As a key component of the automotive chassis, squeeze casting steering knuckles bear complex and diverse loads during vehicle operation, thus requiring high strength and impact resistance. At present, most of the steering joint parts produced by squeeze casting are produced by ductile iron sand casting. With the development requirements of automotive lightweighting, the material of squeeze casting steering knuckles has also begun to shift from ductile iron to lightweight materials such as aluminum alloy. NOHARA S et al. aimed to analyze the stiffness, strength, and fatigue life of squeeze cast steering knuckles under different working conditions, and optimized the structure and shape of squeeze cast steering knuckles. After optimization, the weight of the parts was reduced by about 9%; Zhou Si et al. conducted a lightweight design of the aluminum alloy automotive squeeze casting steering joint structure through topology optimization, reducing the mass of the squeeze casting steering joint by 48% while ensuring strength. However, currently, most research has remained focused on conceptual design and simulation analysis, with little consideration given to the impact of subsequent forming processes on the structure of squeeze casting steering knuckles. Therefore, it is difficult to form squeeze casting steering knuckles after structural optimization.
Squeeze casting technology has strong applicability, dense casting structure, excellent mechanical properties, good quality, and high dimensional accuracy. It is suitable for some structural components that require high mechanical properties, such as automotive wheels, steering knuckles, frames, connecting rods, etc. It is an ideal forming process for achieving lightweight automotive components. This study combines topology optimization methods with squeeze casting technology, using aluminum alloy instead of ductile iron to optimize the topology of the existing squeeze casting steering joint structure. Through simulation verification and mechanical performance verification, the development of squeeze casting aluminum alloy automotive steering joints is completed.
1.Topology optimization of aluminum alloy steering knuckles
1.1 Mathematical model for topology optimization under multiple operating conditions
Topology optimization is the process of finding the optimal material distribution path that meets the required performance within a fixed optimization design space, in order to obtain the lightest structural design solution. The commonly used methods currently include homogenization method, variable density method (SIMP method), level set method, asymptotic structural optimization method (ESO), independent continuous mapping method (ICM), etc. Among them, the variable density method is widely used in the engineering field and commercial software due to its few design variables, easy implementation, and high efficiency.
The common models in the variable density method include the solid isotropic material penalty model (SIMP) and the rational approximation model for material properties (RAMP). The model punishes the intermediate density by introducing a penalty factor, causing the values of the intermediate density to cluster towards both ends of 0/1. 0 indicates that there is no material at the spatial point, and 1 indicates that the area is occupied by solid materials. The optimization model of 0/1 discrete variables can effectively obtain the topology optimization model of continuous variables.
Due to the different operating conditions of cars during driving, the load on squeeze cast steering knuckles varies under different operating conditions. When there are multiple operating conditions, the optimal topology optimization solution for each operating condition is also different. Therefore, for the convenience of calculation, it is necessary to choose a common objective function, and for squeeze casting steering joints, the goal is usually to maximize stiffness. At the same time, it is also necessary to know the relative importance of each operating condition. The commonly used methods include compromise planning and Analytic Hierarchy Process in operations research. Based on the actual situation, it is determined that the relative importance of each working condition is the same. The mathematical model for topology optimization of squeeze casting steering knuckles under multiple working conditions is:
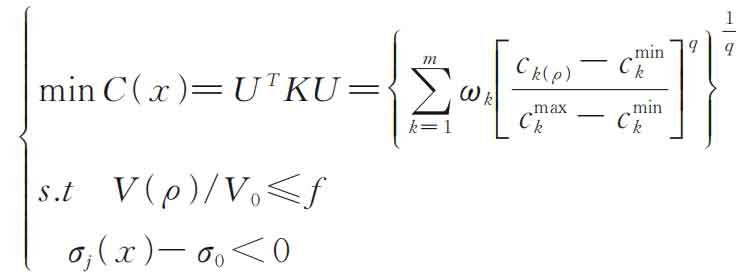
In the formula, K and U represent the element stiffness and displacement matrix, respectively; M is the total number of load conditions, taking m=5; ω K is the weight value of the k-th working condition, and since each selected working condition is equally important, the weight coefficients of each working condition are all 1; Q is the penalty factor, and q ≥ 2, usually q=3; Ck( ρ ) The flexibility objective function for the k-th working condition; Ckmax is the maximum value of flexibility for the k-th working condition, which is the strain energy obtained from the analysis of the original structure before optimization; Ckmin is the minimum value of flexibility for the k-th working condition, which is the strain energy obtained by analyzing the model after filling the material; ρ Design variables, i.e. unit material density; V0 and V( ρ) To optimize the volume of the structure before and after optimization; F is the volume constraint fraction, taking f=30%; σ J (x) is the stress at the j-th node; σ 0 is the stress limit, taken as 230 MPa.
1.2 Establishment of finite element model
Based on the model of ductile iron squeeze casting steering joint, while retaining the original assembly relationship, a maximum solid model of aluminum alloy squeeze casting steering joint is established and imported into hypermesh for mesh division. The mesh size is 1 mm (the minimum model size is 1 mm). Figure 1 shows the topology optimization model of aluminum alloy squeeze casting steering joint after mesh division. The circular part is an undesigned area due to the presence of a mating surface, while the gray area represents the design space, which is the topology optimization area.
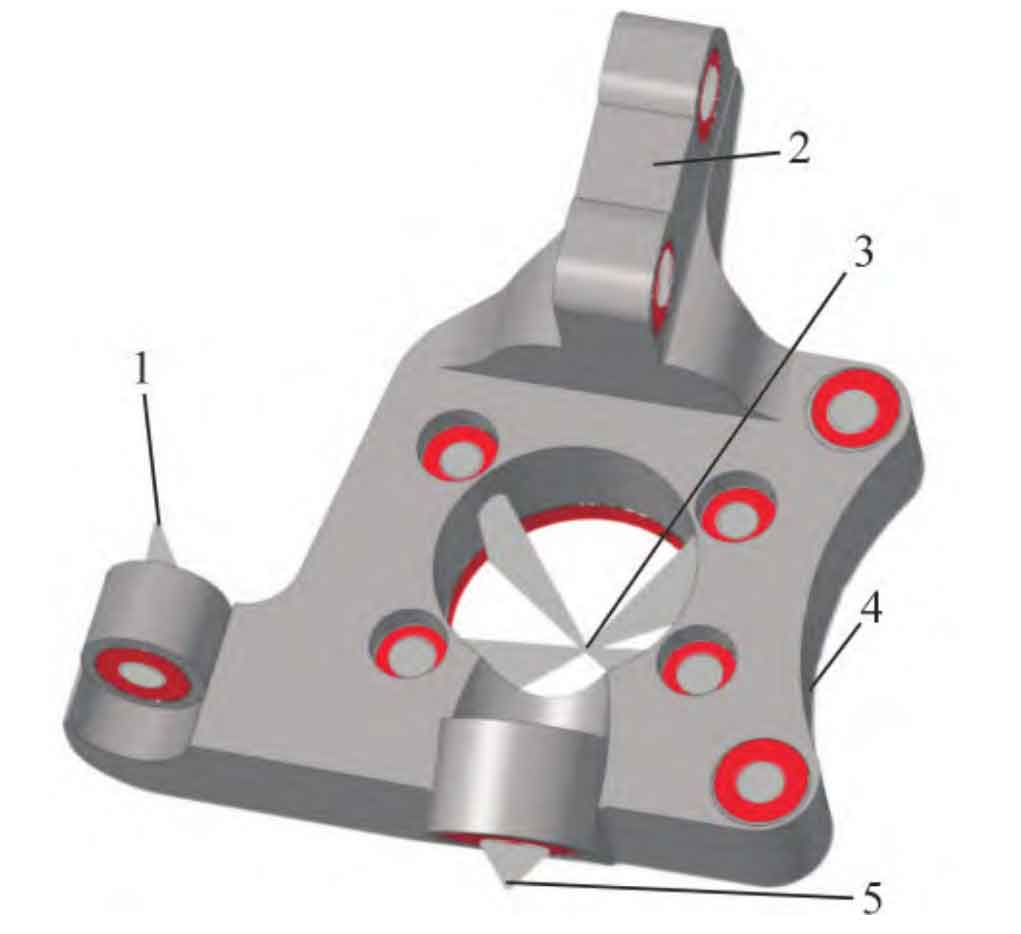
The elastic modulus of the aluminum alloy squeeze cast steering joint is defined as 72.4 GPa, Poisson’s ratio is 0.33, and density is 2700 kg/m3. When a car is driven under different road conditions, the load on the squeeze cast steering knuckles also varies. Based on the actual situation, 5 working conditions were considered, including 4 times full load, unilateral crossing, crossing, forward braking, and forward acceleration. When subjected to different load conditions, the squeeze casting steering joint is not in a completely static state relative to the vehicle body. The inertia release method is adopted, which balances external forces through inertia force and ignores node displacement. The constraint method of automatically selecting virtual constraint points is adopted by software calculation programs.
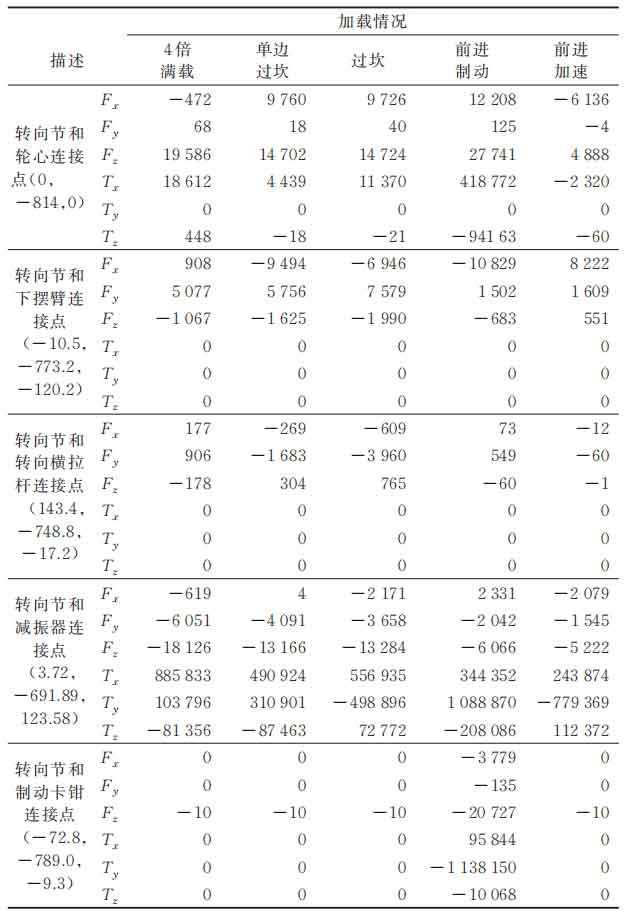
To perform inertia release analysis on the squeeze casting steering joint, it is necessary to directly apply a load at the installation point. The position of the installation point and the applied load are shown in Table 1. Find the position of the connection points between the squeeze cast steering joint and the wheel center, lower swing arm, steering tie rod, shock absorber, and brake caliper in the coordinate system, and then establish an RBE3 flexible unit to connect the surface unit with the above 5 connection points, as shown in Figure 1. Finally, apply the forces (Fx, Fy, Fz) and torques (Tx, Ty, Tz) at the 5 positions provided in Table 1 to each connection point of the squeeze cast steering joint.
1.3 Topology optimization analysis and results
When creating a topology optimization task for squeeze casting steering knuckles, the objective function is the comprehensive flexibility of multiple working conditions, and the optimization constraint is the volume fraction. The upper limit of the volume optimization is set to 30% (i.e. the volume ratio after optimization/before optimization is ≤ 0.3). At the same time, in order to meet the strength requirements of the optimized structure, the stress after optimization is limited to less than 230 MPa. Set the mold lifting method to bidirectional mold lifting, and the direction of mold lifting is shown in Figure 2.
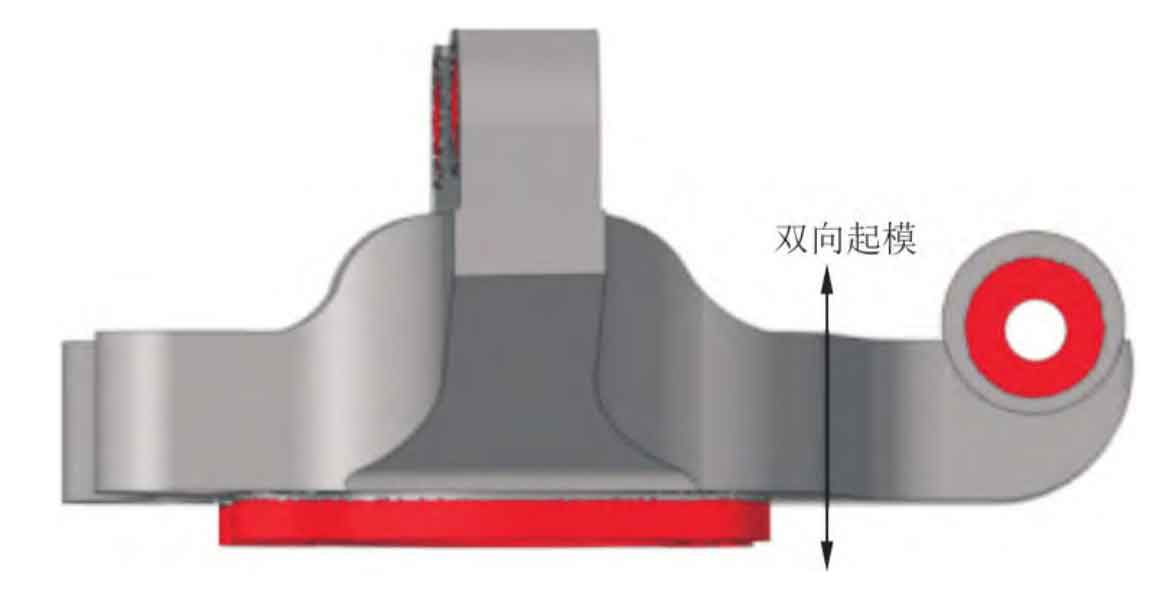
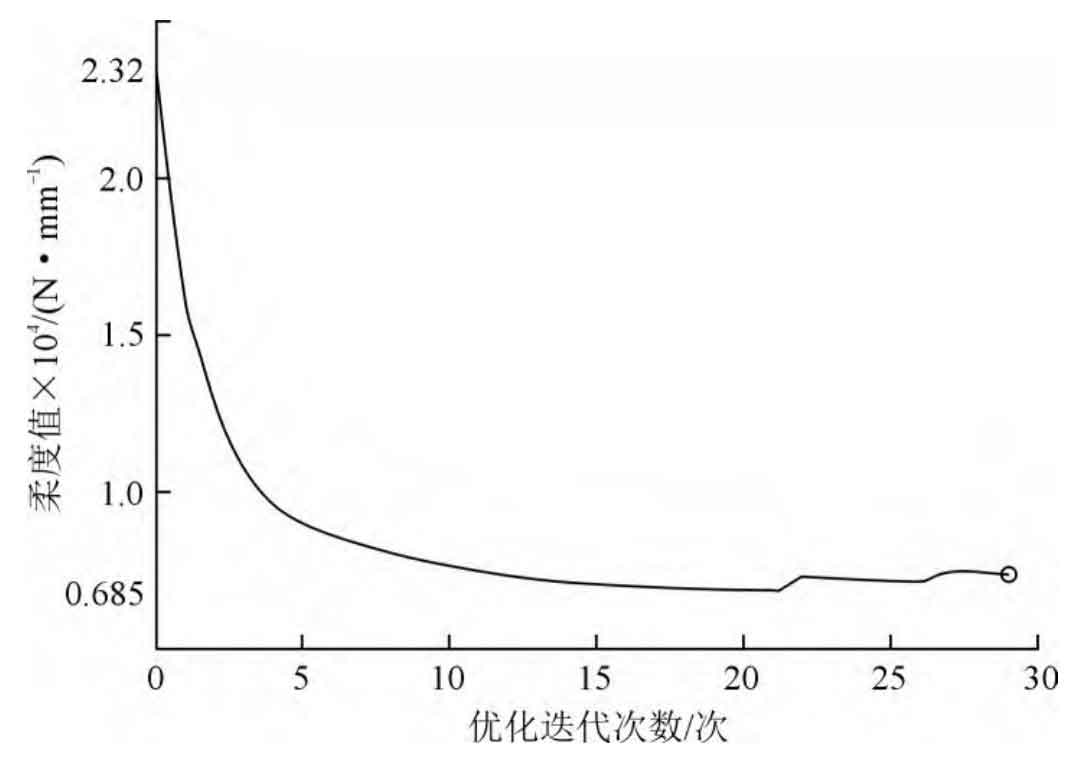
The optimization results show that after 29 iterations, the flexibility gradually converges and eventually stabilizes. The flexibility variation curve is shown in Figure 3. Setting the unit density threshold to 0.3 and retaining units with relative density>0.3, the optimized topology of the squeeze casting steering joint is shown in Figure 4. The dark areas in the figure represent the retained structure, while the remaining areas are areas where structural optimization design can be carried out.
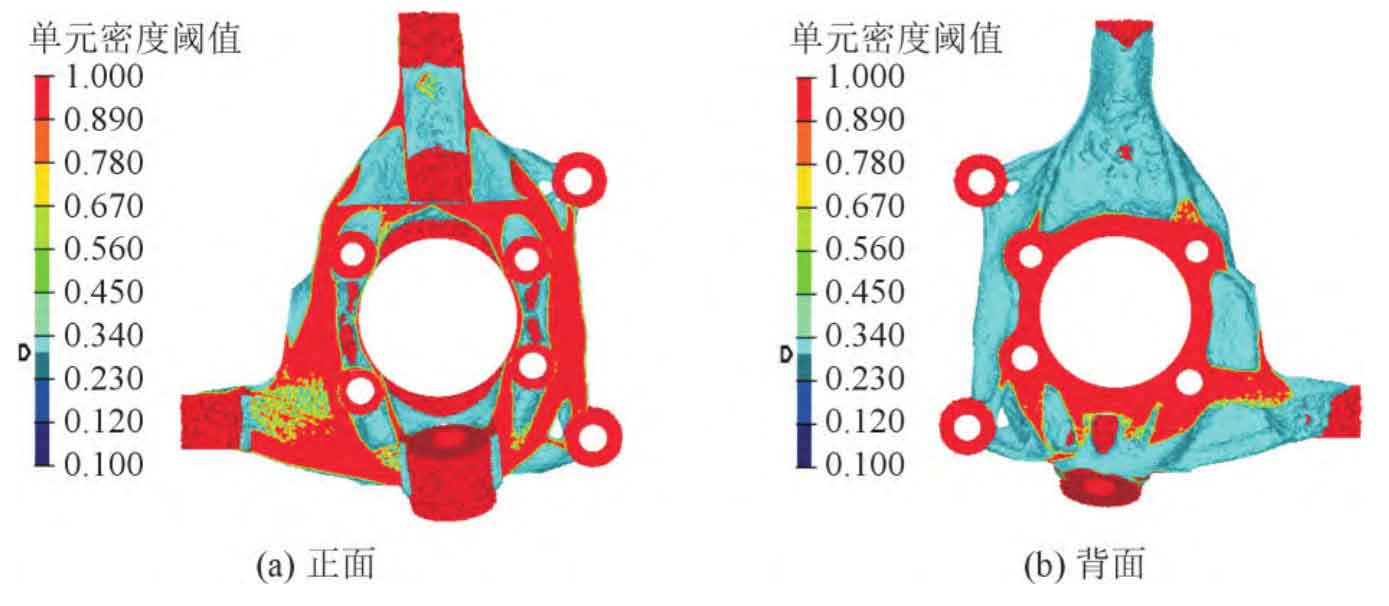
2. Structural design of squeeze cast aluminum alloy steering knuckles
2.1 Topology optimization structure design
Perform smoothing on the topology optimization results and import them into 3D software for structural optimization, as shown in Figure 5.
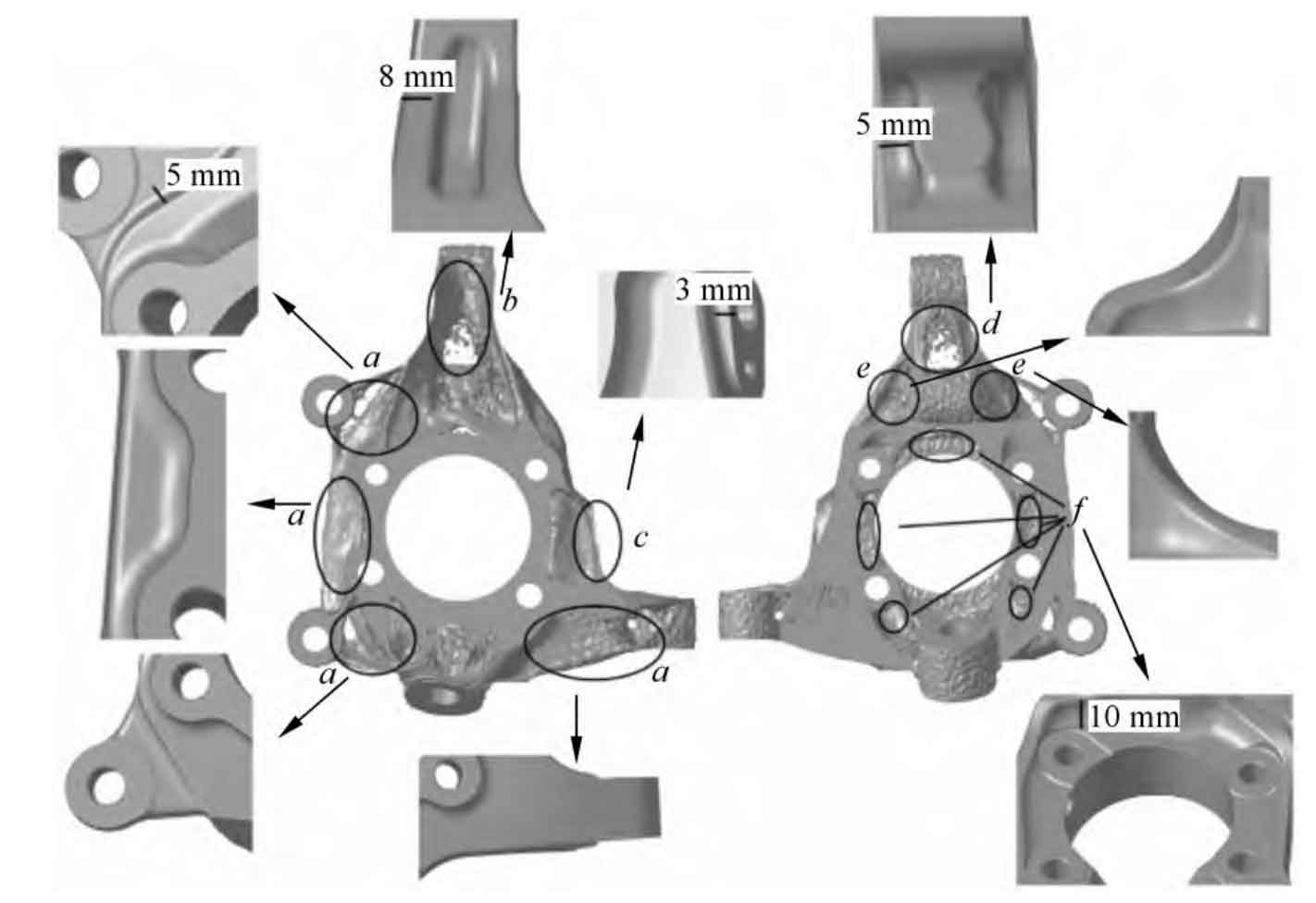
① Due to the large optimization area on the back of the steering knuckle, the entire surface is reduced by 5 mm; On this basis, further reduce the plane around the two holes connected around the brake caliper by 5 mm, as shown in area a optimization in Figure 5;
② Due to the deep optimization results in region B, in order to ensure the structural strength of the squeeze casting steering joint, a groove method was selected at a distance of about 8 mm from the boundary for material reduction;
③ Due to the deep optimization of dimensions in region C, in order to ensure structural strength, a protrusion with a height of about 3 mm is set on the side of the squeeze cast steering joint, and one through hole with a diameter of 10 mm and one blind hole with a diameter of 5 mm are opened. Through this structure, better exhaust can also be achieved during extrusion forming;
④ There are many optimizations in the center position of region D. In order to ensure strength, a reduction of approximately 5 mm in length was made on both sides, while also achieving assembly relationships with surrounding parts;
⑤ Reduce the material on both sides of the connection point e of the shock absorber, changing from an external convex shape to an internal concave shape;
⑥ Due to the influence of bidirectional molding, there is also a large optimization area on the front side of the squeeze casting steering joint, as shown in area f in Figure 5. The area around the center hole is reduced by about 10 mm to the entire surface.
2.2 Design of Squeeze Casting Forming Structure
Due to the use of squeeze casting technology, the requirements for demolding need to be considered. The structural model of the squeeze casting steering joint needs to be demolded, with a demolded angle of 5 °, and the parting surface determined. In addition, the design of some protrusions and grooves is to facilitate positioning in subsequent mechanical processing. Due to the use of a vertical squeeze casting machine, the molten metal is poured from the back to the front. In order to ensure the smooth and stable flow of the molten metal, it is necessary to design a guide rib structure. The structural design of the squeeze casting steering joint process is shown in Figure 6.
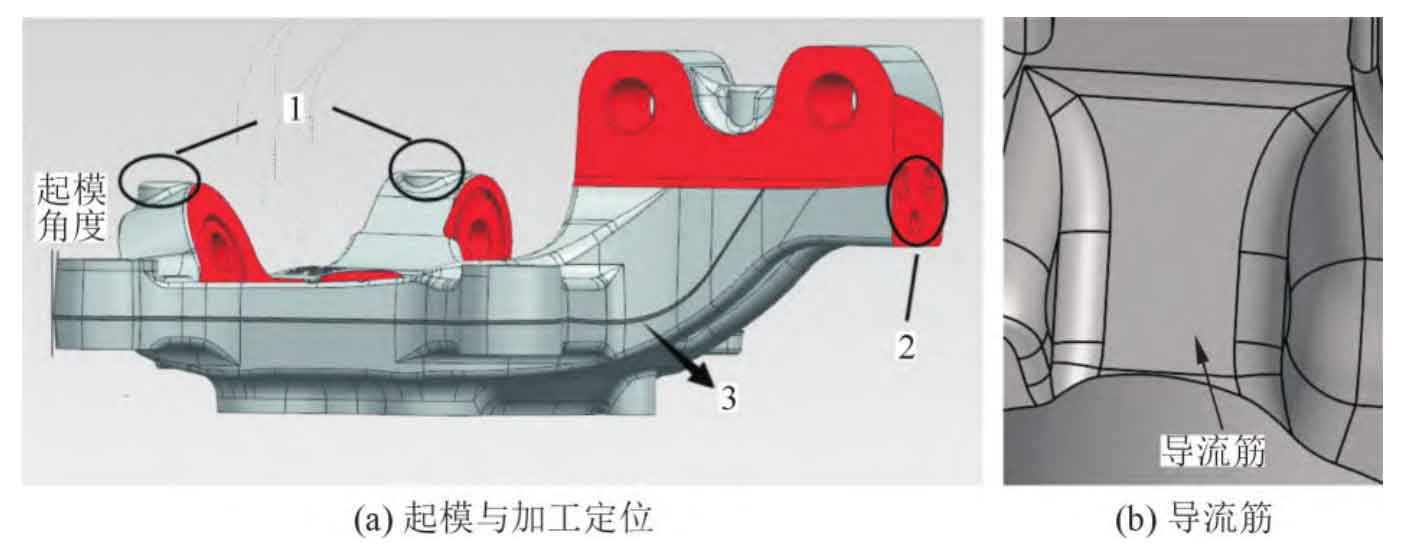
3. Finite element strength verification

Perform finite element analysis on the aluminum alloy squeeze casting steering joint model under the same operating conditions. After analysis, the stress cloud map under each working condition is shown in Figure 7, and the maximum stress under each working condition is shown in Table 2.
Working condition | 4x full load | Unilateral crossing | Crossing the threshold | Forward braking | Forward acceleration | Target requirements |
Maximum stress/MPa | 75.220 | 161.185 | 142.822 | 169.328 | 106.080 | ≤230 |
From Figure 7, it can be seen that the maximum stress of the aluminum alloy squeeze cast steering joint after structural optimization is much lower than the yield strength of the aluminum alloy (230 MPa), and the stress distribution is relatively uniform without stress concentration, meeting the structural strength requirements. At the same time, compared to ductile iron, the aluminum alloy squeeze casting steering joint reduces its weight by 60.9% and has a significant lightweight effect. The physical comparison of the two products is shown in Figure 8.
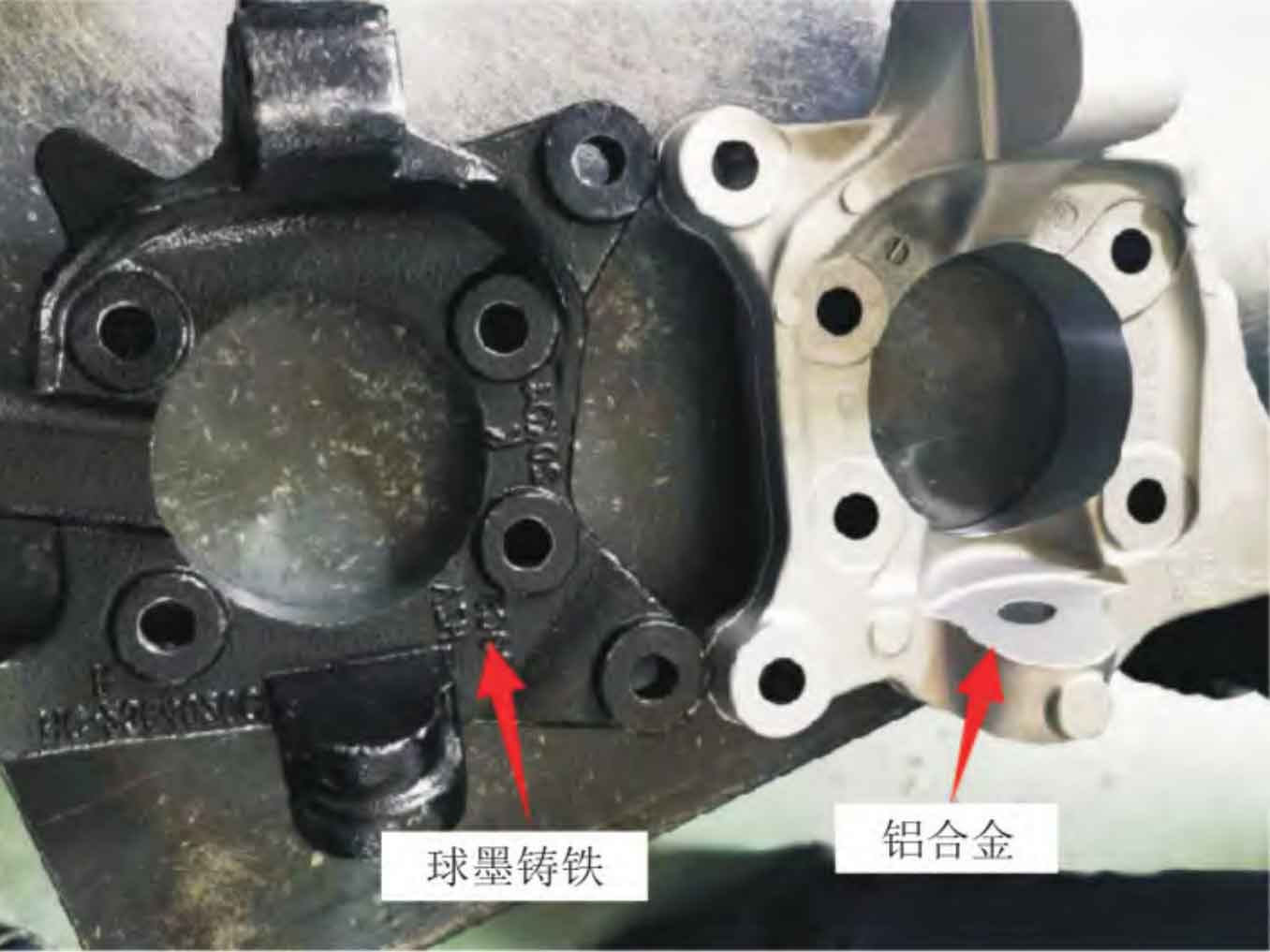
4. Mechanical performance verification
In order to eliminate internal structural segregation, improve microstructure, and enhance mechanical properties of the product, it is generally necessary to perform heat treatment on squeeze cast steering joint castings. The T6 heat treatment scheme for squeeze casting steering joint castings is a solid solution at 540 ℃ x 6 hours, water quenching at 60 ℃ for 5 minutes, and aging at 175 ℃ x 4 hours. The mechanical properties of the extruded cast steering joint after heat treatment were tested by taking tensile samples, as shown in Figure 9. The test results are shown in Table 3, which proves that the mechanical properties of the extruded cast steering joint after heat treatment meet the requirements.
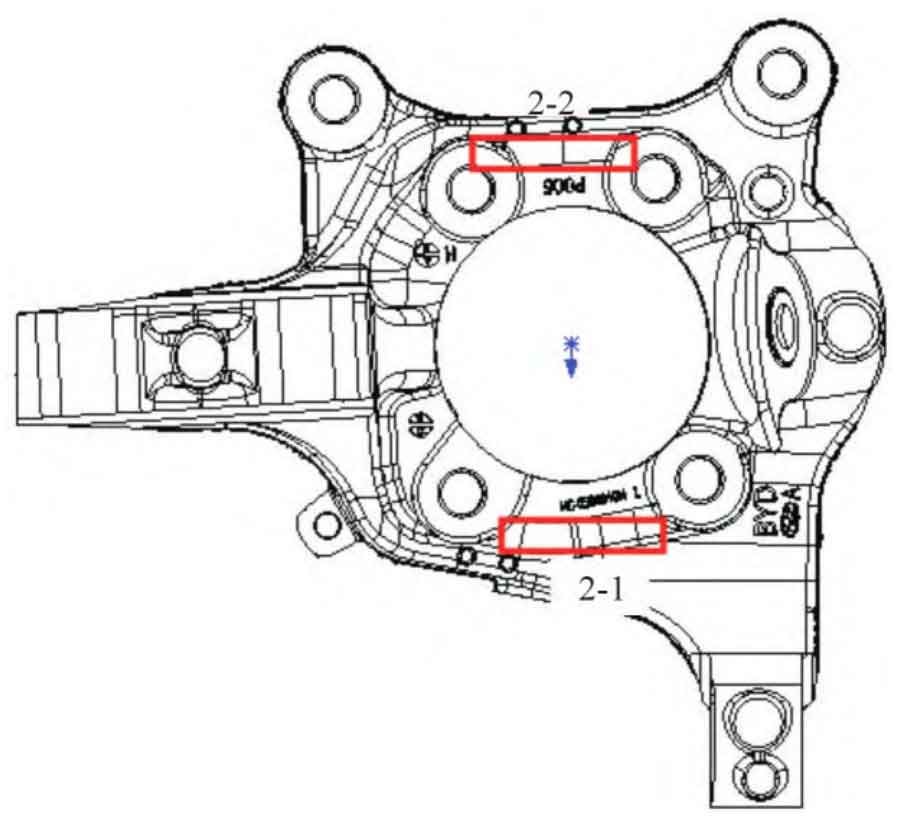
5. Conclusion
(1) Based on the method of variable density topology optimization, a mathematical model for topology optimization of squeeze casting steering knuckles was established, and the maximum solid model of squeeze casting steering knuckles was subjected to static multi working condition topology optimization using HyperMesh finite element analysis software. The results indicate that after 29 iterations, the flexibility gradually converges and eventually stabilizes.
(2) Based on the topology optimization results, the structure of the squeeze casting steering joint was optimized, and combined with the squeeze casting process, the structure of the squeeze casting steering joint was redesigned. The strength verification of the newly designed aluminum alloy squeeze casting steering joint model showed that the maximum stress on the squeeze casting steering joint under various working conditions was much lower than the yield strength, and the mass was reduced by 60.9% compared to ductile iron.
(3) T6 heat treatment was performed on the squeeze cast steering joint casting and mechanical performance testing was conducted. The results showed that the average tensile strength of the body sample was 311.03 MPa, yield strength was 252.13 MPa, and elongation was 7.45%, all of which were higher than the specified values of the product and met the performance requirements of the product.