The turbine guide studied is composed of inner ring, blade and outer ring, and is in a complex frame structure. The thinnest part of the blade is only 1 mm. The geometric shape and sectional structure of the turbine blade are shown in the figure. The guide contains 38 blades and the outer ring diameter is φ 512.80 mm, 54.87 mm thick, inner ring diameter φ 334.00 mm。 From the sectional structure, it can be seen that the wall thickness of the turbine guide casting is thin and uneven, the thinnest wall thickness is 3.28 mm, the thickest wall thickness is 21.05 mm, and there is a thickness transition zone.
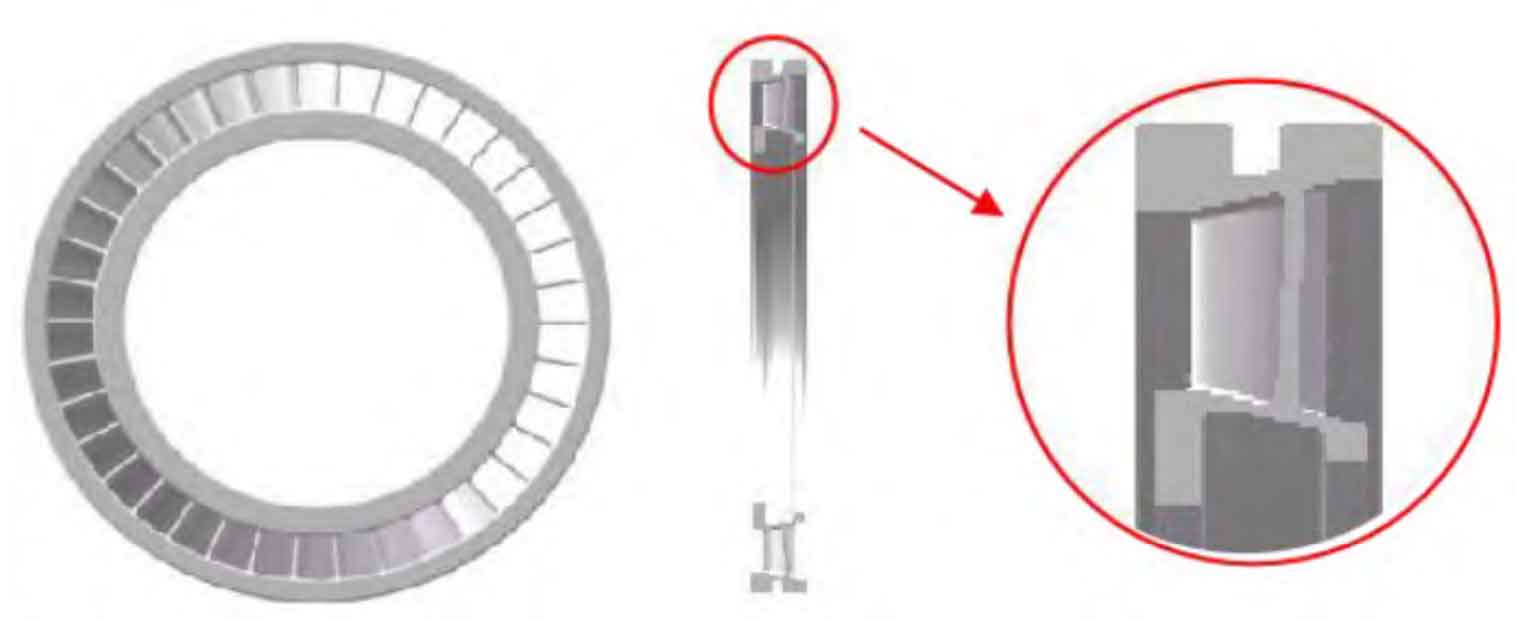
The guide structure is complex, especially the radial and axial torsion of the internal blade. The thickness of the exhaust edge of the guide vane is generally thin, which may lead to the risk of insufficient pouring at the exhaust edge. On the other hand, during solidification and cooling, it is easy to form thick columnar crystals perpendicular to the exhaust edge of the guide vane, which is caused by the temperature gradient between the thin exhaust edge and the thick leading edge of the vane. The coarse columnar crystal in the blade shortens the fatigue life of the turbine guide casting.
Through structural analysis, it can be seen that the biggest difficulties in the casting of this turbine guide are uneven wall thickness, large cross-section variation, and many alloy melt confluence points. Therefore, it is necessary to design the guide gating system reasonably to effectively control the solidification sequence.