Chapter 1:The Strength of White Cast Iron
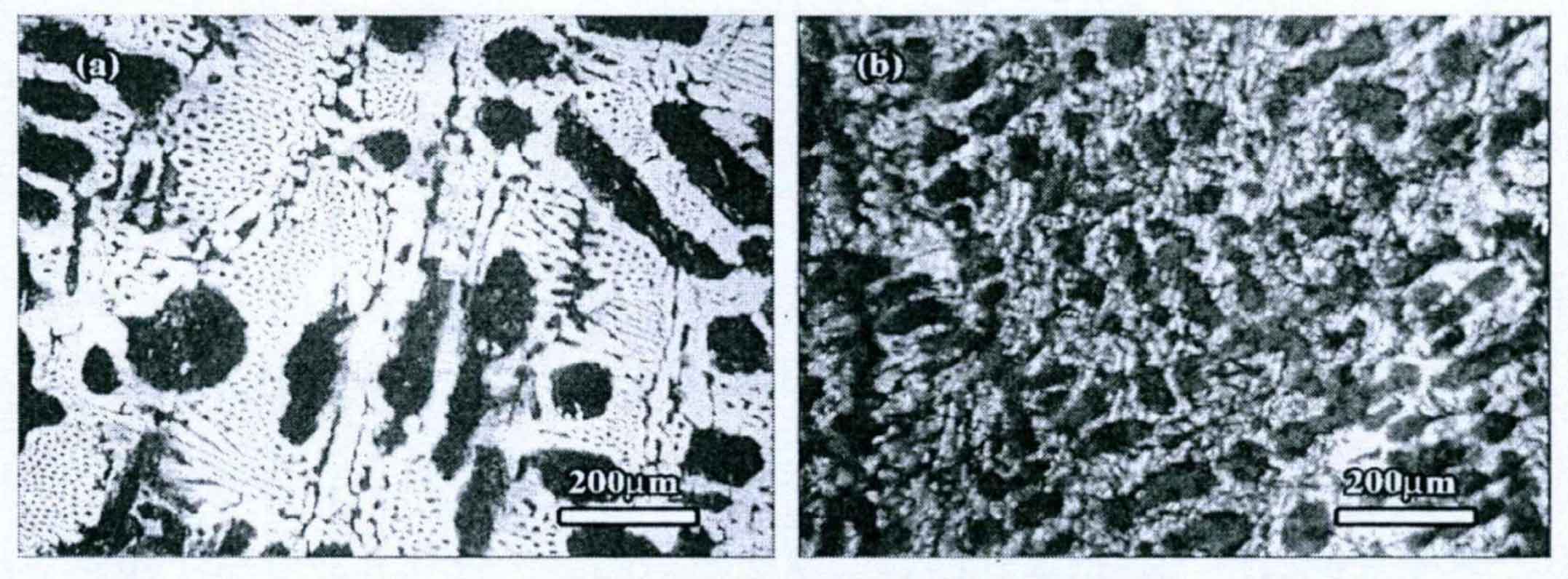
White cast iron is a type of cast iron known for its hardness and wear resistance, making it a valuable material in various engineering and manufacturing applications. Here’s an analysis of its impact in these fields:
- Composition and Properties: White cast iron is characterized by its microstructure, which contains iron carbide or cementite. This makes it hard and brittle. Unlike gray cast iron, which has graphite flakes, the carbon in white cast iron is bonded with iron, forming iron carbide. This composition gives it high compressive strength and excellent wear resistance but also makes it difficult to machine.
- Applications in Engineering:
- Wear-Resistant Surfaces: Due to its hardness, white cast iron is used in areas where abrasion resistance is crucial. This includes parts like liners for cement mixers, coal grinding mills, shot blasting units, and extrusion nozzles.
- Cutting and Grinding Tools: Its wear resistance makes it suitable for cutting tools and machinery parts that need to maintain their shape under stress.
- Automotive Industry: It’s used in brake shoes, clutch plates, and various other components where durability is necessary.
- Manufacturing and Machinability: The brittleness of white cast iron poses challenges in machining. It cannot be shaped easily by conventional methods and often requires special tools. However, its resistance to deformation makes it suitable for castings that require intricate shapes and sizes.
- Impact on Industry:
- Cost-Effectiveness: While difficult to machine, it’s often more cost-effective in the long term for components that require high wear resistance.
- Energy and Material Efficiency: Its durability means less frequent replacement, reducing material usage and energy in manufacturing.
- Design Flexibility: Advances in metallurgy have allowed more flexibility in designing components with white cast iron, adapting it for more specialized applications.
- Limitations and Alternatives: Due to its brittleness, it’s not suitable for parts that undergo a lot of tension or bending. Ductile iron or other steel alloys are sometimes used instead when toughness is as important as wear resistance.
- Advancements and Future Prospects: Ongoing research in alloying and treatment processes aims to enhance the toughness and machinability of white cast iron, widening its range of applications. This includes the development of alloyed white cast irons and heat treatment methods to modify its microstructure for specific needs.
White cast iron plays a critical role in engineering and manufacturing, particularly where wear resistance and hardness are paramount. Its impact is seen in the longevity and performance of parts and machinery across various industries, although it comes with limitations in machinability and toughness.
Chapter 2: Exploring the Durability of White Cast Iron in Heavy-Duty Applications
White cast iron is renowned for its exceptional durability, especially in heavy-duty applications. This durability is due to its unique microstructure and properties. Let’s explore how these characteristics make white cast iron a prime choice for such applications:
- Microstructure and Hardness: The key to the durability of white cast iron lies in its microstructure, which is predominantly composed of cementite (iron carbide, Fe3C). Cementite is a hard compound, and its presence imparts high hardness and wear resistance to white cast iron. This hardness is crucial in heavy-duty applications where components are subject to constant abrasion and wear.
- Wear Resistance: In industries where machinery parts are exposed to abrasive materials or surfaces, white cast iron is often a material of choice. Its wear resistance is particularly beneficial in mining, milling, and grinding applications, where components like crusher liners, mill liners, and slurry pump parts are subjected to extreme wear.
- Resistance to Deformation: The rigid structure of white cast iron makes it highly resistant to deformation under high stress. This makes it suitable for applications involving heavy loads or high pressures, like in heavy machinery and industrial installations.
- Heat Treatment for Improved Properties: While inherently brittle, the properties of white cast iron can be enhanced through heat treatment processes. These processes can increase toughness and make the material more suitable for heavy-duty applications where some level of impact resistance is required alongside wear resistance.
- Applications in Heavy Machinery: White cast iron finds extensive use in the manufacturing of parts for heavy machinery. This includes gears, cutting edges of digging implements, rail car wheels, and other components where durability under high-stress conditions is crucial.
- Limitations: Despite its advantages, the brittleness of white cast iron can be a limiting factor. It’s generally not suitable for applications where impact resistance is a primary requirement, as it can fracture under shock loads. This limitation often necessitates a trade-off between wear resistance and toughness.
- Advancements and Alternatives: The industry continues to explore ways to enhance the toughness of white cast iron without significantly compromising its wear resistance. Additionally, alternative materials like high-chromium white irons, which offer better toughness while retaining good wear resistance, are being developed for more demanding applications.
In conclusion, the durability of white cast iron in heavy-duty applications lies in its exceptional wear resistance and ability to withstand high-stress conditions. This makes it ideal for many industrial and heavy machinery components. However, its brittleness requires careful consideration in applications where impact resistance is also important. Advances in material science are continually expanding its range of applications by improving its overall property profile.
Chapter 3: White Cast Iron Vs. Gray Cast Iron: Understanding the Differences
White cast iron and gray cast iron are two distinct types of cast iron with different properties and uses. Let’s look at the key differences between them:
- Carbon Content and Structure:
- Gray Cast Iron: Contains more silicon and a form of carbon known as graphite. The carbon in graphite form gives gray iron its characteristic gray color when fractured.
- White Cast Iron: Has lower silicon content and contains carbon in the form of iron carbide (cementite). This gives it a white fracture surface.
- Mechanical Properties:
- Gray Cast Iron: It is known for its excellent damping properties and good machinability due to the presence of graphite. It’s not as hard as white cast iron but has good compressive strength.
- White Cast Iron: Is much harder and more brittle due to the presence of cementite. It has a higher wear resistance but is more difficult to machine.
- Applications:
- Gray Cast Iron: Commonly used in applications where vibration damping is important, like engine blocks, machine tool bases, and large frames. It’s also used for pipes, automotive brake disks, and gearboxes.
- White Cast Iron: Used in applications requiring high wear resistance. Common uses include liners for cement mixers, ball mills, and parts of mining machinery.
- Machinability and Weldability:
- Gray Cast Iron: Easier to machine and can be cut by a lathe or mill. However, it’s not suitable for welding due to its high carbon content, which can cause cracking.
- White Cast Iron: Very hard to machine and generally requires grinding. It’s also difficult to weld for the same reasons as gray cast iron.
- Heat Treatment:
- Gray Cast Iron: Doesn’t undergo heat treatment processes frequently, as it’s already suitable for many applications in its as-cast state.
- White Cast Iron: Can be heat-treated to produce malleable iron or ductile iron, which have better ductility and toughness.
- Cost and Availability:
- Gray Cast Iron: More commonly available and generally less expensive than white cast iron.
- White Cast Iron: Less common and can be more expensive, particularly if additional processing like heat treatment is required.
In summary, the choice between white and gray cast iron depends on the specific requirements of the application, such as the need for wear resistance, machinability, vibration damping, and cost considerations. Gray cast iron is more versatile for general purposes, while white cast iron is specialized for high wear-resistant applications.
Chapter 4: The Role of White Cast Iron in Modern Metallurgy and Its Future Potential
White cast iron plays a significant role in modern metallurgy and has promising future potential. Here’s a detailed look at its role and potential:
Current Role in Metallurgy:
- Wear Resistance and Hardness: White cast iron is renowned for its high hardness and wear resistance. This is due to its microstructure, which contains hard iron carbides in a matrix of martensite or pearlite. These properties make it ideal for components subjected to severe abrasion and wear, such as in mining, milling, and earth handling.
- Manufacturing of Grinding Media: It is extensively used in the manufacturing of grinding media, like balls used in ball mills for mineral processing. The hardness and wear resistance ensure the longevity of these grinding components, reducing the need for frequent replacements.
- Production of Wear-Resistant Castings: It’s utilized in producing various wear-resistant castings, such as liners for cement mixers, rolls for crushing grains in milling operations, and parts for agricultural machinery.
- Cost-Effectiveness: Despite its brittleness, white cast iron is often preferred in applications where its wear resistance and hardness can be capitalized on. It’s more cost-effective than other wear-resistant materials like high carbon steels or certain alloys.
- As a Source for Malleable Iron: White cast iron can be heat-treated to produce malleable iron, which is less brittle and more workable. This expands its applications in industries that require a balance of toughness and strength.
Future Potential:
- Alloy Development: Ongoing research in metallurgy focuses on developing new alloys of white cast iron with enhanced properties like better resistance to corrosion, heat, and even more improved wear resistance.
- Composite Materials: There’s potential in creating composite materials combining white cast iron with other metals or non-metals to exploit the benefits of multiple materials. This can lead to new applications in various industries.
- Improved Processing Techniques: Advancements in casting and heat treatment processes could enhance the properties of white cast iron, making it more suitable for a wider range of applications.
- Automotive Applications: With the automotive industry constantly seeking materials that offer strength and durability while reducing weight, white cast iron could see increased usage, especially in areas subjected to high stress and wear.
- Recycling and Sustainability: As industries lean towards sustainability, the potential to recycle white cast iron effectively can make it a more attractive option, reducing the environmental impact of new material production.
- Customizable Properties: The ability to tailor the microstructure of white cast iron through controlled cooling and alloying elements opens up possibilities for customizing its properties for specific applications, thereby broadening its usage.
In conclusion, white cast iron, due to its distinct properties and the continuous advancements in metallurgical science, stands as a crucial material in modern industry with a promising future for diversification and enhancement. Its role in wear-resistance applications, cost-effectiveness, and potential for improved properties through research and development mark it as a material of significant ongoing and future relevance.
Chapter 5:Decoding the Microstructure of White Cast Iron
Decoding the microstructure of white cast iron involves a detailed understanding of its unique composition and the factors that influence its properties. Here’s an in-depth analysis:
Basic Composition and Structure
- Carbon and Iron: The primary constituents of white cast iron are carbon and iron. The carbon content typically ranges between 1.8% and 3.6%.
- Carbides Formation: In white cast iron, the carbon exists mainly in the form of cementite (Fe3C), a hard, brittle compound. This is what primarily gives white cast iron its characteristic hardness and brittleness.
- Microstructure Components: The microstructure generally consists of pearlite and cementite, with a very small proportion of free graphite, if any. The rapid cooling rate associated with the casting process of white cast iron leads to the formation of this distinct microstructure.
Influences on Microstructure
- Cooling Rate: The cooling rate during the solidification process plays a crucial role in the final microstructure. A fast cooling rate promotes the formation of cementite over graphite, leading to a harder and more brittle structure.
- Alloying Elements: Alloying elements such as chromium, molybdenum, and nickel can be added to modify the properties. For example, chromium increases hardness and corrosion resistance, while nickel can enhance toughness.
- Heat Treatment: Although white cast iron is generally brittle, specific heat treatments can transform its structure. For instance, annealing can convert some of the cementite into graphite, resulting in malleable iron, which is tougher and more ductile.
Characterizing the Microstructure
- Hardness: The high concentration of cementite imparts significant hardness to white cast iron. This is often quantified using standard hardness tests like Rockwell or Brinell hardness tests.
- Brittleness: The same cementite that provides hardness also contributes to brittleness, making white cast iron less ductile and more prone to cracking under high stress or impact.
- Magnetic Properties: The presence of iron carbides also influences the magnetic properties of white cast iron, which can be a consideration in certain applications.
Applications Based on Microstructure
- Wear-Resistant Surfaces: Due to its hardness, white cast iron is often used in surfaces that require high wear resistance, like the inner parts of ball mills and mixer blades.
- Crushing and Grinding Tools: Its ability to withstand abrasion makes it suitable for use in crusher hammers, grinding rollers, and other tools in the mineral processing industry.
Future Research and Development
- Microstructure Tailoring: Research into controlling the cooling rate and composition to tailor the microstructure for specific applications can expand the utility of white cast iron.
- Surface Treatment Technologies: Surface treatments like carburizing or nitriding can further enhance the wear resistance and service life of white cast iron components.
- Composite Materials: Developing composite materials that combine the hardness of white cast iron with the toughness of other metals could lead to innovative applications.
The microstructure of white cast iron, characterized by its high carbon content and cementite formation, defines its mechanical properties and suitability for specific applications. Understanding and manipulating this microstructure through alloying, heat treatment, and cooling rate adjustments are key to broadening its applications and improving its performance in various industrial settings.
Chapter 6: Understanding White Cast Iron
Understanding white cast iron requires an exploration of its composition, characteristics, and how these factors translate into its modern applications. Here’s an overview:
Composition
- Carbon Content: White cast iron typically contains 1.8% to 3.6% carbon. The high carbon content is critical to its defining characteristics.
- Cementite (Fe3C): In white cast iron, most of the carbon is present as cementite, rather than graphite. Cementite is a hard and brittle intermetallic compound.
- Other Elements: It often includes other alloying elements like silicon (which affects the carbon’s form in the iron), manganese, sulfur, and phosphorus in small amounts. Additional elements like chromium, nickel, and molybdenum may be added to achieve desired properties.
Characteristics
- Hardness and Wear Resistance: The cementite content imparts exceptional hardness and wear resistance to white cast iron, making it ideal for surfaces subjected to severe abrasion.
- Brittleness: It is more brittle than other types of cast iron. This brittleness is due to the presence of cementite, which, while hard, is also quite inflexible.
- Strength: White cast iron has a good compressive strength but poor tensile strength and shock resistance due to its brittle nature.
- Lack of Ductility and Malleability: Unlike other cast irons, it lacks ductility and malleability. This characteristic limits its use in applications requiring shaping or bending.
- Heat Treatment: Through specific heat treatments, white cast iron can be altered to produce malleable iron or ductile iron, enhancing its applications.
Modern Uses
- Abrasive Wear Applications: Its high hardness makes it suitable for industrial applications involving abrasive wear. It is used in parts like the shells of ball mills, slurry pumps, impellers, and liners for grinding machinery.
- Crushing Machinery: In mining and mineral processing, white cast iron is used in making parts for crushing and grinding equipment due to its abrasion resistance.
- Railroad Industry: The wear resistance of white cast iron makes it suitable for certain railroad applications, like brake shoes and couplings.
- Shot Blasting Nozzles: Its hardness and wear resistance make it an ideal material for parts like shot blasting nozzles, which face both abrasion and high-velocity impact.
- Pump and Valve Components: In pumps and valves, especially those handling abrasive materials, white cast iron is used for parts that require high wear resistance.
- Agricultural Implements: Some agricultural tools and machinery, which require resistance to wear and tear, also employ white cast iron.
Future Developments
Ongoing research in metallurgy aims to enhance the properties of white cast iron, like improving its toughness or developing composite materials that combine the benefits of white cast iron with other materials. This will potentially open up new applications and improve its efficacy in existing ones.
In summary, white cast iron, with its high carbon content leading to a hard and wear-resistant but brittle material, finds its niche in modern industry where abrasion resistance is crucial. While its brittleness limits some applications, advancements in metallurgical techniques continue to expand its utility.
Chapter 7: The Scientific Analysis Microstructure of White Cast Iron
The scientific analysis of the microstructure of white cast iron involves understanding its unique characteristics at a microscopic level. This microstructure, which fundamentally influences its physical and mechanical properties, is a result of its chemical composition and the conditions under which it was formed and processed. Here’s a breakdown of the key aspects:
Formation and Composition
- Carbon Content: White cast iron is a carbon-iron alloy containing 1.8% to 3.6% carbon. This high carbon content is crucial in defining its microstructure.
- Cementite Formation: Unlike other forms of cast iron, where carbon is primarily in the form of graphite, in white cast iron, carbon exists as cementite (Fe3C). Cementite is a hard, brittle compound that dominates the microstructure.
- Alloying Elements: Elements like silicon, manganese, sulfur, and phosphorus are present in small quantities. The inclusion of other alloying elements like chromium or nickel can modify the microstructure for specific properties.
Microstructure Characteristics
- Carbide Network: The microstructure is characterized by a network of cementite distributed within a matrix of pearlite or martensite. The exact nature of this matrix can vary depending on the cooling rate and heat treatment.
- Pearlite and Martensite: The matrix in which the cementite is embedded can be pearlitic or martensitic. Pearlite provides some ductility, while martensite increases the hardness and strength.
- Grain Structure: The grain structure in white cast iron is typically finer due to the rapid cooling rate, which prevents the formation of graphite and results in a hard and brittle structure.
- Phase Diagram Analysis: Understanding the iron-carbon phase diagram is crucial for predicting and controlling the microstructure of white cast iron. The cooling rate and composition determine whether the carbon will form cementite or graphite.
Properties Influenced by Microstructure
- Hardness and Wear Resistance: The cementite network provides exceptional hardness and wear resistance, making it ideal for abrasive environments.
- Brittleness: The brittle nature is due to the presence of cementite. White cast iron is more prone to cracking under stress compared to other cast irons.
- Strength: While it has good compressive strength, its tensile strength is low due to the lack of ductility.
- Magnetic Properties: The iron-carbide compound influences its magnetic properties, which can be a consideration in certain applications.
Analyzing Techniques
- Microscopy: Optical and electron microscopy are used to examine the microstructure, revealing details about the distribution and morphology of cementite and the matrix.
- X-ray Diffraction: This technique can be employed to identify the phases present in the alloy, particularly useful for distinguishing between different forms of iron and carbon compounds.
- Hardness Testing: Tests like Rockwell or Brinell hardness tests quantify the hardness, providing insights into the effectiveness of the microstructure for certain applications.
In summary, the microstructure of white cast iron is defined by its high carbon content forming a network of hard and brittle cementite within a matrix of pearlite or martensite. This structure results in a material that is extremely hard and wear-resistant, yet brittle. Understanding and manipulating this microstructure through alloying, heat treatment, and control of cooling rates are crucial for tailoring its properties to specific industrial applications.
Chapter 8: The Role of White Cast Iron in Industrial Machinery
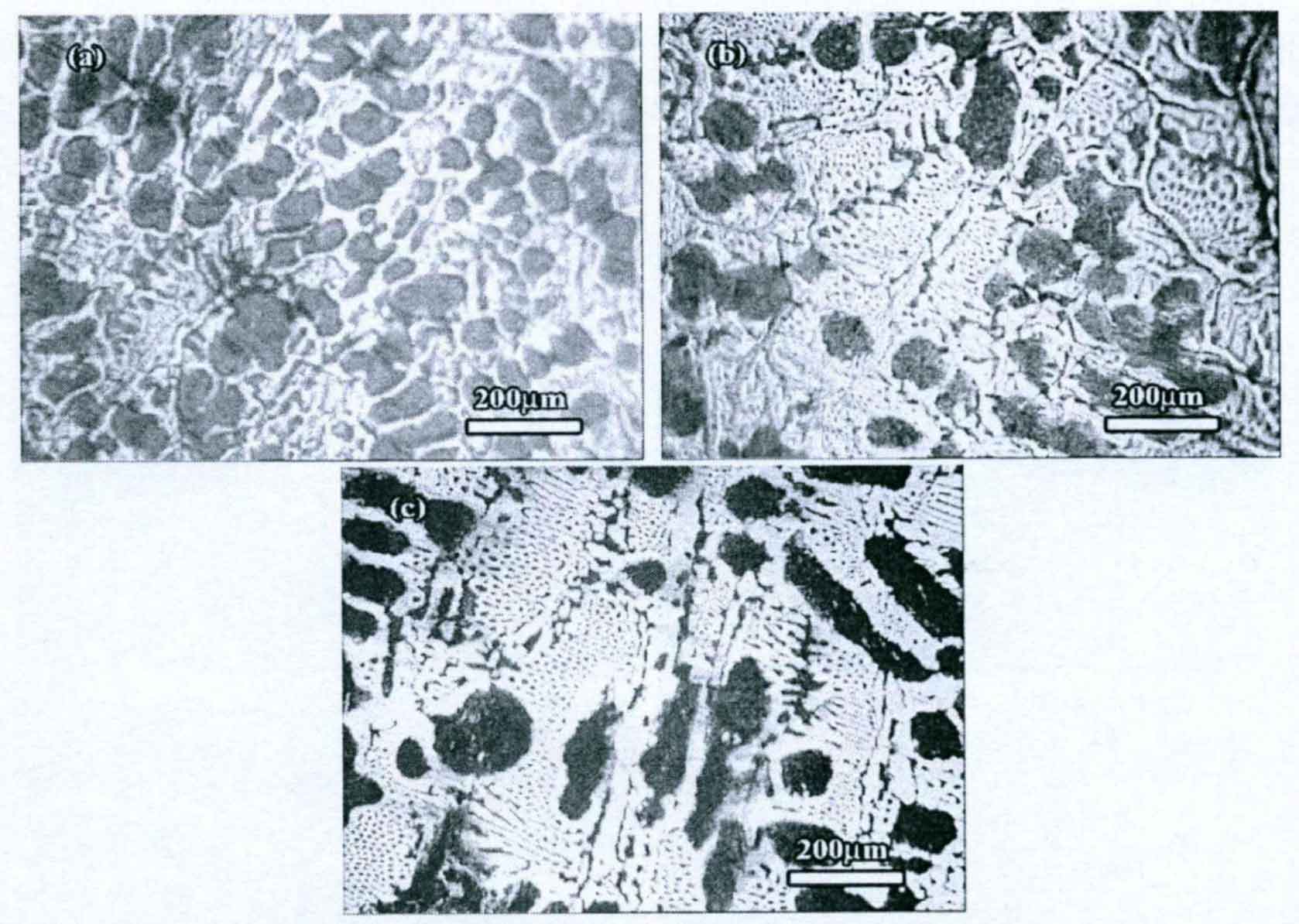
White cast iron plays a pivotal role in industrial machinery due to its unique properties. Here’s an overview of how it is utilized across various industries:
Wear Resistance
- Mining and Ore Processing: In the mining industry, white cast iron is used for parts like crusher jaws, grinding mill liners, and slurry pump parts. Its high hardness and abrasion resistance make it ideal for handling and processing ores, which are typically very abrasive.
- Earth Moving and Construction Equipment: Components like bucket teeth and wear plates in heavy-duty earth-moving machinery are often made of white cast iron. The material’s resistance to wear and abrasion is crucial in these high-impact, soil-engaging environments.
Hardness and Strength
- Industrial Grinding and Crushing: White cast iron’s hardness makes it suitable for grinding media used in ball mills, which pulverize materials in various industries. Similarly, its use in crushing machinery parts, like hammers and crushers in cement plants, illustrates its capacity to withstand significant impact and wear.
- Manufacturing of Cutting and Shaping Tools: Tools for cutting, shaping, or processing hard materials often incorporate white cast iron. Its hardness allows these tools to maintain their shape and sharpness over extended periods.
Durability in High-Stress Environments
- Railway Applications: Components like brake shoes and coupling components in railway systems use white cast iron. Its durability under repetitive stress and resistance to wear make it suitable for the demanding conditions of rail transportation.
- Pump and Valve Industries: Pumps and valves, particularly those used in abrasive environments like mining or chemical processing, often feature components made from white cast iron. Its ability to resist erosion and corrosion is beneficial in these settings.
Cost-Effectiveness
- Automotive Components: Some automotive parts, especially those subjected to high wear like brake disks, can be made from white cast iron. It offers a cost-effective solution due to its long service life and minimal wear.
- Agricultural Machinery: In agriculture, equipment parts that are exposed to high abrasion from soil and rocks, like ploughshares, are often made from white cast iron for durability and cost-effectiveness.
Specialized Applications
- Shot Blasting Equipment: The hardness and abrasion resistance of white cast iron make it ideal for parts in shot blasting equipment, such as the blades that direct abrasive materials at high velocities.
- Metallurgical Industry: In steelmaking and foundry applications, white cast iron components are used in various tools and molds due to their ability to withstand high temperatures and abrasive conditions.
Future Potential
The ongoing development in metallurgical techniques may further enhance the properties of white cast iron, expanding its applicability in industries that require materials with high wear resistance and hardness. Moreover, alloying and heat treatment advancements could unlock new applications and improve performance in existing ones.
White cast iron is a critical material in industrial machinery, valued for its wear resistance, hardness, and durability. It finds widespread use in high-wear environments, from mining and construction to manufacturing and transportation, offering a balance of performance and cost-effectiveness that is hard to match with other materials.