Abstract
This article introduces the lost foam casting process of ultra-high chromium alloy impellers. By optimizing alloy composition, adopting a bottom pouring system, reasonably setting risers, utilizing inner cold iron, and implementing fine-grain strengthening measures, the castings achieve sequential solidification, eliminating defects such as shrinkage holes and cracks, and significantly improving abrasion resistance. The final product quality meets the requirements of acid corrosion conditions in slurry pump equipment.
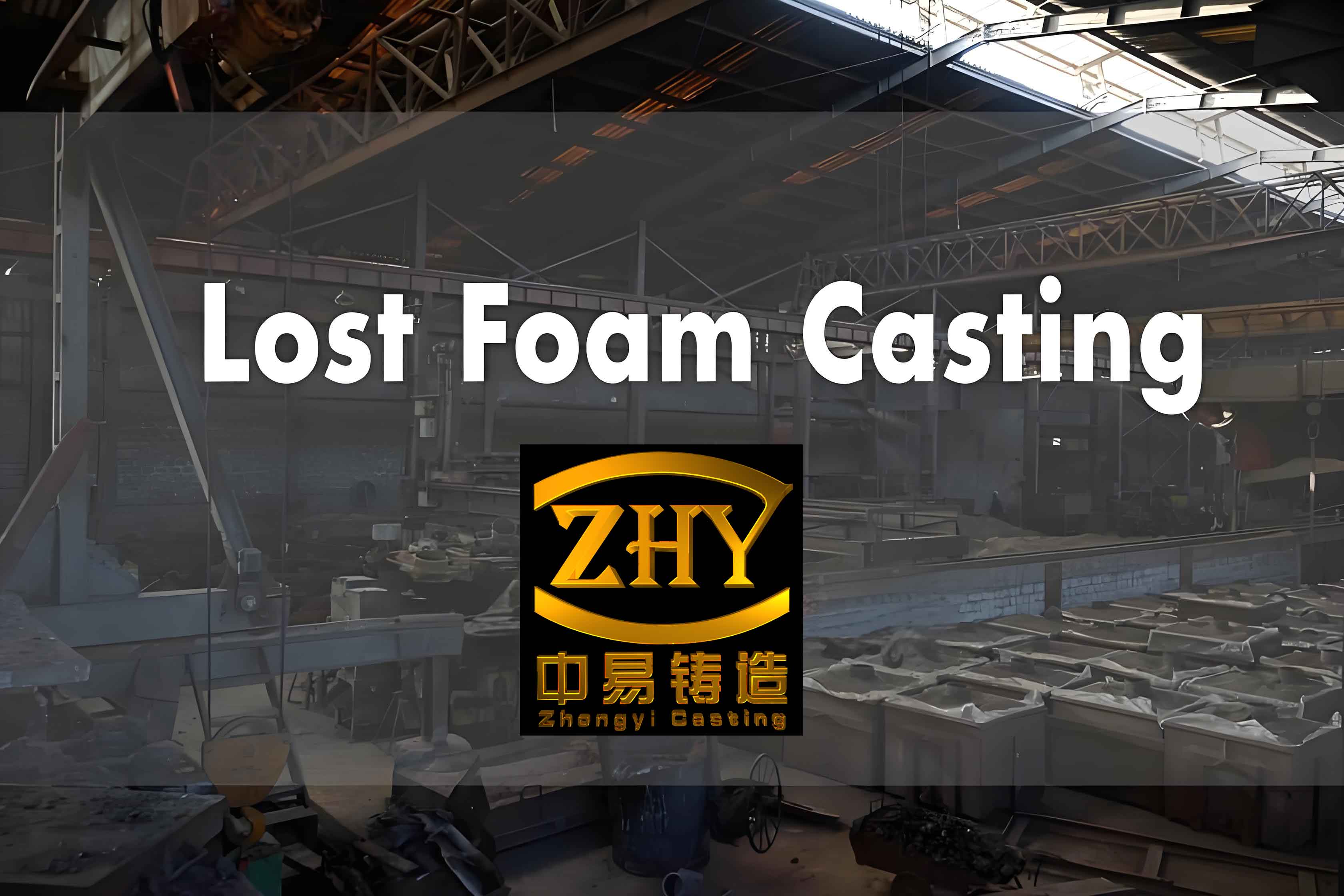
Keywords: ultra-high chromium alloy; impeller; lost foam casting; process design; defect
1. Introduction
In the operation of slurry pump equipment, the impeller, as the most critical component for performing work, undergoes severe wear due to chemical corrosion from acidic media (pH=1~2) and abrasive wear, erosion wear, and contact fatigue wear from solid particles. Once the impeller fails severely, the entire equipment will cease to function properly. The composition and morphological characteristics of the alloy are the primary factors determining the impeller’s resistance to various types of wear. Meanwhile, the well-designed lost foam casting process provides a technological guarantee for enhancing the comprehensive mechanical properties of impeller components.
This paper delves into the development of the lost foam casting process for ultra-high chromium alloy impellers, emphasizing alloy composition optimization, pouring system design, riser configuration, and fine-grain strengthening measures. Through these approaches, the castings achieve sequential solidification, eliminating defects and enhancing wear resistance, thereby meeting the operational requirements of slurry pump equipment under acidic conditions.
2. Alloy Composition Design
The chemical composition and element content of metallic materials are the foundation for obtaining the desired metallurgical structure. Casting processes and heat treatments influence phase transformations, morphologies, distributions, and mechanical properties, enabling materials to meet application requirements under different working conditions. By adjusting the chemical composition (Table 1) and process parameters, the desired metallurgical structure and mechanical properties are obtained to satisfy application needs under various conditions.
Table 1. Main Composition of Ultra-high Chromium Material (Mass Fraction, %)
Element | Mass Fraction (%) |
---|---|
C | 2.5~3.2 |
Cr | 33.0~45.0 |
Mo | 0.5~3.0 |
Ni | 3.0~6.0 |
Cu | 1.0~3.5 |
Ce | 0.03~0.1 |
2.1. Role of Major Alloying Elements
- Carbon (C): Carbon is the primary element forming carbides. Carbides exhibit high hardness, and increasing carbon content significantly boosts the number of carbides. A higher volume fraction of carbides is essential for ensuring material hardness and wear resistance. The carbon content is selected within the range of 2.5% to 3.2%.
- Chromium (Cr): Part of the chromium forms carbides, primarily M23C6-type carbides in low-carbon high-chromium alloys. Most chromium dissolves in the matrix, reducing the critical cooling rate and enhancing hardenability. A higher chromium content in the matrix is closely related to the Cr/C ratio. When the Cr/C ratio is high, it provides a compositional basis for obtaining a ferritic matrix morphology. Chromium is the element with the highest contribution to the high abrasion resistance of the alloy, and its addition ranges from 33.0% to 45.0%.
- Molybdenum (Mo): Molybdenum has a significant solubility in both α-iron and γ-iron, exhibiting excellent solid solution strengthening and resistance to temper softening. When molybdenum is dissolved in M7C3-type carbides, replacing some chromium and iron atoms, it forms higher metallic bond energy, significantly improving the material’s high-temperature chemical stability and resistance to high-temperature wear. The molybdenum content is set at 0.5% to 3.0%.
- Nickel (Ni): Nickel does not form carbides but mainly dissolves in the matrix. Nickel is an austenite-stabilizing element, expanding the austenite phase region. At higher concentrations, it allows the high-temperature stable austenite phase to persist to room temperature. Nickel also enhances the material’s corrosion resistance, hardenability, and toughness. In combination with molybdenum and chromium, nickel significantly improves the material’s thermal strength, thermal fatigue strength, and high-temperature oxidation resistance. The nickel content is controlled within the range of 3.0% to 6.0%.
- Copper (Cu): Copper cannot form compounds with carbon but can exist in alloy carbides. When copper and molybdenum are added together to high-chromium alloys, they delay the incubation period of austenite transformation and improve hardenability. Copper raises the electrode potential of iron-carbon alloys, enhancing the material’s corrosion resistance in acidic media. The copper content is controlled within the range of 1.0% to 3.5%.
- Cerium (Ce): Cerium is a surface-active element added as a modifier in the form of cerium-based rare earths. Cerium selectively adsorbs on eutectic carbides, mainly accumulating in the growth direction of eutectic carbides during eutectic solidification. It hinders the normal growth of iron, chromium, and carbon atoms into carbide crystals, reducing the growth rate of the leading phase of eutectic carbides in this direction, forcing eutectic carbides to become smaller and duller. Cerium increases austenite nucleation, resulting in a denser, finer, and more uniform austenite structure. The refinement of carbide and austenite grains significantly improves material toughness and wear resistance. The cerium content is within the range of 0.03% to 0.1%.
3. Microstructural Analysis
Based on the alloy’s chemical composition and the Fe-Cr-C ternary phase diagram, the eutectic carbon equivalent (CE) of low-carbon ultra-high chromium alloys is 2.3%, classifying them as hypoeutectic high-chromium cast iron. The primary carbide morphology is (Fe, Cr)23C6, with a volume fraction of 30%.
During solidification, as the temperature decreases, low-carbon austenite phase precipitates first from the liquid phase, with coarse primary austenite grains. As the temperature further decreases, the liquid phase decreases, and the carbon concentration increases, reaching the eutectic reaction state, where a eutectic transformation occurs: L → A + Fe3C. With further temperature reduction, the austenite precipitated during the ternary eutectic reaction transforms most of the secondary M23C6 carbides into high-chromium ferrite, while the remaining austenite remains in the room temperature microstructure.
Ternary high-chromium cast iron has a wide solidification temperature range, coarse grains, low impact toughness, and high brittleness, requiring heat treatment to refine grains and improve strength and abrasion resistance. The metallographic structure after heat treatment (etched with aqua regia) consists of 45% ferrite, 25% austenite, and 30% carbides (eutectic carbide M23C6 and secondary carbides). The microstructural morphology determines the material’s suitable strength, high abrasion resistance, and good impact toughness.
4. Casting Process Design and Fine-grain Strengthening
4.1. Pouring System Design
The impeller employs the lost foam casting process, where liquid metal is poured under negative pressure, causing the foam pattern cluster to gasify and decompose, with the iron liquid replacing the pattern cluster and solidifying to form the casting. The interface between the advancing iron liquid front and the foam absorbs heat, while the replacement process also hinders the forward movement of the iron liquid, slowing down the filling speed. Therefore, when designing the pouring system, based on the theory of large outlet flow, the cross-sectional area of each part of the pouring system is increased (1.3 to 2.2 times that of resin sand cavity pouring), and a bottom-pouring system is adopted, with a raised slag-collecting structure added at the end of the cross runner. The ingates are distributed at the intersection of the two blades and the front and rear cover plates, allowing the iron liquid to advance steadily from the blades upwards. The bottom-pouring system with a large outlet for rapid filling ensures a smooth flow of iron liquid and a smaller temperature gradient, preparing for balanced solidification of the impeller.
4.2. Riser Design
Due to the ultra-high chromium content of the impeller material, the alloy exhibits significant shrinkage. In the design of the lost foam process, the risers need to be enlarged to prevent the formation of shrinkage pores and porosity. However, the high volume fraction of carbides in the alloy increases material brittleness and reduces toughness. Enlarging the risers will inevitably lead to stress concentration and superposition, increasing the potential risk of cracks in the casting.
In the context of the lost foam casting process for ultra-high chromium alloy impellers, riser design is a crucial aspect that significantly impacts the quality of the final castings. The ultra-high chromium content of the impeller material results in significant alloy shrinkage during solidification. To address this issue, the risers in the casting process need to be enlarged to ensure effective feeding and prevent the formation of shrinkage pores and porosity.
However, there are also challenges associated with enlarging the risers. The high volume fraction of carbides in the alloy increases its brittleness and reduces toughness. This makes the alloy more susceptible to cracking, especially under stress concentrations. Enlarging the risers, therefore, inevitably leads to stress concentration and superposition in the casting, increasing the potential risk of cracks.
To balance these considerations, the riser design in the lost foam casting process of ultra-high chromium alloy impellers must be carefully planned. The following are some key points to consider:
- Equilibrated Solidification Theory: The riser design should strictly follow the equilibrated solidification theory. This involves ensuring that the risers are strategically placed to provide effective feeding to the hot spots in the casting, such as the intersections of the impeller hub, blades, and cover plates.
- Riser Size and Shape: The size and shape of the risers need to be optimized to balance the need for effective feeding and the risk of stress concentration. The risers should be large enough to provide sufficient feeding material but not too large to cause excessive stress concentration. The diameter and height of the risers should be carefully calculated based on the hot spot size and the alloy’s shrinkage characteristics.
- Riser Placement: The risers should be placed in locations that minimize stress concentration and maximize feeding efficiency. For example, in the case of ultra-high chromium alloy impellers, risers can be placed on both sides of the hub, aligning with two blades, to efficiently feed the hub hot spot. Additionally, venting and slag-removing risers can be placed at the top of the impeller to weaken the adverse effects of the wall-attachment effect and prevent slag defects.
- Stress Mitigation: To further reduce the risk of cracks, measures such as embedded sleeves can be used as internal chills to increase the supercooling of the iron liquid and achieve fine-grain strengthening. This helps to refine the grain structure, improve the morphology, structure, and distribution of carbides, and enhance the overall mechanical properties of the material.
In conclusion, riser design in the lost foam casting process of ultra-high chromium alloy impellers requires a delicate balance between effective feeding and stress concentration management. By carefully planning the size, shape, and placement of the risers, and incorporating additional measures such as internal chills, it is possible to produce high-quality castings that meet the demanding requirements of abrasive and erosive applications.