, it is first necessary to reduce the gas generation of molding sand. To address this issue, adjustments can be made to the raw material ratio and processing technology. For example, reducing the amount of ash powder and bentonite added, reducing the amount of coal powder used, and increasing the number of exhaust holes in the mold cavity.
4. Product improvement effect
Through the implementation of the above improvement measures, ZHY Casting has achieved significant improvement results. After reducing the gas generation of the mold and improving the exhaust system, the problem of sand sticking on the appearance of the casting has been effectively solved, and the product quality has been significantly improved.
conclusion
When dealing with the problem of sand sticking, sand casting manufacturers need to start from two aspects: reducing the gas generation of sand and improving the exhaust system, continuously optimizing the process and adjusting the raw material ratio. Through continuous improvement measures, product quality can be effectively improved, waste rate can be reduced, and better economic benefits can be achieved.
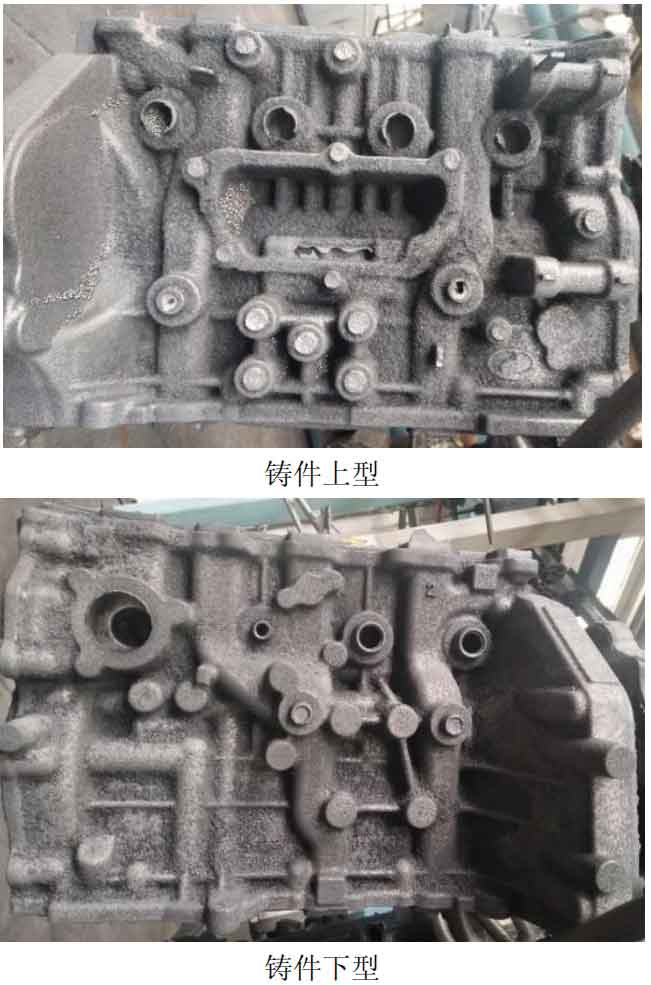
Sand casting manufacturers need to comprehensively consider multiple factors and take targeted measures when dealing with sand sticking problems. Only by continuously improving and optimizing processes can we effectively improve product quality, meet market demand, and achieve long-term development.
Sand casting manufacturers can further improve production quality and efficiency, reduce the incidence of sand sticking defects, provide customers with higher quality products and services, and achieve sustainable development of the enterprise.
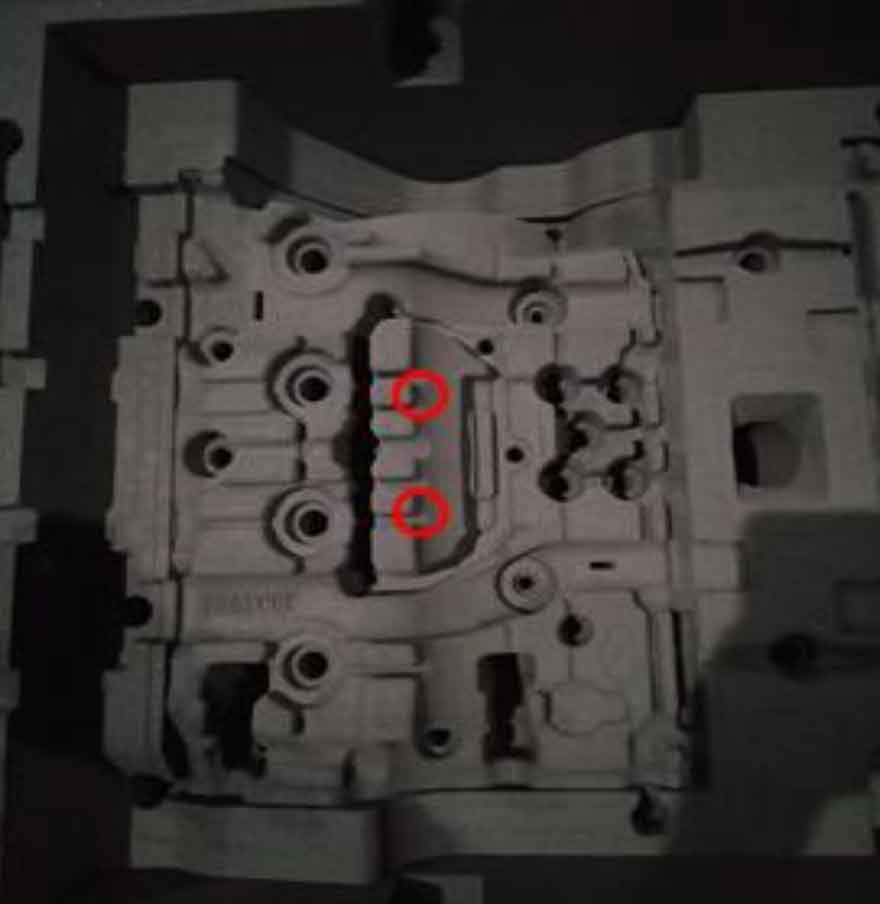
Through the implementation of the above comprehensive measures, sand casting manufacturers can comprehensively enhance their technological strength and competitive advantages, continuously meet customer needs, and achieve sustainable development and win-win situations. In the context of increasingly fierce industry competition, sand casting manufacturers should maintain an open mindset, constantly innovate and progress, keep up with the times, in order to stand invincible in the market and win broader development space.
Chapter 3: Optimization and improvement of furan resin sand casting technology: key exploration of sand casting manufacturers
In today’s modern casting technology, sand casting manufacturers are constantly exploring the optimization and improvement of technology while pursuing high-quality castings. The furan resin sand casting technology, as an important casting process, plays a crucial role in meeting the application needs of various fields. However, the defects in furan resin sand castings directly affect the quality of the castings, so the optimization and improvement of furan resin sand casting technology is particularly urgent. This article will focus on exploring how to improve the quality of furan resin sand castings through scientific control measures to meet the demand of sand casting manufacturers for high-quality castings.
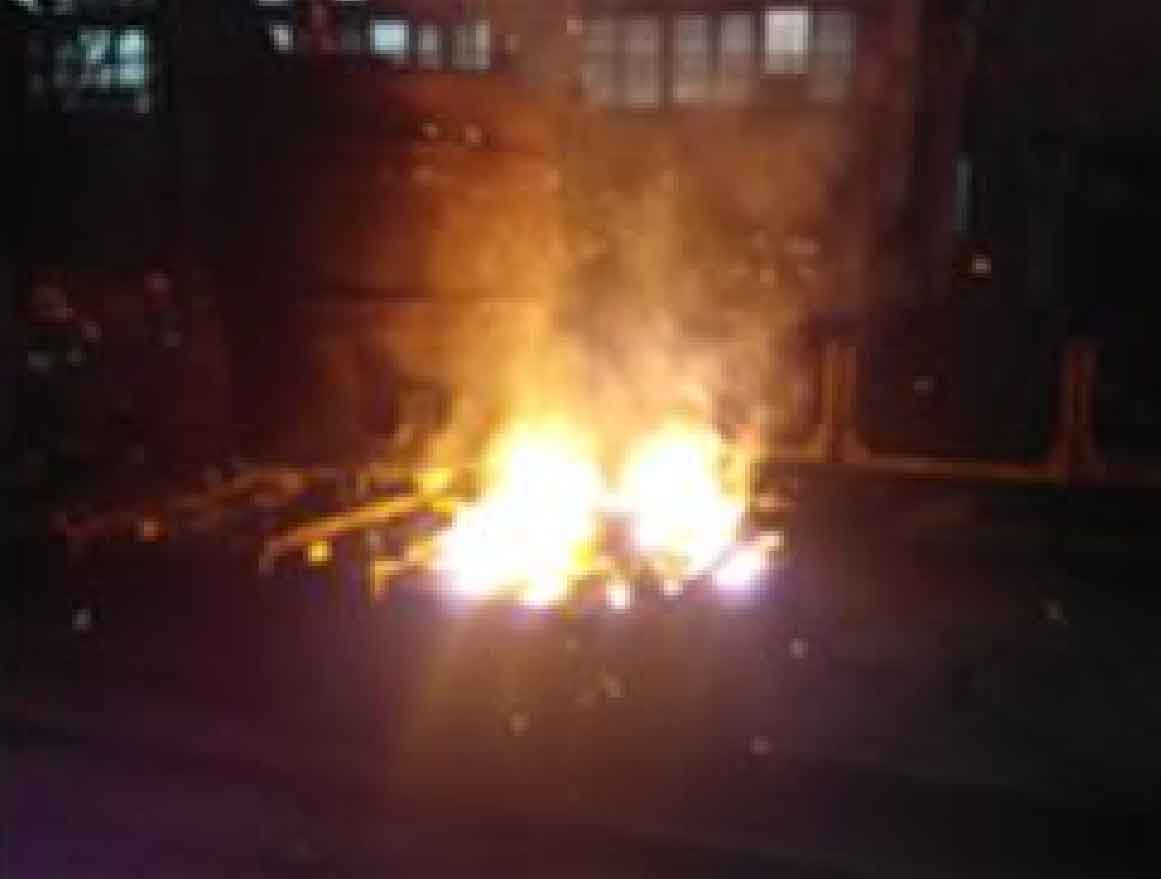
1. Strength control and optimization:
Strength control is crucial in the manufacturing process of furan resin sand castings. Research has found that the amount of resin added and the particle size of silica sand directly affect the strength of resin sand. Therefore, for sand casting manufacturers, scientific control of resin addition and reasonable selection of silicon sand particle size are key.
Scientific control of resin addition: Sand casting manufacturers need to control the resin addition within the range of 0.8%~1.5% and adjust it according to the performance requirements of the castings. Excessive or insufficient resin addition can lead to quality issues in castings, so controlling within an appropriate range can ensure casting quality and reduce costs.
Reasonable selection of silicon sand particle size: Sand casting manufacturers should choose the appropriate silicon sand particle size, and generally choose a 40/70 mesh silicon sand with 3 sieves for the best effect, which can improve the strength performance of furan resin sand castings and reduce costs.
2. Scientific control of process parameters:
For the process technology of furan resin sand castings, scientific control of process parameters is directly related to the quality of the castings. Sand casting manufacturers need to focus on controlling the curing strength and curing time to improve the technological effectiveness of the process.
Curing strength control: For furan resin sand castings, reasonable control of curing strength can solve the problem of porosity. Sand casting manufacturers should control the curing strength within an appropriate range to avoid quality problems caused by excessive or insufficient curing strength.
Curing time control: Sand casting manufacturers need to scientifically control the curing time to improve production efficiency while ensuring curing strength, in order to ensure the overall quality of furan resin sand castings.
3. Breathability control and optimization:
Breathability is one of the important factors affecting the performance of furan resin sand castings. Sand casting manufacturers need to strengthen scientific control over compactness and improve the technical characteristics of furan resin sand castings to meet the quality requirements of castings.
Scientific control of compactness: By scientifically controlling compactness, the gap between resin sand particles can be reduced, and the strength of castings can be improved. Sand casting manufacturers should adjust control parameters according to the actual situation to achieve the best effect.
Improving operability: Sand casting manufacturers need to pay attention to parameters such as usable time and resin sand molding time, and make reasonable adjustments to improve operational efficiency and production efficiency.
4. Conclusion:
In the constantly developing casting process technology, the optimization and improvement of furan resin sand casting technology is an important issue that sand casting manufacturers must face. By scientifically controlling strength, process parameters, and permeability, sand casting manufacturers can effectively improve the quality of furan resin sand castings, meet market demand, and gain greater competitive advantages.
Through in-depth exploration of furan resin sand casting technology, this article aims to provide effective technical guidance and improvement plans for sand casting manufacturers, and promote continuous innovation and improvement of casting process technology. I believe that in the near future, furan resin sand casting technology will usher in new development opportunities, bringing more business opportunities and development space for sand casting manufacturers.
Chapter 4: Gas explosion and sand sticking defects in clay sand castings and their solutions
The 7274 flywheel housing is a clay sand casting of a Weichai engine successfully developed by ZHY Casting in 2022. It is made of HT250 material and has a gross weight of 20.5 kilograms, as shown in Figures 1 and 2.
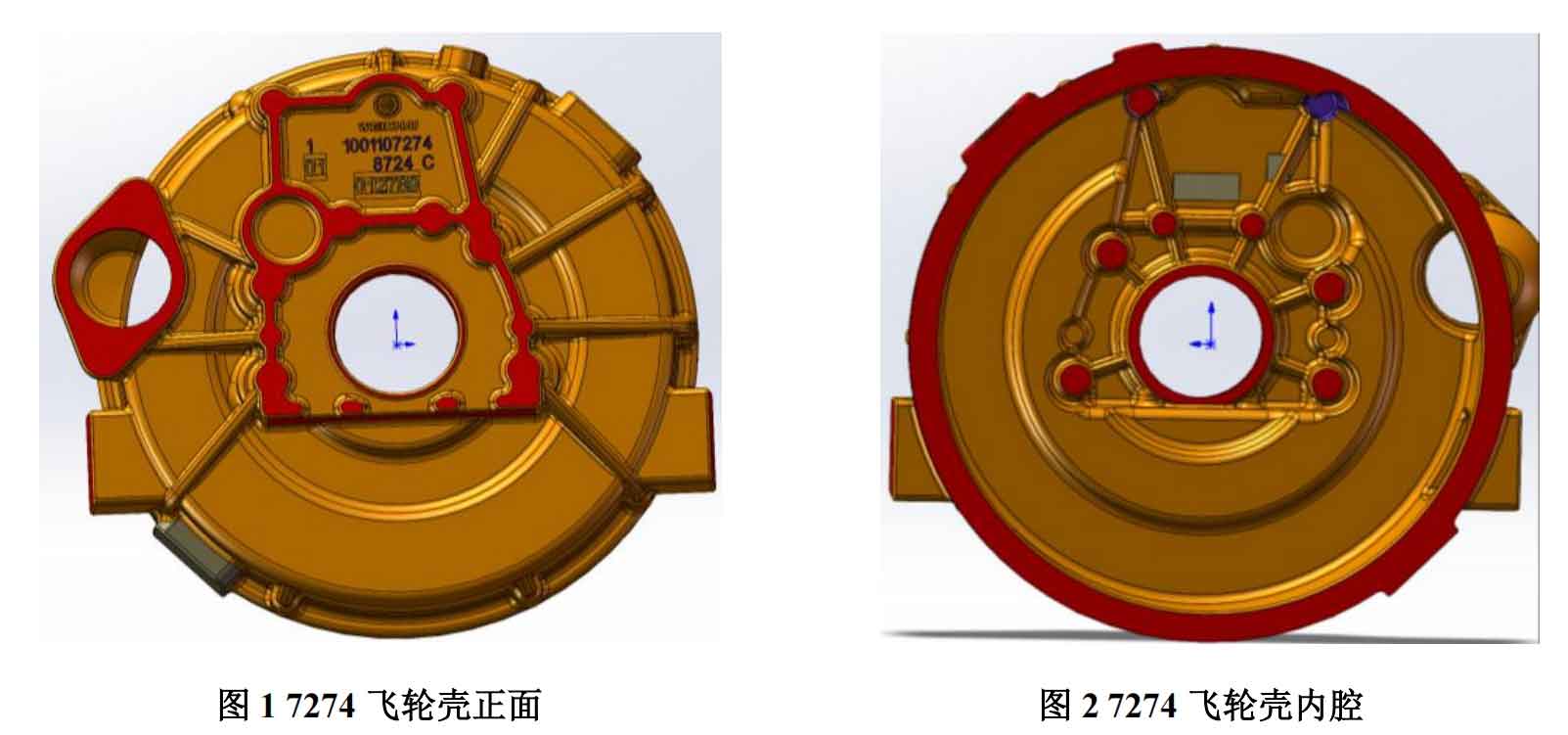
As a leading sand casting manufacturer, we adopt the clay sand static pressure molding and film coated sand hot core production process (see Figure 3, Figure 4, Figure 5) to ensure the quality and durability of castings.
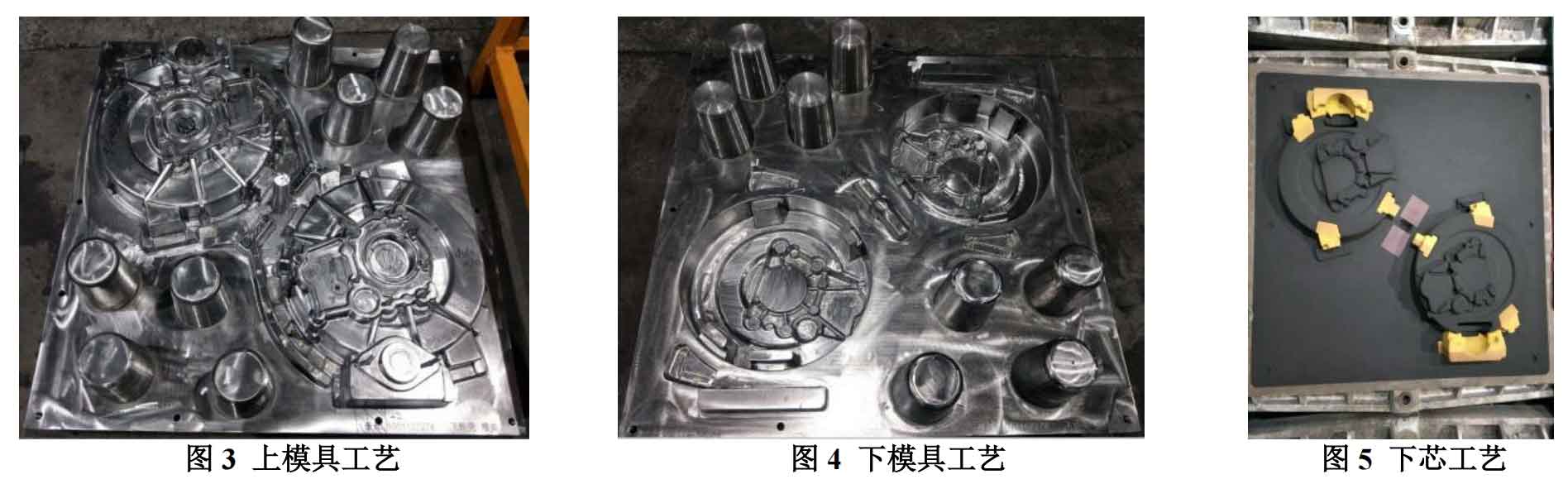
However, in the mass production process of clay sand castings, local surface sand sticking defects often occur (see Figures 6 and 7), and even serious gas explosion sand sticking problems (see Figure 8).
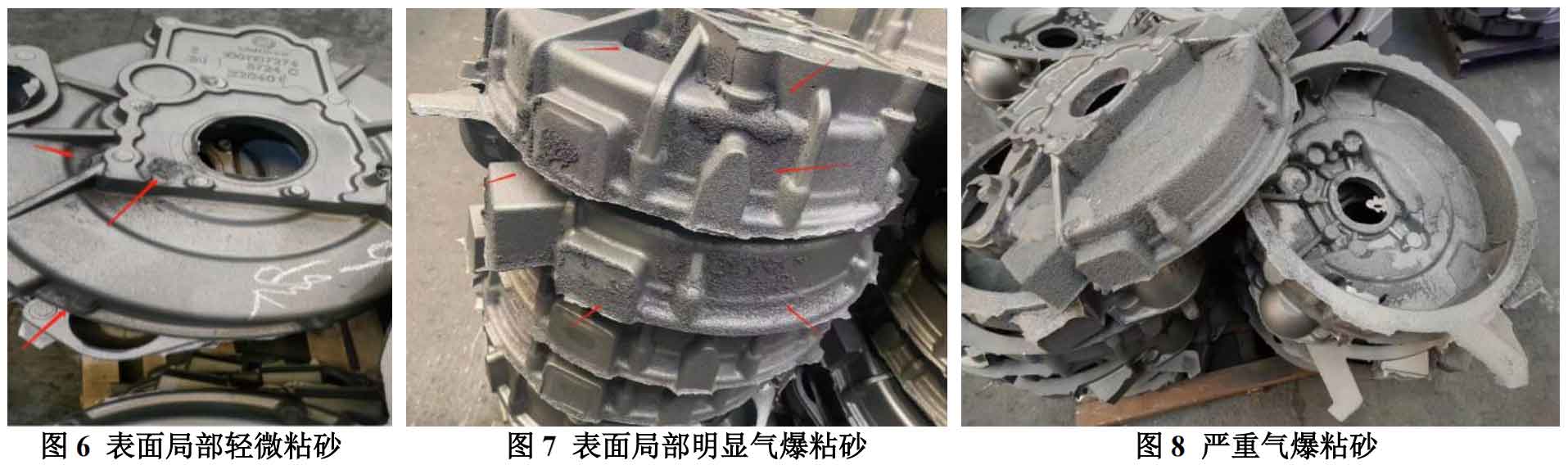
In response to these challenges, sand casting manufacturers have taken a series of targeted measures to address the root causes of these defects and improve the overall quality of castings.
(1) Optimize the design of the pouring system:
In order to reduce the risk of gas explosion and sand sticking, sand casting manufacturers have focused on optimizing the design of the pouring system. By reducing the flow resistance area and extending the pouring time, sand casting manufacturers aim to minimize defects caused by rapid pouring. In addition, increasing the area of the diversion gate and installing additional exhaust holes can help achieve smoother pouring and improve gas discharge capacity, thereby reducing the incidence of sand sticking defects.
(2) Improving the quality of molding sand:
Sand casting manufacturers recognize the crucial role of sand quality in the integrity of castings, and therefore take measures to reduce mud content and combustion reduction, thereby improving sand permeability and reducing the risk of gas related defects. In addition, by adjusting the amount of water and additives such as bentonite and coal powder, sand casting manufacturers have optimized the compaction rate of molding sand, further improving its effectiveness and stability during the casting process.
(3) Process simulation and analysis:
In order to gain a deeper understanding of the root causes of gas explosion and sand sticking defects, sand casting manufacturers used MAGMA simulation analysis. Through a detailed inspection of filling speed, temperature, pressure, and air entrainment dynamics, sand casting manufacturers have identified areas for improvement in the original mold casting process. By addressing issues such as uneven filling speed and poor exhaust at critical points, sand casting manufacturers can develop effective solutions to mitigate the impact of these defects.
(4) Verification and validation:
After implementing process improvements based on simulation analysis results, sand casting manufacturers conducted rigorous validation tests to evaluate their effectiveness. The results showed a significant improvement in surface cleanliness and a reduction in defects. The subsequent mass production verified the sustained effectiveness of the measures taken, paving the way for the smooth production of high-quality clay sand castings.
(5) Applied to similar components:
Drawing on the successful experience of process improvement, sand casting manufacturers have extended similar measures to other components, such as flywheel housings 8428 and 0415. The positive results of these efforts highlight the scalability and applicability of sand casting manufacturer methods.
In short, achieving defect free clay sand castings is a continuous learning and improvement process. By utilizing advanced simulation techniques and combining practical process improvements, sand casting manufacturers have successfully overcome the challenges posed by gas explosion and sand sticking defects. The application of these methods not only ensures the production of high-quality castings, but also demonstrates the commitment of sand casting manufacturers to innovation and excellence in the field of sand casting.
Through cooperation with esteemed partners and relentless pursuit of process optimization, sand casting manufacturers will lead the development of clay sand casting technology. The journey of sand casting manufacturers pursuing perfection is ongoing, guided by principles of quality, innovation, and customer satisfaction.
Chapter 5: Solution to crack defects in thick and large castings of duplex stainless steel
As a sand casting manufacturer, we have conducted in-depth research on crack defects in thick and large castings of duplex stainless steel and proposed effective solutions to ensure the stability and reliability of casting quality.
1. Background introduction
Duplex stainless steel is an important metal material with excellent mechanical properties and corrosion resistance, widely used in engineering fields in harsh environments such as seawater. However, duplex stainless steel is prone to crack defects during the casting process, especially for thick and large castings, where crack problems are particularly prominent.
2. Examples and analysis of crack defects
2.1 Examples of crack defects
The pump body castings produced by sand casting manufacturers have crack defects due to the failure of cooling process control. These crack defects are often discovered in subsequent inspections, which has a serious impact on product quality.
2.2 Analysis of crack defect causes
The generation of crack defects is mainly related to the microstructure changes of duplex stainless steel during the casting process. Within a certain temperature range, duplex stainless steel is prone to precipitation σ As a result, the brittleness of the casting increases, making it prone to cracking. In addition, duplex stainless steel also exhibits a brittle tendency at 475 ℃, further exacerbating the formation of cracks.
3. Solution
3.1 Reduction σ Phase precipitation
In order to solve the problem of crack defects, sand casting manufacturers have proposed reducing σ Solution for phase precipitation. Among them, using forced air cooling after high-temperature boxing is an effective method. This method can quickly reduce the temperature during the casting cooling process, effectively reducing σ The generation of phases reduces the risk of cracking.
3.2 Operational Details
In practical operation, sand casting manufacturers need to pay special attention to the following aspects:
Ensure that the temperature of the casting when entering the water is above 900 ℃ to ensure rapid passage σ The temperature range of phase precipitation;
Control the cooling rate of castings to avoid uneven cooling caused by too fast or too slow;
For heavy castings, a fan with spray can be used for forced cooling to ensure the uniformity of cooling effect.
4. Conclusion
Through the analysis and discussion of crack defects in thick and large castings of duplex stainless steel, we provide a feasible operational guide for sand casting manufacturers. Forced air cooling after high-temperature boxing is a simple and effective method that can effectively reduce the risk of cracks in castings and ensure the stability and reliability of casting quality.
In future production practice, sand casting manufacturers will further optimize operational details, improve process levels, and provide customers with higher quality products and services.
Chapter 6: Sand casting manufacturers improve the quality of duplex stainless steel A995-5A castings
In the field of modern industrial manufacturing, sand casting manufacturers play an irreplaceable role in producing high-quality duplex stainless steel castings. Dual phase stainless steel, due to its unique dual phase structure of austenite and ferrite, exhibits excellent mechanical properties and corrosion resistance, making it the preferred material for many industrial applications. Especially for A995-5A grade duplex stainless steel, it has been widely used in demanding marine and chemical treatment environments due to its high strength, good toughness, and excellent corrosion resistance. However, in the production process of sand casting manufacturers, castings are prone to crack defects during the cooling process, posing a serious threat to the quality and performance of castings.
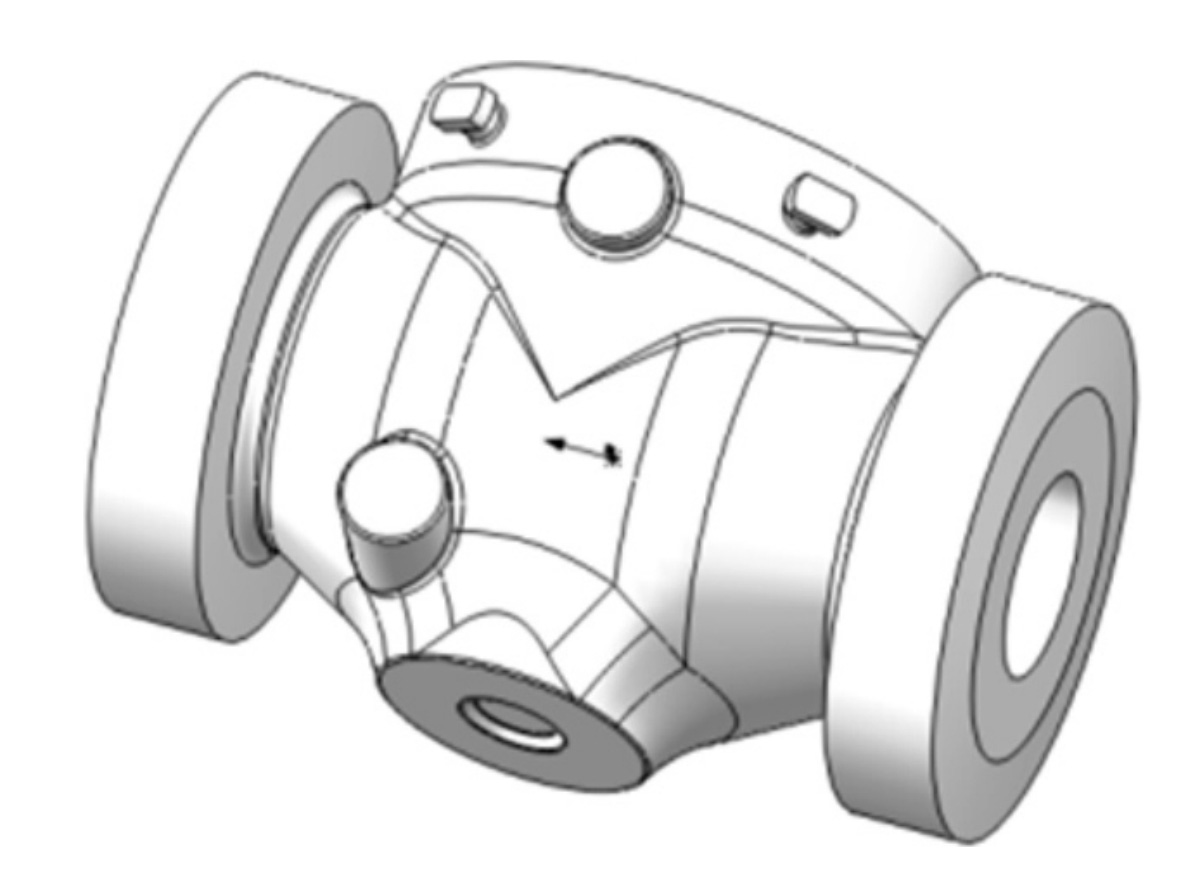
1. The challenges faced by sand casting manufacturers
One of the biggest challenges faced by sand casting manufacturers in producing A995-5A grade duplex stainless steel castings is the generation of cracks. These cracks are usually generated during the cooling process of castings due to improper temperature control, especially at the cooling rate and σ The formation process of phase organization is more pronounced. σ Phase is a hard and brittle intermetallic compound that significantly reduces the plasticity and toughness of castings, leading to the occurrence of cracks. To address this issue, sand casting manufacturers have taken a series of technical measures to ensure that castings can be successfully cooled and cured without cracking.
2. Preventive measures taken by sand casting manufacturers
Sand casting manufacturers have implemented the following key technical measures in the production process to minimize or avoid the occurrence of crack defects:
- Direct water quenching after high-temperature boxing: Sand casting manufacturers perform boxing immediately after the casting has just solidified, and then immediately water quench the casting. This method can quickly pass through the temperature range of 600~1000 ° C, reducing σ The precipitation of phases reduces the risk of crack formation.
- Timely furnace heat treatment: For certain specific castings, sand casting manufacturers will directly send the castings into the heat treatment furnace for appropriate heat treatment after boxing. By precisely controlling the heat treatment temperature and time, it is possible to effectively reduce σ The formation of phases to avoid the occurrence of cracks.
- Heat treatment after cooling to medium temperature: Sand casting manufacturers will also adopt a strategy of heat treatment when the castings are cooled to 100-150 ° C. This strategy aims to reduce internal stress in castings and further reduce the possibility of crack formation through a mild cooling process and subsequent heat treatment.
- Forced air cooling or spray: sand casting manufacturers can control the cooling process more carefully by carrying out forced air cooling or spray treatment on castings after high temperature boxing, so as to slow down the rate of temperature decline of castings and effectively avoid cracks. This method is particularly suitable for thick steel castings, as it allows sand casting manufacturers to more accurately manage the cooling rate of castings, avoiding excessive internal stress caused by rapid cooling.
3. Technical optimization of sand casting manufacturers
In order to further improve the quality of duplex stainless steel castings, sand casting manufacturers continue to optimize their production processes and technologies. Including:
- Fine process control: By using high-precision temperature control equipment and advanced casting simulation software, sand casting manufacturers can achieve more detailed temperature and cooling rate control during the casting process, ensuring that the temperature of the castings decreases uniformly throughout the cooling process, avoiding stress concentration and crack formation caused by large temperature differences.
- Chemical composition optimization: By optimizing the chemical composition of castings, sand casting manufacturers can further reduce σ The probability of phase formation. Properly adjusting the content of chromium, nickel, molybdenum, and nitrogen can not only improve the mechanical properties and corrosion resistance of castings, but also help reduce the risk of cracks.
- Improvement of post-treatment technology: Sand casting manufacturers also attach great importance to the post-treatment process of castings, such as solving the problem of sand cleaning, optimizing cutting and polishing processes, and implementing appropriate heat treatment procedures, all of which are key links to ensure the final quality of castings.
4. conclusion
Sand casting manufacturers play a crucial role in the production process of duplex stainless steel A995-5A castings. By adopting the above measures and technological optimization, not only can crack defects be effectively prevented, but also the mechanical properties and corrosion resistance of castings can be ensured to meet or even exceed the usage requirements. With the continuous progress of manufacturing technology and the continuous optimization of production processes, sand casting manufacturers will be able to produce higher quality and better performance duplex stainless steel castings, meeting the increasingly stringent industrial application requirements. This not only demonstrates the technological innovation capability of the sand casting industry, but also provides a solid foundation for the competitiveness of sand casting manufacturers in the global market.