Resin sand casting, also known as the furan sand casting process, is a widely used method in modern manufacturing for producing high-quality metal castings. It involves the use of a mixture of resin and sand as the molding material. This casting process offers several benefits that make it a preferred choice for many industries. Here are some of the key advantages of resin sand casting:
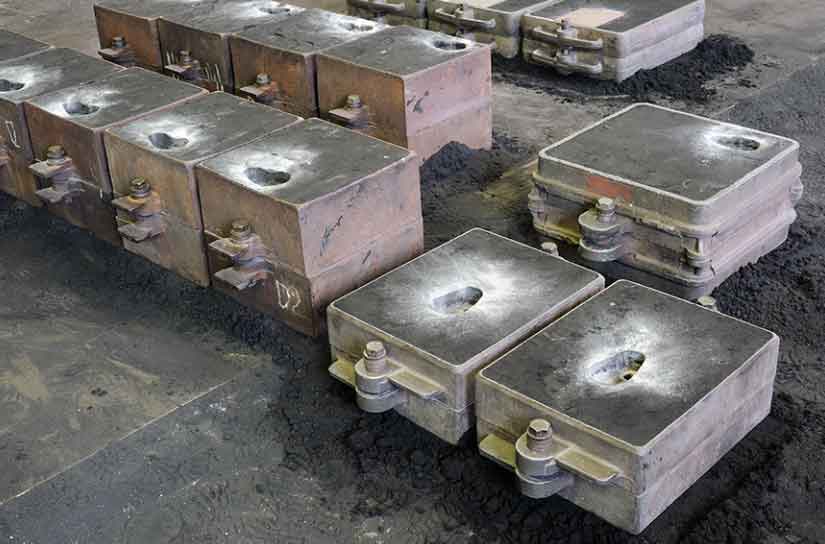
- Versatility: Resin sand casting is a highly versatile process that can be used to produce complex and intricate metal parts of various shapes and sizes. It allows for the production of both small and large castings, making it suitable for a wide range of applications across different industries.
- Cost-effectiveness: Compared to other casting methods, resin sand casting offers a cost-effective solution for manufacturing metal parts. The materials used in the process, such as resin and sand, are relatively inexpensive. Additionally, the tooling costs associated with resin sand casting are generally lower compared to methods like die casting or investment casting.
- Excellent dimensional accuracy: Resin sand casting enables the production of castings with excellent dimensional accuracy. The mixture of resin and sand used in the process has good flowability and can replicate intricate details and features of the pattern or mold accurately. This results in castings with precise dimensions and tight tolerances, reducing the need for additional machining or finishing operations.
- Superior surface finish: The resin sand casting process produces castings with a smooth and refined surface finish. The sand used in the process is fine and tightly packed, allowing for better surface replication. This eliminates the need for extensive surface preparation or post-casting treatments, reducing production time and costs.
- Good mechanical properties: Castings produced through resin sand casting exhibit excellent mechanical properties. The combination of resin and sand results in a robust mold that can withstand the pouring of molten metal at high temperatures. The resulting castings possess high strength, good hardness, and improved resistance to wear, making them suitable for demanding applications.
- Design flexibility: Resin sand casting offers design flexibility, allowing engineers and designers to create complex geometries and incorporate intricate details into the castings. This enables the production of customized and unique parts tailored to specific requirements. The ability to accommodate design changes easily makes resin sand casting suitable for prototyping and low-volume production runs.
- Environmental friendliness: Compared to other casting processes, resin sand casting is relatively environmentally friendly. The sand used in the process can be recycled and reused multiple times, reducing waste generation. Additionally, the use of furan resin, which is derived from renewable sources, contributes to the sustainability of the process.
Resin sand casting provides numerous benefits in modern manufacturing. Its versatility, cost-effectiveness, excellent dimensional accuracy, superior surface finish, good mechanical properties, design flexibility, and environmental friendliness make it an attractive choice for producing high-quality metal castings across a wide range of industries.