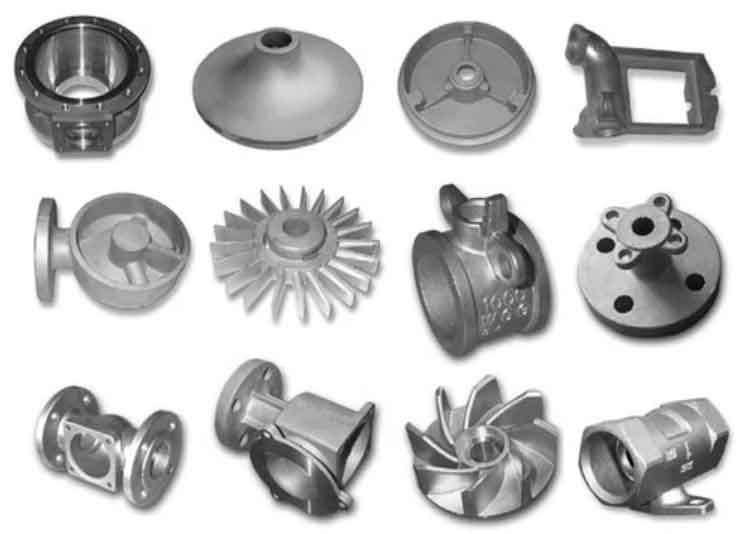
Sand casting continues to unlock significant potential in modern manufacturing due to its versatility, cost-effectiveness, and ability to produce complex and large-scale components. Let’s explore how sand casting unleashes its potential in today’s manufacturing landscape:
Design Flexibility:
Sand casting offers design freedom, allowing for the creation of intricate and complex geometries. Designers can incorporate undercuts, thin walls, and internal features that may be challenging or costly to achieve with other manufacturing processes. This flexibility enables innovative product designs and the realization of unique component shapes.
Versatility in Material Selection:
Sand casting accommodates a wide range of metal alloys, including ferrous and non-ferrous materials. From aluminum and copper alloys to steel and iron, sand casting allows manufacturers to choose the most suitable material for the desired mechanical properties, corrosion resistance, or heat resistance of the final component.
Cost-Effective for Medium to Large Production Runs:
Sand casting is particularly cost-effective for medium to large production runs. The low initial tooling costs and the ability to use readily available and relatively inexpensive materials, such as sand and pattern materials, make sand casting a cost-efficient option. The scalability of the process allows for economical production of high-quality components.
Prototyping and Rapid Iteration:
Sand casting is well-suited for prototyping and rapid iteration in the product development cycle. The low-cost tooling and shorter lead times compared to other casting methods make it an ideal choice for producing functional prototypes for testing, evaluation, and validation. Design changes and iterations can be easily incorporated into the sand molds, enabling quick refinements and improvements.
Large Component Production:
Sand casting is capable of producing large and heavy components, making it suitable for industries that require such parts. Industries such as automotive, aerospace, energy, and construction benefit from sand casting’s ability to manufacture critical components like engine blocks, turbine housings, pump bodies, and structural parts.
Complex Geometry and Internal Features:
Sand casting allows for the creation of components with intricate geometries and internal features. The use of sand cores enables the production of complex internal cavities, such as cooling passages, hollow sections, or intricate patterns. This capability is particularly advantageous in industries where components require precise internal structures.
Scalability and High Production Rates:
Sand casting can be scaled up to accommodate high production rates while maintaining cost-effectiveness. With optimized process parameters, efficient mold handling, and advanced pouring techniques, sand casting foundries can achieve consistent and reliable production rates, meeting the demands of various industries.
Sustainability and Environmental Considerations:
Sand casting has made significant progress in terms of sustainability. The implementation of sand reclamation processes, the use of environmentally friendly binders, and the optimization of energy consumption contribute to sustainable manufacturing practices. Additionally, the recyclability and reusability of sand and other materials used in sand casting minimize waste generation and reduce the environmental impact.
Sand casting continues to play a vital role in modern manufacturing, offering unique advantages and unlocking its potential across various industries. Its versatility, cost-effectiveness, design flexibility, and ability to produce complex and large-scale components make it a preferred choice for manufacturers looking for reliable and efficient production methods. With advancements in process control, automation, and material science, sand casting is poised to continue thriving in the ever-evolving manufacturing landscape.