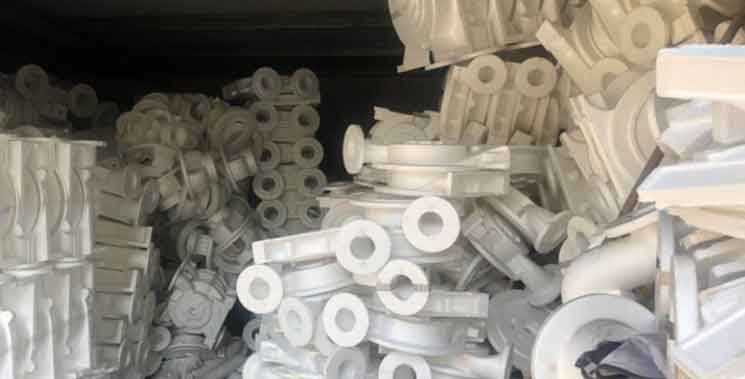
Lost foam casting is a complex process that can sometimes result in defects. Here are some common defects in lost foam casting, their potential causes, analysis methods, and possible solutions:
- Gas Porosity:
- Cause: Gas entrapment due to the decomposition of the foam pattern or improper venting.
- Analysis: X-ray or CT scanning, visual inspection, or metallographic examination.
- Solution: Improve foam pattern quality, optimize gating and venting systems, use coatings or additives to reduce foam decomposition, or increase mold permeability.
- Shrinkage Porosity:
- Cause: Insufficient feeding or inadequate material volume in certain areas.
- Analysis: Visual inspection, X-ray or CT scanning, or metallographic examination.
- Solution: Increase the size and number of risers, improve gating design, optimize pouring temperature and rate, or modify the casting geometry to ensure proper feeding.
- Incomplete Filling:
- Cause: Insufficient pouring time, inadequate gating design, or clogged vents.
- Analysis: Visual inspection, mold filling simulation, or flow visualization techniques.
- Solution: Optimize pouring time, improve gating design to ensure proper filling, clear or enlarge vents, or use flow aids or risers to promote complete filling.
- Surface Defects (Veining, Pinholes):
- Cause: Inadequate mold coating, excessive mold temperature, or improper metal temperature.
- Analysis: Visual inspection, surface analysis techniques, or metallographic examination.
- Solution: Apply high-quality mold coatings, control mold temperature, optimize pouring and metal temperature, use filters to remove impurities, or improve venting to release gases.
- Misruns and Cold Shuts:
- Cause: Improper gating, inadequate pouring temperature, or fast solidification.
- Analysis: Visual inspection, metallographic examination, or cooling curve analysis.
- Solution: Redesign gating system, adjust pouring temperature, use insulating or exothermic sleeves, increase pouring rate, or preheat molds to ensure proper solidification.
- Dimensional Inaccuracies:
- Cause: Pattern or mold distortion, thermal expansion/contraction, or improper cooling.
- Analysis: Dimensional measurement, comparison with design specifications, or simulation analysis.
- Solution: Optimize pattern design, control mold temperature, implement proper cooling techniques, use heat-resistant materials, or post-machining to achieve dimensional accuracy.
- Metal Penetration:
- Cause: Inadequate coating, excessive pouring temperature, or improper gating.
- Analysis: Visual inspection, surface analysis techniques, or metallographic examination.
- Solution: Apply high-quality coatings, control pouring temperature, improve gating and venting systems, or use barrier coatings to prevent metal penetration.
When troubleshooting defects in lost foam casting, it is essential to analyze the specific defect, identify the root cause, and implement appropriate solutions. Continuous process monitoring, quality control measures, and regular analysis of defects can help in improving the overall casting quality and reducing defects.