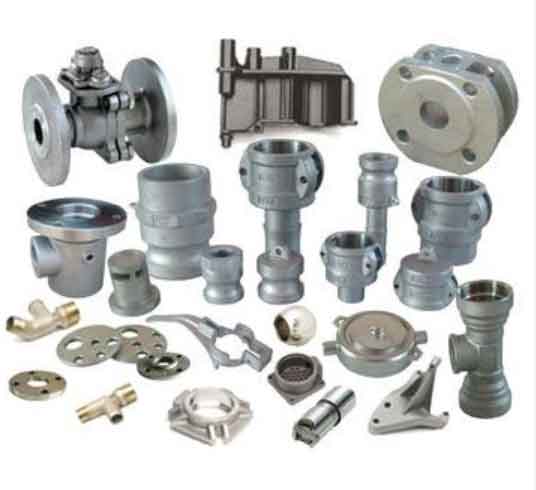
Sustainable sand casting refers to practices and initiatives that aim to minimize the environmental impact of the casting process and promote the efficient use of resources. It involves adopting environmentally friendly practices and implementing recycling measures throughout the casting lifecycle. Here are some key aspects of sustainable sand casting:
- Reduced energy consumption: Sustainable sand casting focuses on optimizing energy consumption during the manufacturing process. This can be achieved through the use of efficient equipment, process control systems, and improved insulation. Energy-efficient furnaces, for example, can significantly reduce energy consumption during the melting and pouring stages.
- Eco-friendly molding materials: Traditional sand molds often use organic binders, such as resins, that can release harmful emissions during the casting process. Sustainable sand casting promotes the use of eco-friendly binder systems, such as water-based or clay-based binders, which have lower emissions and are more environmentally friendly. These alternative binder systems minimize the release of volatile organic compounds (VOCs) and contribute to improved air quality in the foundry.
- Recycling and reuse of sand: Sand used in sand casting can be recycled and reused to minimize the need for new sand and reduce waste. Foundries employ sand reclamation techniques to separate the sand from the castings, remove impurities, and restore its properties for reuse. By recycling sand, foundries can significantly reduce the demand for new sand, conserve natural resources, and minimize waste generation.
- Scrap metal recycling: In addition to sand recycling, sustainable sand casting promotes the recycling of scrap metal generated during the casting process. Metal scraps and rejected castings can be collected and recycled back into the production process, reducing the need for new raw materials and minimizing waste disposal.
- Water conservation: Sustainable sand casting initiatives focus on water conservation measures to minimize water usage during the casting process. Foundries can implement closed-loop water systems, water treatment technologies, and process optimization strategies to reduce water consumption and minimize the impact on local water resources.
- Waste management and emissions control: Sustainable sand casting emphasizes proper waste management practices, including the handling, segregation, and disposal of waste materials. Foundries implement measures to reduce waste generation and ensure proper treatment of hazardous materials. Additionally, emissions control systems, such as dust collectors and air filtration systems, are employed to minimize the release of pollutants into the atmosphere.
- Life cycle assessment (LCA): Life cycle assessment is a tool used to evaluate the environmental impact of the entire sand casting process, from raw material extraction to end-of-life disposal. By conducting an LCA, foundries can identify areas of improvement, quantify the environmental footprint of their operations, and implement strategies to reduce overall environmental impact.
By adopting sustainable practices in sand casting, foundries can minimize their environmental footprint, conserve resources, and contribute to a more sustainable and responsible manufacturing industry. These initiatives not only benefit the environment but also align with the growing demand for environmentally friendly products from consumers and regulatory bodies.