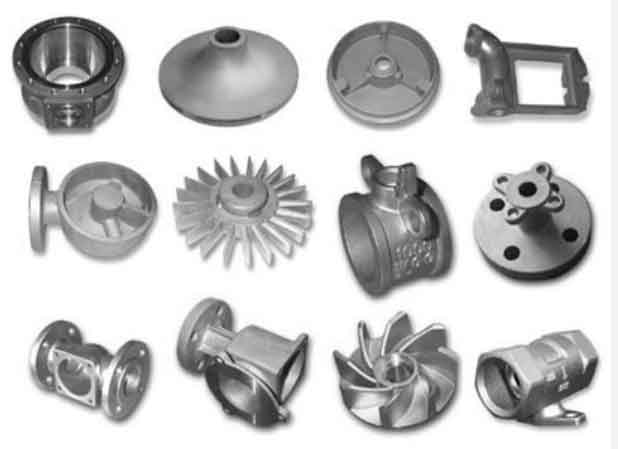
Grey cast iron is a versatile material that exhibits several key properties, which make it suitable for a wide range of applications. Let’s delve into the essential properties and explore some common applications of grey cast iron:
- Composition and Microstructure: Grey cast iron is primarily composed of iron, carbon, and silicon, with small amounts of other elements such as manganese, sulfur, and phosphorus. The microstructure of grey cast iron consists of graphite flakes dispersed in a matrix of ferrite and pearlite. The presence of graphite gives it the characteristic gray appearance.
- Strength and Hardness: Grey cast iron has good compressive strength, making it suitable for applications where components are subjected to compressive loads. However, it has relatively low tensile strength and impact resistance. The hardness of grey cast iron can range from 150 to 300 HB (Brinell hardness).
- Excellent Castability: Grey cast iron has excellent fluidity and can be easily cast into intricate shapes. It has a low melting point and high fluidity when in a molten state, enabling the production of complex components with detailed features. This castability makes it a preferred choice for a wide range of industrial applications.
- Wear Resistance: The presence of graphite flakes in grey cast iron provides effective lubrication, resulting in excellent wear resistance. It is commonly used in applications where components experience sliding or abrasive wear, such as brake discs, cylinder liners, piston rings, and machine tool parts.
- Damping Capacity: Grey cast iron exhibits exceptional damping capacity, which helps absorb vibrations and reduce noise levels. This property is valuable in applications where noise and vibrations need to be minimized, such as machine tool bases, engine blocks, and equipment foundations.
- Thermal Conductivity: Grey cast iron has relatively high thermal conductivity, allowing for efficient heat transfer. It is commonly used in applications involving heat dissipation, such as engine blocks, exhaust manifolds, cookware, and heat exchangers.
- Corrosion Resistance: Grey cast iron is prone to corrosion in certain environments, especially in the presence of moisture and corrosive agents. However, it can be protected by various surface treatments, coatings, or by alloying the iron with other elements to enhance its corrosion resistance.
Common applications of grey cast iron include:
- Engine blocks, cylinder heads, and pistons in the automotive industry.
- Machinery components such as gears, pulleys, and machine tool bases.
- Pipe fittings, valves, and pumps in plumbing and fluid handling systems.
- Brake discs, brake drums, and brake calipers in the automotive and transportation industries.
- Cookware, stoves, and grills due to its heat retention and distribution properties.
- Manhole covers, frames, and municipal infrastructure components.
- Construction applications such as structural supports, bridge components, and building facades.
These are just a few examples, as grey cast iron finds applications in numerous industries due to its unique combination of properties and cost-effectiveness. Its widespread use in industrial engineering is a testament to its importance and versatility.