Casting defects can have a significant impact on the quality and integrity of metal components. Identifying the root causes behind these defects is crucial for implementing effective solutions and improving the casting process. This article aims to uncover the hidden culprits behind casting defects by exploring their root causes and providing insights into how to address them.
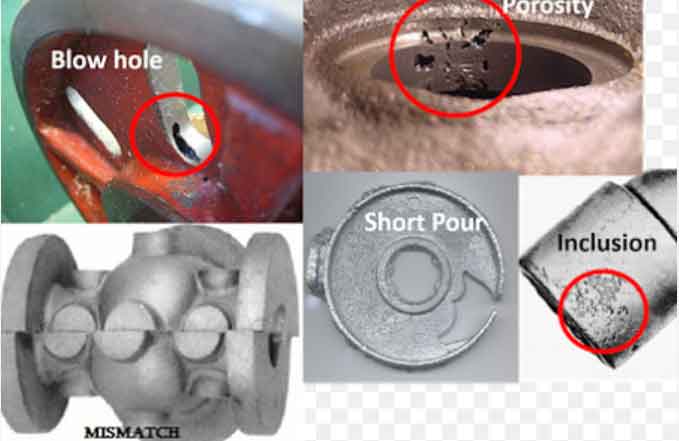
- Inadequate Mold Design:
- Insufficient gating and riser design can result in improper metal flow, inadequate feeding, and subsequent defects such as porosity, shrinkage, and misruns.
- Poor venting in the mold can lead to trapped gases, causing porosity defects.
- Inappropriate Material Selection:
- Improper choice of casting material in terms of alloy composition, purity, or mechanical properties can contribute to defects such as inclusions, segregation, and poor dimensional stability.
- Material contamination or improper handling can introduce impurities into the molten metal, leading to defects in the casting.
- Poor Pouring and Solidification Practices:
- Inconsistent pouring temperature and rate can cause issues like cold shuts, misruns, and inadequate filling of the mold cavity.
- Inadequate control of solidification time and cooling rates can result in shrinkage defects and uneven solidification, leading to warpage and distortion.
- Improper Melting and Treatment:
- Inadequate melting techniques, such as insufficient degassing or improper alloying, can introduce gas-related defects like porosity and blowholes.
- Insufficient or incorrect use of fluxes and additives can contribute to inclusions and slag defects.
- Lack of Process Control and Monitoring:
- Inconsistent process parameters, such as improper mold temperature, inadequate venting, or incorrect pouring speed, can lead to defects in the casting.
- Insufficient process monitoring and control can result in variations and deviations that contribute to defects.
- Insufficient Training and Skills:
- Inadequate knowledge and skills of foundry personnel can lead to improper handling of equipment, incorrect process implementation, and a higher likelihood of defects.
- Lack of awareness and understanding of defect recognition and prevention strategies can hinder the ability to address and resolve casting defects effectively.
- Design-related Factors:
- Poor design choices, such as sharp corners, thin sections, or inadequate fillets, can contribute to defects like cracks, shrinkage, and improper filling.
- Insufficient consideration of the casting process during component design can lead to challenges in achieving defect-free castings.
Uncovering the root causes of casting defects is essential for improving the overall quality of metal components. By addressing issues related to mold design, material selection, pouring and solidification practices, melting and treatment techniques, process control and monitoring, training and skills, and design considerations, manufacturers can effectively minimize casting defects. Implementing comprehensive quality control measures, investing in personnel training and development, and fostering a culture of continuous improvement are key to overcoming the hidden culprits and achieving defect-free castings.