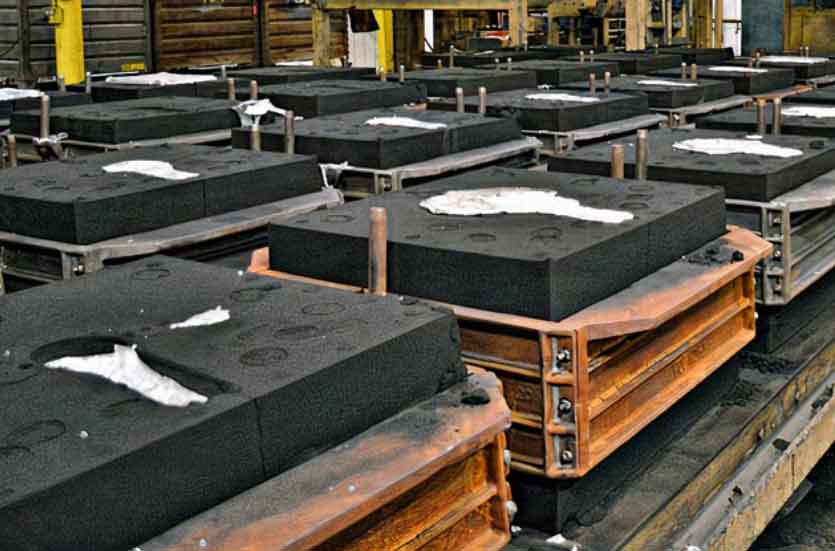
The chemistry behind resin sand casting involves the interaction of materials and binders to create the sand molds used in the casting process. Understanding these components is essential for successfully implementing resin sand casting. Let’s take a closer look at the key materials and binders involved in this process:
Materials Used in Resin Sand Casting:
- Sand: Sand is the primary molding material used in resin sand casting. It provides the shape of the mold and supports the cavity into which molten metal is poured. The sand used in resin sand casting is usually silica sand due to its excellent refractory properties and availability.
- Resin Binder: Resin serves as the binding material that holds the sand grains together to form a solid mold. It imparts strength to the mold and enables the sand to maintain its shape during handling, pouring, and solidification of the metal. The two common types of resin binders used in resin sand casting are:
- a. Furan Resin: Furan resin is a thermosetting resin derived from furfuryl alcohol. When mixed with sand, it undergoes a chemical reaction upon curing, forming a strong and rigid mold.
- b. Urethane Resin: Urethane resin, also known as polyurethane resin, is another commonly used binder in resin sand casting. It is mixed with sand and undergoes a curing process to create a strong and durable mold.
Chemistry of Resin Curing:
The curing process of the resin binder is critical for forming a robust sand mold. It involves a chemical reaction called polymerization, where the resin molecules cross-link with each other and with the sand grains to create a solid network. The curing process for furan and urethane resins differs:
- Furan Resin Curing:Furan resin curing typically involves two steps:
- a. Activation: The sand is mixed with a liquid activator, which is usually an acid or an acid salt. The activator reacts with the furfuryl alcohol in the furan resin, creating an intermediate product known as the furan no-bake binder.
- b. Curing: The furan no-bake binder is then exposed to heat, which triggers a polymerization reaction, cross-linking the resin and solidifying the mold.
- Urethane Resin Curing:Urethane resin curing involves a two-part system:
- a. Prepolymer: The urethane resin is pre-mixed with a polyol component, creating a prepolymer. The polyol component contains hydroxyl groups.
- b. Curing Agent: Before the mold-making process, a curing agent, usually an isocyanate compound, is added to the prepolymer. The isocyanate reacts with the hydroxyl groups in the prepolymer, causing polymerization and curing of the resin.
The curing process is typically carried out at room temperature, and the time required for curing depends on the specific resin and binder system used.
Understanding the chemistry behind resin sand casting is crucial for optimizing the molding process, ensuring strong and durable molds, and achieving high-quality castings. Manufacturers can tailor the resin and binder system to meet specific casting requirements, enabling the production of complex shapes and precise components in a cost-effective and sustainable manner.